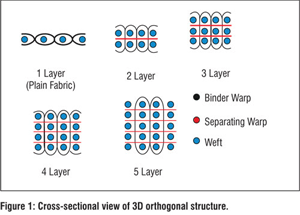
3D fabrics: Performance depends on layers
As the layer increases in a 3D orthogonal structure of 3D fabrics, its performance also increases, but the ratio of binder warp to separating warp should be optimum, infer Dr Uday Patil and Gnanauthayan G.
As the layer increases in a 3D orthogonal structure of 3D fabrics, its performance also increases, but the ratio of binder warp to separating warp should be optimum, infer Dr Uday Patil and Gnanauthayan G.
Textile composite material is one of the promising technologies and its application is tremendously increasing day by day in various fields such as aerospace, marine, automotive, etc. Three dimensional (3D) woven fabric as reinforcement is the backbone of textile composites and becoming popular due to cost saving, high production, nearest shaping and superior mechanical properties. The 3D textile composites have reasonable resistance to crack propagation due to heavy tow interlacement. In addition, they have better de-lamination, toughness, impact damage resistance and post-impact mechanical properties than conventional laminated composites.
Mostly 3D fabrics are manufactured by both conventional weaving principles and specialised weaving systems. In unconventional weaving systems, 3D weaving is usually done by adding another set of yarns in the Z-direction. There is dual direction shedding principle, which is possible between X&Y yarns and XY & Z yarns. By this we can prepare woven fabric with substantially very high thickness compared to the conventional 2D fabrics.
In 3D woven fabrics, generally multilayer, angle interlock and orthogonal weave architectures are the most widely used weave structures. These weave structures can also be produced with conventional 2D weaving machines especially with shuttle looms. Pleated fabrics, terry fabrics, velvet structures, spacer fabrics and shell fabrics are also considered as 3D structures, according to various literatures.
R G Panneerselvam reported that 3D fabrics can also be woven in normal looms as well. According to him, to weave 3D fabrics, it is required to use one series of stitching warp and multi series of separating warp as per the number of layers to be formed. The stitching warp passes from top to bottom and bottom to top but all the separating warp lies almost straight and hence the stitching warp takes up more length than the separating warp. Therefore, the stitching warp is brought from a loose tension beam and the entire separating warp is brought from another normal tension beam.
There are certain parameters which influence the properties of the 3D woven products; most important of them is the crimp of yarn and the weave structure. This has been studied by Mazhar Hussain Peerzada et al, they studied three different structures, layer to layer, orthogonal and angle interlock weaves have been used. Effect of weave has been investigated in both longitudinal (warp) and horizontal (weft) direction. The effect of crimp on failure mechanism was also studied. It is observed that the crimp interchange between the carbon tows and the binder yarn leads to decreasing load over the fibres (warp and weft). As a result, strength and stiffness may be increased. Layer to layer weave structure was found to have higher strength and moduli (in warp) as well as strength as compared to orthogonal and angle interlock weaves.
In this study, 3D dimensional orthogonal structure is constructed using conventional weaving principles. Weft layers ranging from 1-5 is constructed with same thread density per layer. These samples are evaluated for different characteristics which are essential as well as desirable for reinforcements in composite industry.
Materials and methods
The 3D orthogonal structure is constructed using conventional weaving principle with 2/10sNe count spun polyester. The 3D woven fabric manufactured is given in table 1.
The beam density for binder warps (30 EPI) is kept constant for all the samples and for separating warps it is varied from 15-60 EPI. The thread density is designed in such a way that each sheet of