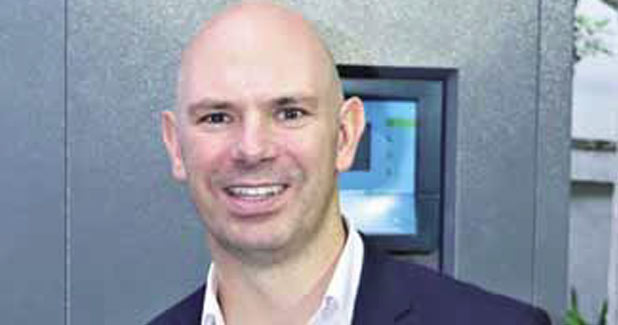
Industry 4.0 is a key focus for Atlas Copco: Latham
Atlas Copco’s Compressor Technique business area provides compressed air solutions; industrial compressors, gas and process compressors and expanders, air and gas treatment equipment and air management systems.
Atlas Copco’s Compressor Technique business area provides compressed air solutions; industrial compressors, gas and process compressors and expanders, air and gas treatment equipment and air management systems. The business area has a global service network and innovates for sustainable productivity in the manufacturing, oil and gas, and process industries.
Conrad Latham, General Manager, Atlas Copco Compressor Technique – India, speaks on the role of compressed air systems in textile industry, and USPs of the technologies Atlas Copco has been offering the Indian textile industry.
Excerpts…
How do you think the role of compressed air systems in textile industry has developed over the years?
The compressed air systems have grown with the growth of textile companies. The use of compressed air in the textile can be generally split into two – air for weaving and air for spinning. In the last few years, we see that the demand for weaving is slowing v/s the demand for spinning. Also, the types of compressors used for spinning are normally oil-injected screw type whereas weaving normally requires high quality oil-free air.
Also, we see that the type of oil-free air compressors changes as the number of looms grows. For smaller cotton weaving customers, the best solution is oil-free screw compressors but as the number of looms grows beyond a threshold limit then the most efficient solution is turbo centrifugal compressors. Of course, a combination of turbo and screw compressors is often seen as the most energy efficient solution.
Whether the application is spinning or weaving the demand of all textiles customers is to reduce their energy costs. It is not uncommon for a textile plant to spend up to 50 per cent of their energy costs on compressed air. Working closely with our customers, Atlas Copco is the only compressor company that can offer every form of compressor technology and drying solutions to maximise the compressed air system for the lowest running costs of all textile companies.
Most of the companies are focusing on digitalisation, Industry 4.0 and energy saving technologies. How have Atlas Copco’s collaborations in compressed air systems contributed to this?
Like all companies, this is a key focus for Atlas Copco. The biggest development over the last couple of years is the implementation of our Smartlink system on all equipment that we manufacture. Presently we have more than 1,20,000 machines connected across the world and more than 10,000 across India. Our customers demand that the data being generated from the compressors and dryers be used to improve their overall productivity and reduce their energy bills. We have been able to prove that by continuous monitoring of a customers’ compressed air system, we can increase their uptime by 16 days a year and stop the compressors running in an inefficient unloaded condition for 22 days a year, which equates to an approximate saving of Rs 5 lakh per year for an average textile plant.
Tell us about the project implementation and service and after-sales service set-ups for compressed air systems segment of the textile machinery division.
Customers are not interested in energy saving if the compressors are not running. Maintaining continuous uptime is the key for all textile companies. So working with Atlas Copco who is a proven service provider with more than 180 direct service engineers and over 700 indirect service engineers across India helps bring peace of mind to our textile customers. Using our unique Smartlink solutions to allow continuous monitoring of the compressed air system and coupling this with our energy managers, we can constantly look for new ways for customers to reduce their energy bills whilst maintaining their maximum uptime.
How do you think compressed air systems contribute to the ultimate quality of end-products? What at present is lacking in industry, and what is your blueprint for improvement for the industry?
It is clear that in the textile industry, quality is an absolute must have. The most important area for compressed air quality is the quality of the air. For example, in cotton weaving, having oil-free air at the correct dew point is paramount for the success of a company. No contamination can come into contact with the cotton if the compressed air is 100 per cent oil-free. The only way to guarantee 100 per cent oil-free air is to use an ISO 8573 class zero certified compressor. Atlas Copco was the pioneer in class zero compressors and now all its Z and AQ models of compressors are certified. Having a certified class zero compressor also increases the uptime of the weaving looms by avoiding any possible oil contamination that my clog the loom, thereby preventing it from running smoothly. Many end users are now insisting that their products be made only using class zero certified compressors.
What is the present share of your technologies in the textile industry? Has it grown and how much?
Unfortunately, this is very difficult quantify as there is no independent body that measures market share in India. It also depends very much on the type of compressor being used.
What are the USPs of the technologies Atlas Copco has been offering the Indian textile industry?
The biggest unique feature we have is our people. With passionate people we know we can deliver fantastic customer service and support. Our whole company is focused to find the best, most sustainable and efficient solutions for our customers. We invest constantly on competence development to bring the best customer experience and learn continuously from our successes and failures. From a product innovation we believe our hybrid solution of centrifugal and oil-free screw compressors bring the lowest energy bills to our textile customers and when this is coupled with our unique MD drying technology, our Airnet piping solution and our Optimizer 4.0 central controller we believe that no other compressor company can offer such innovation so focused to reduce the energy bills of our customers.
Atlas Copco is known for its strength in after-sales? How is the establishment placed in this aspect?
We have more than 300 direct employees focused on our after-market. We have placed a lot of investment in this to improve the customer experience. We want our customers to have the very best service locally provided to them. We have spread ourselves across India and have maintained a ratio of 50 customers to one field service engineer. We believe that the investments we have made in dedicated after-market competence development, our innovation planning software and quick reporting system, provide a customer experience second to none.
What are your suggestions to give a boost to this revolutionary concept of Make in India? What are Atlas Copco’s contributions?
Atlas Copco has been making in India since 1960 and is happy to celebrate its 60 years this year. We continue to invest in new product development and are working constantly on products that can be exported as well. We have three production facilities in Pune and a Global Engineering and Competence Center that is providing world class support to almost every Atlas Copco Division globally.
How do you look at the future of the compressed air systems in textile industry in India? What are the strategies and new proposals to strengthen?
Atlas Copco will continue to listen to its customer’s needs and work to provide them the very best service and experience. We are constantly driving innovation with the single mission to reduce the energy bills of our customers. We know how important energy efficiency is for all textile companies is and that the survival of the textile industry is driven by continuous cost reductions. We endeavour to support our customers and future customers to find the best compressed air solutions for them and to make sure that they are as productive and as profitable as they can be.
This is my first time pay a quick visit at here and i am really happy to read everthing at one place horse racing live coverage
Nice post. I learn something new and challenging on blogs I stumbleupon on a daily basis. where to stream afrobasket live streaming
… [Trackback]
[…] Find More on that Topic: indiantextilejournal.com/industry-4-0-is-a-key-focus-for-atlas-copco-latham/ […]