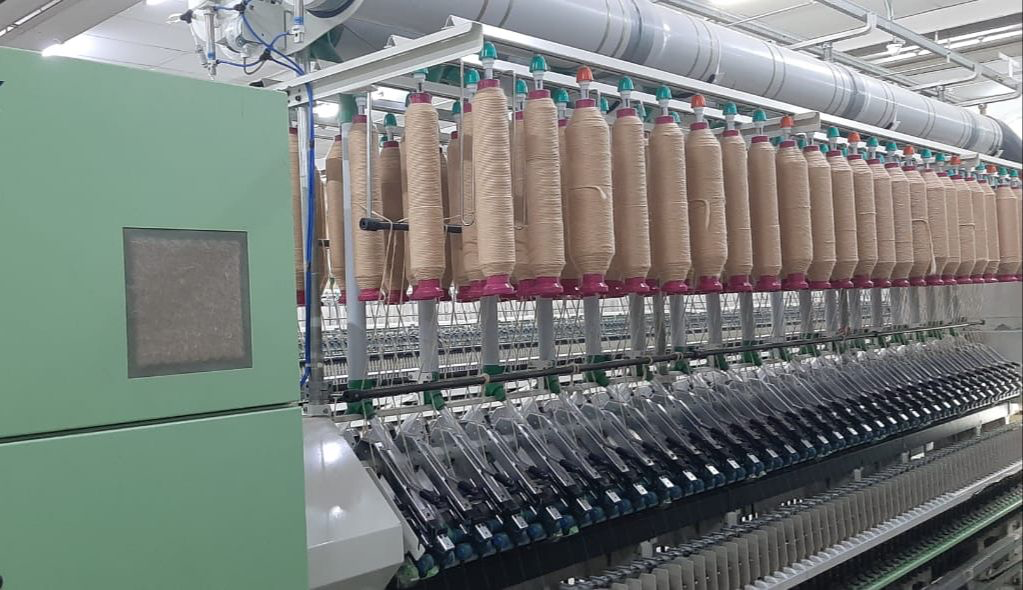
Compact spinning technology: A new twist to naturally coloured cotton
Textile industries are compelled to revisit historical and ecological natural fibres, informs Dr S Venkatakrishnan and K M Saravana Murali.
The urgency of sustainability has become more pronounced in recent years across the globe, textile Industries are actively seeking natural materials with minimum ecological impact to address environmental, economic and social concerns. While natural fibres inherently have a low environmental impact, the use of fertilizers, pesticides and harmful chemicals during production can compromise their eco-friendly status.
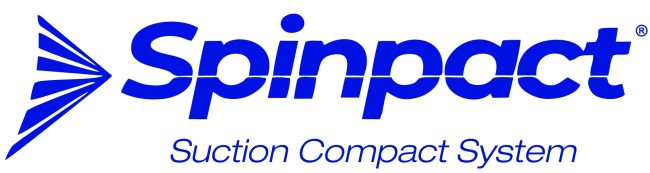
Introduction
The early 20th century witnessed a significant shift with the advent of synthetic fibres, rapidly capturing a substantial market share. However, this coincided with a growing awareness of environmental issues and legislation, leading customers to resist synthetic fibres. Consequently, textile industries were compelled to revisit historical and ecological natural fibres. Eco-farming emerges as a production system advocating for the maximal use of organic inputs while discouraging synthetic agro-inputs. This approach aims to maintain soil productivity, fertility, and pest management within the framework of sustainable natural resources and a healthy environment.
Coloured cotton is receiving increasing importance in view of their eco-friendly character. The urge for eco-friendly cotton can only be fulfilled preferably by organically grown coloured cotton by avoiding harmful chemicals in dying and processing. Coloured cotton is not a product of any recent genetic engineering or biotechnology. Several lint colours (brown, black, mahogany red, khaki, blue, green, dirty white and white) are found in the four species of the genus Gossypium.
In recent years, there has been a rising demand for garments made from organically grown, naturally coloured cotton lint, particularly in developed countries. India is on the verge of commercially cultivating coloured cotton lint, ranging from light to medium brown, aligning seamlessly with the principles of eco-farming. Anticipated to fit well within this sustainable system, coloured cotton lint is poised to garner increased attention from textile and apparel industries to produce eco-friendly functional fabrics and garments.
Factors influencing the quality of yarn, fabric and final products
The quality of the end-product is not solely determined by the inherent properties of the fibres, it is also heavily influenced by the processing conditions and the diligence exercised throughout the entire processing cycle. Achieving the full potential of fibre properties in yarn and fabric poses challenges in practice, given the diverse array of factors at play, including processing sequences, parameters, conditions, and the type of equipment utilised.
Vigilant and continuous monitoring of processing parameters throughout the entire production cycle for ensuring the consistent production of high-quality products. A comprehensive exploration of modern manufacturing practices, encompassing equipment, processing conditions and emerging trends aimed at elevating the value of cotton yarn and fabrics, is imperative. Presently, China stands as the foremost producer of coloured cotton and is renowned for its prowess in spinning and weaving processes. Meanwhile, in India, noteworthy strides have been made with the development and registration of medium brown cotton genotype DMB-225, dark brown cotton genotype DDB-12, and green cotton genotype. DGC-78 at ARS, Dharwad, acknowledged by the National Bureau of Plant Genetic Resources (NBPGR) during the year 2012-13 .
History and background
Humanity has been cultivating and using naturally coloured cotton since 2500 BC, as documented by earlier researchers. In India, brown linted varieties from the Gossypium arboretum L species, specifically Cocanada 1, Cocanada 2, and Red Northerns, were commercially grown on black soils in rainfed conditions in parts of Andhra Pradesh. However, these coloured linted varieties faced challenges such as low productivity per unit area, poor fibre characteristics, nonuniform colours and the inability to be spun on machines for commercial textile production. Growers were also concerned about contamination with white cotton in the field, at the Gin and during transportation.
Benefits
- Naturally coloured cotton eliminates the need for artificial coloration, as it contains natural pigments (condensed tannin) in the fibres lumen that imparts colour as it grows and matures. The brown colour, which is more obvious in the longitudinal view and darker in the lumen area, since the pigment tannin is concentrated in the lumen, and which is responsible for the brown colour.
- Growers of naturally coloured cotton may require fewer pesticides due to its inherent insect and disease-resistant qualities, along with drought and salt tolerance.
- Naturally coloured cotton is inherently flame retardant, with higher limiting oxygen Index (LOI) value compared to conventional white cotton.
- Exhibits excellent antibacterial and UV protection properties.
- Provides an extremely soft hand-feel due to higher wax content compared to white linted cotton.
Concerns
- Growers remain worry of contamination with white cotton in the field, at the Gin and during transportation.
- Limited colour shades
- Faces challenges of low yield and poor fibre quality attributes
- Limited availability of seeds poses a concern.
- Identifying isolated areas in different pockets of states: for commercial cultivation.
- Lack of dedicated ginning and spinning units increases the risk of contamination.
- Absence of appropriate manufacturing procedures.
- The domestic market lacks a fixed price for the produce due to limited cultivation.
Materials and methods
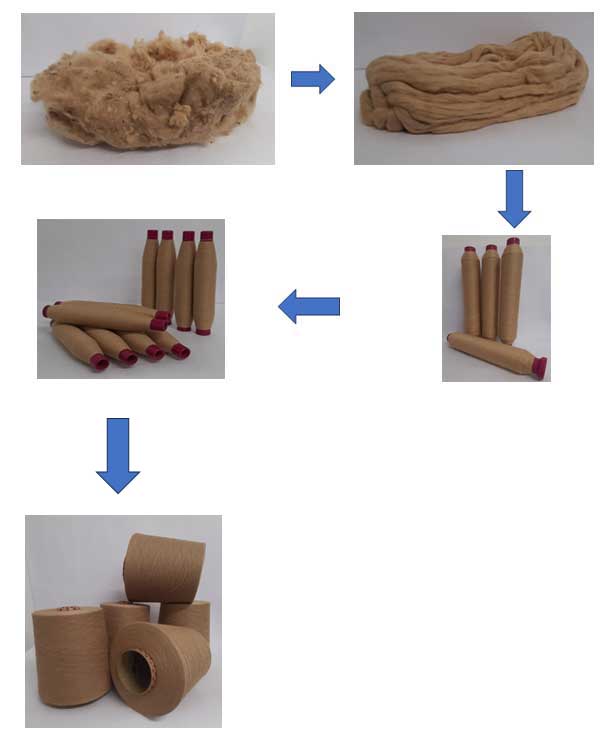
Our study focused on the utilisation of medium brown cotton genotype DMB-225, which was developed at ARS, Dharwad, and registered at the National Bureau of Plant Genetic Resources (NBPGR) in 2012-13. Additionally, dark brown cotton genotype DDB-12 and green cotton genotype DGC-78 were also developed at ARS, Dharwad during the same period. For this research, we specifically chose the medium brown cotton DMB-225, and cultivation was undertaken through a contract farming arrangement facilitated byKandu based in Bengaluru. This involved collaboration with selected group of farmers within designated pockets in Karnataka. The harvested cotton underwent on-site processing, including ginning. Subsequently, the extracted seeds were carefully crushed with stringent measures in place to prevent any unauthorised removal from the contract farming area. The harvested lint (four bales) of brown cotton brought by Kandu was processed in the LMW- Dr DJ R&D Centre in Coimbatore. We employed ring and compact spinning technology after analysing the fibre quality attributes. Yarns of three different counts, Viz: 12s, 16s & 20s Ne were spun in Ring spinning – both Non-compact and Compact systems. The quality of the yarn produced were thoroughly analysed, and based on the results, decided to process only 20s Ne in compact system. Throughout the production process, we conducted.
comprehensive evaluation of material properties to ensure and maintain quality. The following measurements were carried out at various stages:
- The Input and output materials were collected from the processing machines and tested for its fibre quality attributes in Uster AFIS instrument.
- The quality of 12s, 16s & 20s Ne yarn produced from ring (noncompact) & ring (compact) were analysed for different yarn quality parameters in Uster Instruments.
The identified fibre quality attributes led to the adoption of specific blow room and spinning preparatory machineries, along with optimised sequences. Throughout the process, machine parameters were fine tuned to ensure optimal output quality, while minimising waste extraction.
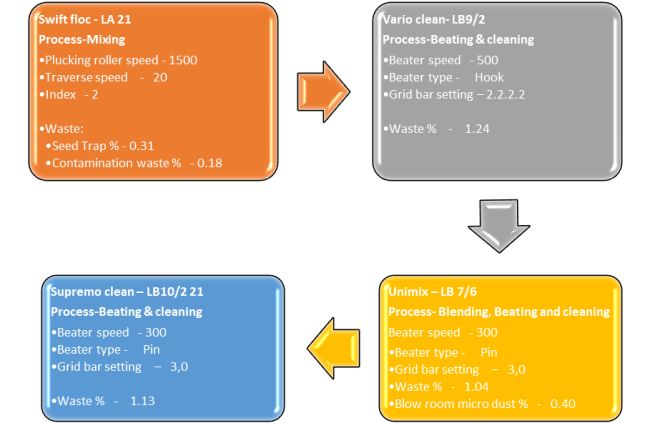
Flow chart 1: Blow room process
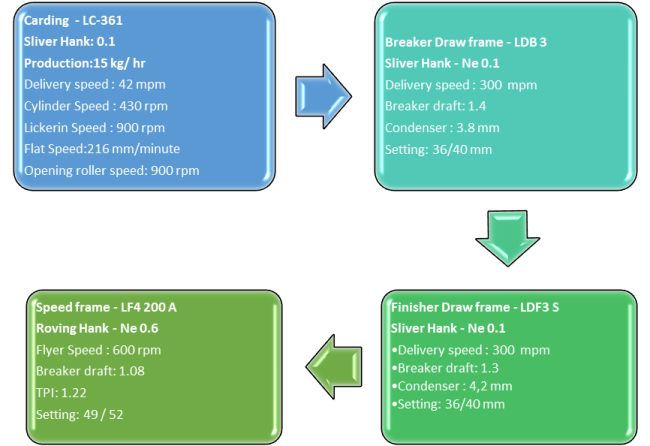
Flow chart 2: Preparatory process
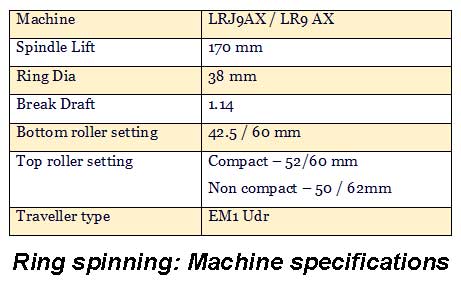
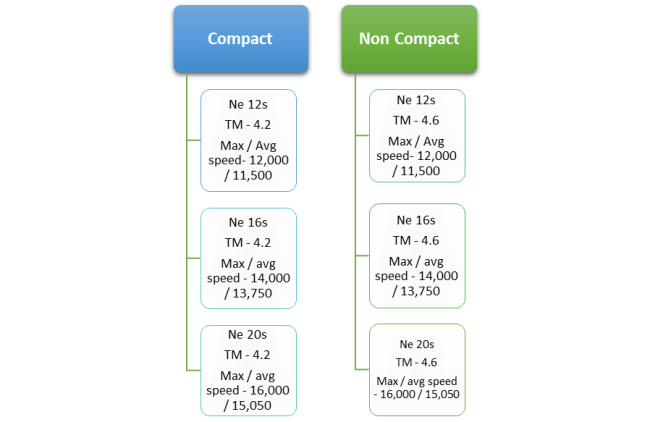
Ring spinning – Process parameters
Results & discussion
Flowchart 1 & 2 depict the blow room preparatory process method, machineries used, and the optimised process parameters and sequences employed in this study. Typically, 3 per cent waste in the blow room and 8 per cent waste in the carding process are expected based on the presence of trash and foreign matters in the incoming cotton. However, due to elevated trash levels, 4.50 per cent waste is extracted in the blow room, and 12.57 per cent in the carding process. The histogram in Figure 1 illustrates the percentage of trash extracted and lint present at each stage from mix to card delivery.
Despite the initial high trash content in the input material, the card delivery sliver is remarkably free of trash, containing 99.6 per cent lint. The higher wax content in the naturally coloured brown cotton, compared to normal white cotton, facilitates the thorough removal of trash. Moreover, the process parameters are meticulously set to preserve the inherent fibre properties during trash removal at each preparatory stage. Figure 2 displays the HVI measured fibre attributes at different stages, revealing a slight improvement in upper half mean length and strength (3.4 per cent & 5.1 per cent, respectively) in card sliver compared to mixing. All other fibre properties remain unaltered from mixing to card sliver (Figure 2).The fibre attributes evaluated by AFIS at different stages of spinning preparatory process are shown in Figure 3.
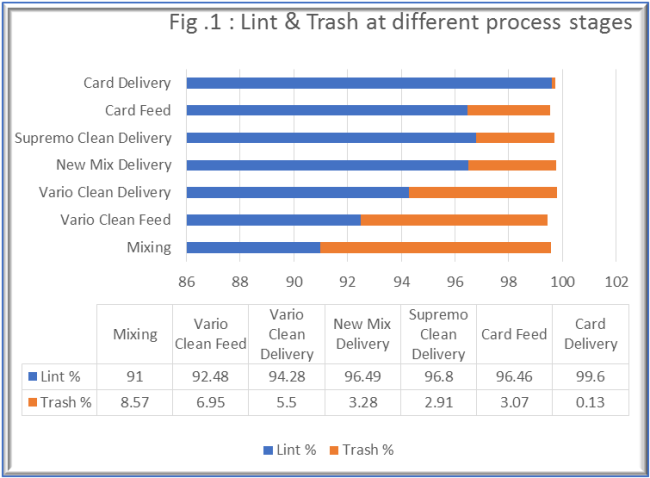
Figure 1: Lint and trash at different process stages
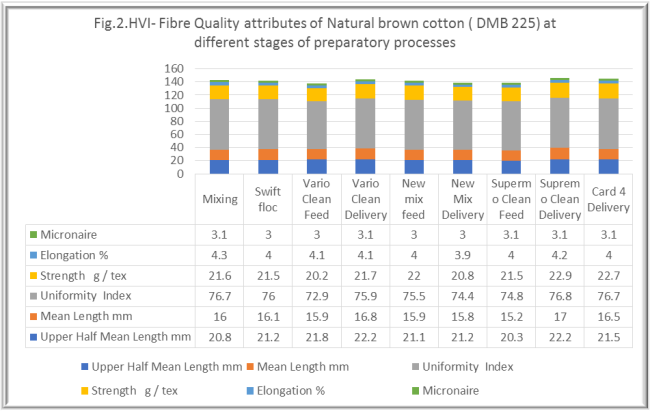
Figure 2: HVI-Fibre quality attributes of National brown cotton (DMB 225) at different stages of preparatory processes.
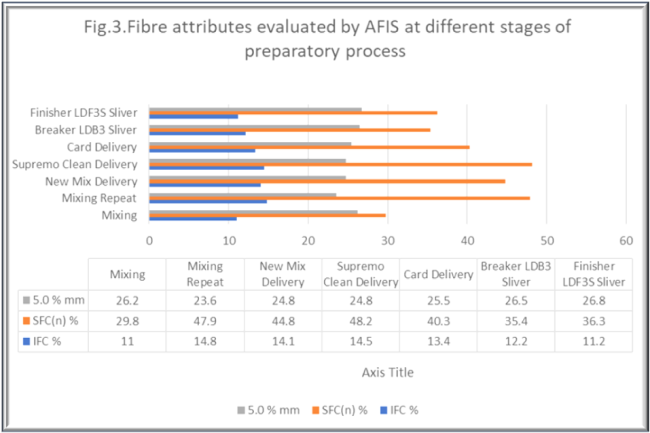
Figure 3: Fibre attributes evaluated by AFIS at different stages of preparatory process.
In the preliminary stages of preparation, the proportion of short fibres tends to rise as weaker immature fibres break during beating. You will observe a simultaneous uptick in the immature fibre content up to the card feed. During card processing, the majority of these broken, immature fibres are discarded as card waste. The finisher draw-frame sliver, in turn boasts an impressive 90% mature fibres with an AFIS 5 % length reaching up to 26.8 mm. This accomplishment is primarily attributed to the thoughtful selection of machineries and the optimisation of process parameters. The performance of card, breaker draw frame, Finisher draw frame delivery slivers and speed frame roving were assessed in UT-6 for U%. CVm 1m%, and CVm 3m% with the results falling within the satisfactory range (Table1)
Table 1: Card & Draw-frame sliver U % measured by UT6
U% Results | CARDING | BREAKER DRAW FRAME | FINISHER DRAW FRAME | SPEED FRAME |
Sliver U% | 3.09 | 3.05 | 3.47 | 4.73 |
Cvm 1m % | 3.11 | 1.73 | 0.41 | 1.28 |
Cvm 3m % | 2.86 | 1.63 | 0.21 | 0.83 |
Yarn quality parameters of non-compact & compact ring yarn
The quality standards for yarn differs based on its intended use in either weaving or knitting for fabric production. Key quality parameters include tenacity (RKM value) CSP (count strength product), elongation and imperfections (measured as U %, thick & thin places). These parameters are crucial for both weaving and knitting and are influenced by factors such as fibre quality attributes, processing machineries, spinning methods and the specific process parameters set on each machine in the production line. In this study, process parameters are determined based on fibre attributes and the yarn count to be spun (Process flow chart:2).
Note: The comparison between Compact and Non-compact yarn is discussed here as there is no data available for Carded Compact yarn in Uster Statistics for bench marking.
Tenacity & elongation
For all the three counts studies (12s,16s & 20s Ne), the tenacity of Compact yarn surpasses that of non-compact yarn, as expected. The highest tenacity value of 15.36 (Cn/tex) is achieved for 20s Ne compact yarn (Chart 1). A similar trend is observed in CSP values, with compact yarn outperforming non-compact yarn. In the case of non-compact yarn (Chart 2).
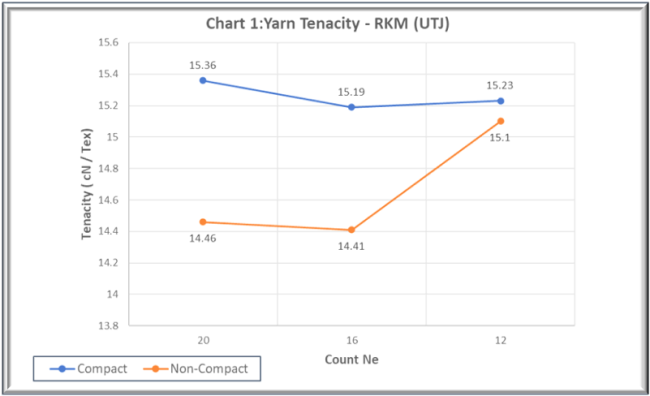
Chart 1: Yarn tenacity – RKM (UTJ)
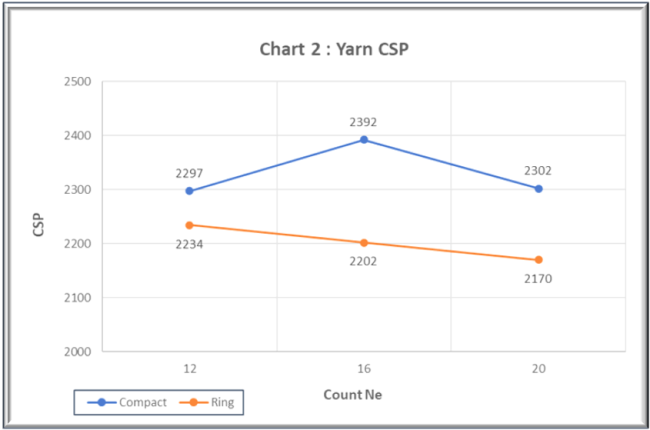
Chart 2: Yarn CSP
Yarn Unevenness (U%)
In the context of U%, a higher value signifies greater “unevenness”, while a lower U % indicates greater yarn “evenness”. In this study, non-compact yarn exhibited higher U % values across all three counts (12s, 16s & 20s Ne) compared to compact yarn. Compact yarn demonstrated lower U% values for all three counts (12s,16s &20s Ne), with the yarn displaying greater evenness in the 12s Ne and 16s Ne counts as compared to the 20s Ne count (chart 3).
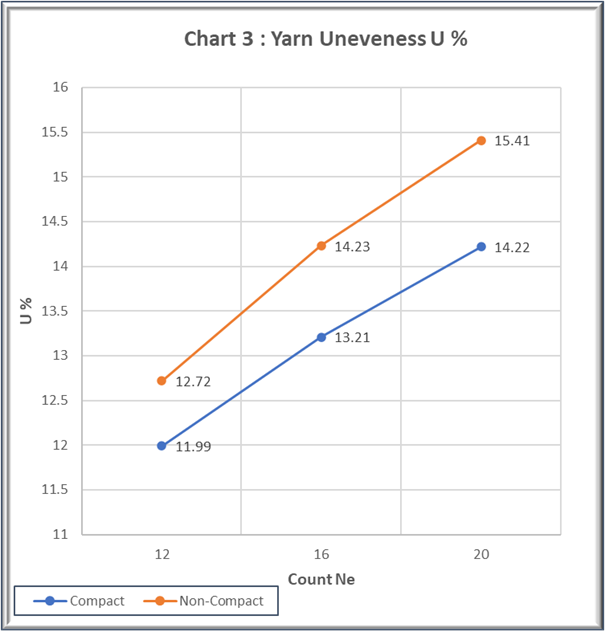
Chart 3: Yarn unevenness U%
Imperfections in yarn
Prevalence of thin & thick places: For all the three yarn counts analysed (12s,16s and 20s Ne), non-compact yarn exhibits a higher prevalence of thin places (– 50%) per kilometer of yarn compared to compact yarn (refer: Chart 4).
Conversely, the occurrence of thick places (+50%) per kilometer of yarn is more pronounced in non- compact yarn for all three counts (12s,16s and 20s Ne) when contrasted with compact yarn (refer: chart 5).
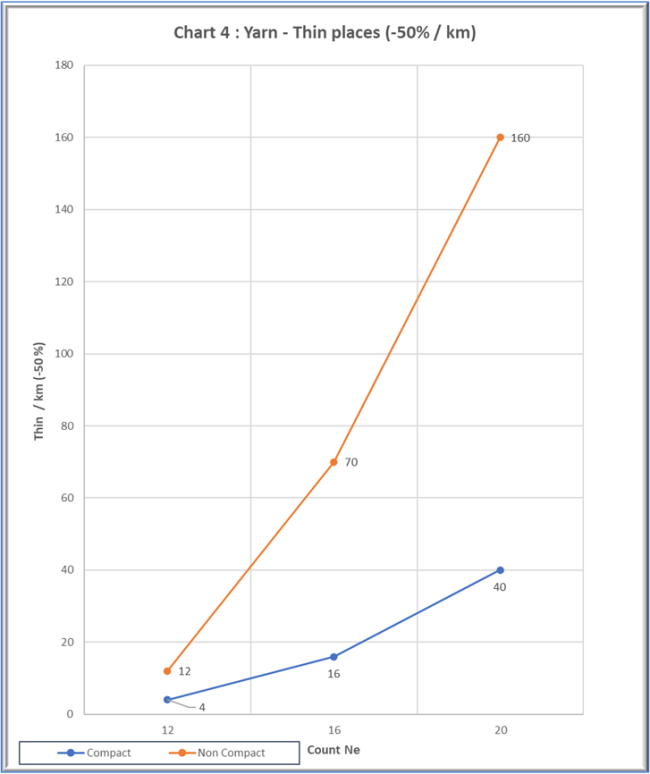
Chart 4: Yarn-Thin places (-50%/ km)
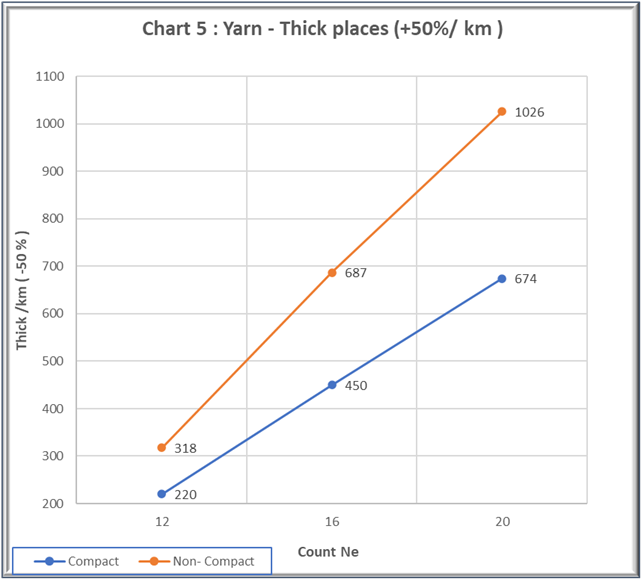
Chart 5: Yarn-Thick places (+50%/ km)
Conclusion
- The present study opens up the possibilities of machine spinning (Ring-Compact) of short staple “Naturally Coloured Cotton” with yarn quality suitable for Knitted fabrics.
- Its suits very well for running in modern knitting machines to produce high-quality knitted fabrics.
- Further the studies confirm that, the thoughtful selection of preparatory machineries, sequences and optimisation of parameters leads to complete elimination of broken immature fibres and able to produce finisher sliver having AFIS 5 per cent length upto 26.8 mm , maturity ratio 0.81 and strength 22.7 g/tex.
- By proper preparatory process and optimisation, it is possible to achieve up to 5 per cent increase in finisher sliver fibre strength without any additional combing process and due to this improvement in the sliver qualities, higher tenacity is achieved in the yarn produced from compact process.
- This work confirms the possibility of spinning the naturally coloured medium brown cotton (DMB 225) into 16s and 20s Ne count yarn in Ring-Compact spinning system with required quality levels without many difficulties by adopting the above manufacturing procedures.
- This work confirms the viability of incorporating naturally coloured cotton into textile production due to its well-established machineries selection, optimised process parameters and reported functional attributes, advantages and diverse end uses.
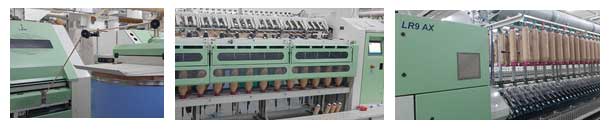
Note: To evaluate the excellence of “short staple naturally brown coloured” yarn produced using carded sliver through the ring- compact system, the resulting yarn were subjected to rigorous testing using an array of Uster Instruments and the test outcomes were then compared with the Uster statistics-2023, with minor modifications to the standard to accommodate the unique characteristics of naturally coloured short staple brown cotton with a UQL below 25 mm. It’s worth noting that the existing Uster standard pertains to a minimum fibre length of 25 mm and above, leaving no specific guideline for carded 20s Ne compact yarn and the current compact yarn standards exclusively cater to combed sliver.
References
- Bhatt Pooja., “Naturally coloured cotton”, Journal of Eco-friendly Agriculture, vol:14, issue:2, 2019 (P82-83)
- Manjula.S.Maralappanavar., “ Genetic Improvement and registration of naturally coloured Gossypium hirsutum cotton genotypes suitable for textile industry” , J.Cotton. Res. Dev.27, July, 2013 (P157-164)
- G.Hustvedt and P.C.Crews, “The ultraviolet protection factor of naturally pigmented cotton , J.cooton.Sci., 2005, 9, 47.
- S.Hua, X.Wang,S.Yuan,M.Shao,X.Zhao,s.Zhu and L.Jiang, Characterization of pigmentation and cellulose synthesis in coloured cotton fibres, Crop Sci.,2007, 47,1540-1546.
- Fox.Sally., “Naturally coloured cotton”., Spinoff,March,1987(P29-37).
- Lee.J., “ A new spin on naturally coloured cotton”., Agricultural Research Magazine, April, 1996, 44.4 (P20-21).
- Veerland,Jr.,James.M.,“Coloured cotton: return of the native.” International Development Research Center Reports, 10 (2), (P4-5).
- Van Zandit., “Development of fabrics from Foxfibre naturally coloured cottons(coyote and buffalo) and evaluation of flame resistant characteristics” , Unpublished masters thesis., Texas Tech University, Lubbock, Texas.
- Y.H.Xiao,Z.S.Zhang,M.H.Yin, M.Luo,X.B.Li.Hou and Y.Pei, Cotton flavonoid structural genes releated to the pigmentation in brown fibres, Biochem.Biophys. Res.Commun., 2007, 358, 73-78.
- T.Li,H.Fan,Z.Li,J.Wei,Y.Lin and Y.Cai,”The accumulation of pigment in fibre related to proanthocyanidins synthesis for brown cotton, Acta Physiol.plant.,2012, 34, 813-818
About the authors:
Dr S Venkatakrishnan is a Freelance Fibre & Textile Consultant in Coimbatore. He holds a degree of M.Sc., Ph.D., A.T,A.,F.T.A. in Textile Technology.
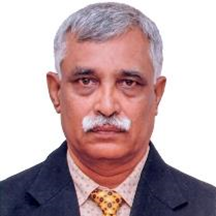
KM Saravana Murali works at the R&D department of Lakshmi Machine Works. He has done a B Tech in Textile Technology.
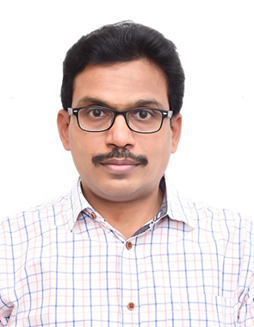