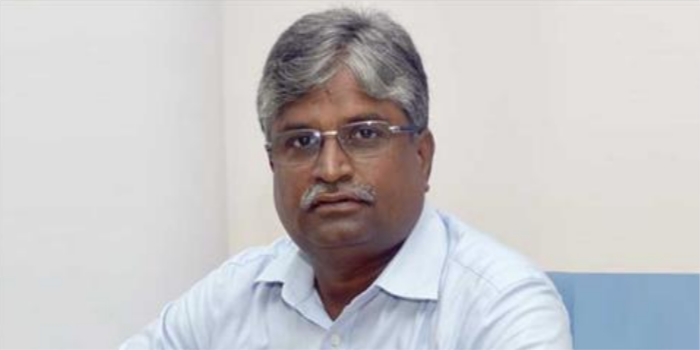
Automation is important for Indian spinning industry
In this interview, C Kamatchisundaram, VP - Textile Machinery Division (TMD), Voltas Ltd, explains the importance of modern technologies for Indian spinning industry for maintaining productivity at highest levels.
Today, Indian
spinning industry faces a daunted task of producing high quality yarn
cost-competitively and by using least resources. In this interview, C Kamatchisundaram, Vice
President – Textile Machinery Division (TMD), Voltas Ltd, explains
the importance of modern machinery and technologies for spinners for
maintaining productivity at highest levels.
How is Voltas serving the Indian spinning industry?
Voltas has been present in the
textiles industry for over 6 decades now and is probably the single most
valuable resource supporting the industry on a continuous basis. We represent
more than 30 principals, offering end-to-end products and solutions across the
gamut of spinning and post-spinning needs. These alliances have not only helped
Voltas’ Textile Machinery Division (TMD) to offer the state-of-the-art
technologies to the market but also services that go beyond the customer
expectations.
Voltas offers the entire range of
products needed for the spinning industry. Our key Principal in the spinning
industry is Lakshmi Machine Works (LMW), who is a global leader in spinning
machinery industry. LMW is one of the only three manufacturers in the globe who
offer the entire range of spinning machinery from Blowroom to spinning. LMW
offers cutting edge technology products and solutions, which caters to the
needs of different segments in the industry irrespective or the size. More than
60 per cent of the investment in the Indian spinning industry takes place
through equipment manufactured by our Principal LMW. It is quite pertinent to
mention here that more than 70% of the yarn produced in the country is through
the machinery supplied by LMW.
We have a comprehensive product suite of accessories and the replaceable
needed for the spinning industry. We offer ring travellers from our Principals
Lakshmi Ring Travellers (LRT) and card clothing needed for the carding machines
from Lakshmi Card Clothing (LCC). Both LRT and LCC are leaders in their
respective field, serving the customers for more than five decades.
We also offer specialty lubricants from Klueber, which not only enhance the
lubricant cycles but also improve the performance of the machinery. In
addition, we offer various other allied machinery
How is Voltas helping Indian spinners to overcome
manufacturing challenges?
The
major need of the customers is to produce quality yarn at the highest
productivity levels at competitive cost and using least resources. Our
Principals LMW offer the smart series of machinery to meet all the above needs.
The smart series of machinery from LMW employ innovative technology, have built
in automation and built with user friendly features enabling customers reduce
the dependence on labour. These machineries have set new benchmarks on
productivity, quality of yarn, power conservation, resource needs etc.
The
smart and capable engineers of Voltas add further value to the customers by
supporting in them in all sphere of activities in the operation of the mills.
While cotton-based value chain dominates the Indian
textile industry, the Government of India (GoI) aims to increase the
contribution of manmade fibre (MMF) based textile products in the industry.
What kind of opportunities will this shift offer to spinning
technology/solution providers like Voltas?
The
Indian textile industry is majorly cotton focussed at a rate of 60:40 for
cotton and synthetic. If we exclude synthetic filaments and look at the ratio
only based the products made from fibres, the ratio would be further skewed in
favour of cotton at 75:25. Accordingly, the export of garments and apparels
from India is mainly cotton based. The GoI and the Indian textile industry have
realised the need to increase its focus on the export potential in the
synthetic sector to improve the global market share.
The GoI
has announced Production-Linked Incentive (PLI) scheme with an outlay of Rs 10,000
crore to promote manufacturing and export of synthetic textiles and technical
textiles. The ‘Make in India’ programme is expected to gain further momentum in
synthetic textiles. Hence, we opine that investments in synthetic textile
manufacture would accelerate in the coming years. This will bring along good
opportunities for Voltas, as the company is favourably positioned to encash on
it. Voltas’ strategy to offer both capital equipment and after sales has helped
it become a ‘one-stop’ solution provider. The company’s comprehensive portfolio
of products and solutions add weightage to its services. For example, the
spinning machinery offered by our Principals LMW is the most favoured by the
manmade yarn spinning mills in the synthetic clusters like Bhilwara and
Hyderabad. We already have a good inflow of enquiries for investments in
synthetic textile manufacture and we have also finalised quite a no of orders
including megaproject for synthetic yarn manufacture in Western region.
The
card clothing offered by our Principals LCC and the ring travellers offered by
LRT are the most preferred options by manmade yarn producers. Similarly, the
circular knitting machines offered by our principals Terrot is the preferred
machine for manufacture of Active wear products across the globe and hence any
new investor in active wear manufacture in India would obviously look at Terrot
as the first choice. We are already in advanced level of discussions with few
players for investments in active wear.
Automation and digitalisation are gaining across the
textile industry. How is Voltas with its array of solutions and technologies
helping the textile mills in India in their journey towards modernisation?
Once considered limited
only to handicrafts, textiles have now become a highly urbane, scientific
and engineering activity of new types of fibers and technologies. A wave of
innovation that has hit the textile industry is the coming of Industry 4.0 –
automation and introduction of artificial intelligence in the textile machinery
sector.
The Industry 4.0 is a very
generic term. If you have to classify the activities that go in to Industry
4.0, then it is automation, which includes robotics. The second part is remote
monitoring of the equipment through networking (which is IIoT), which includes
predictive analysis and collect a wealth of data on performance (which is
called big data). The third but most important part is to use analytics and
artificial intelligence to derive insights from the big data and rapidly
deploying corrective/preventing actions for improvement. The fourth part is to
digitize the designs/ product samples through virtual samples to manufacture
customized products. The fifth part in Industry 4.0 is how we make the business
transaction happen leveraging technology to reduce the cycle time of purchase
and to enhance the purchasing experience. These could be online quote
generation, online order placement, online tracking of the orders, etc. The
above are few examples and the opportunities to leverage Industry 4.0 are
abundant.
Our Principals, LMW, has
been a front runner in offering Industry 4.0 solutions. In fact, LMW was the
first to offer automation for ring frames, speed frames and automatic transport
of material from the blowroom to the carding machine. Automation has become an
integral part of the spinning industry today. If a spinning industry is not
invested in automation, it is going to be difficult to sustain, going forward.
As you know, availability of
labour is a major problem and with the second wave of COVID-19, the industry
may see an exodus of migrant labour. This has made the industry to look at
automation as a solution. It is not something which is good to have, but it has
become a need of the hour. In monitoring and controlling the equipment through
IIoT, LMW was the first to offer networking of the entire plant. The current
state of IoT allows the investors to monitor the power consumption as well. Similarly,
LMW was the first to introduce “Online ordering of parts and components†and it
was launched before a decade. It is pertinent to mention here that more than
90% of the orders received by our Principals LMW now are through the aforesaid
system.
Our principals in knitting,
processing and finishing sectors also have made tremendous strides in serving
the customers leveraging Industry 4.0. Nevertheless, it is continuous journey
and expected to make huge changes in the way a plant is designed, monitored,
managed and controlled to achieve the business goals.
What are the emerging trends in spinning technologies?
A variety of new spinning
technologies have been introduced to in the past few years to match up with the
technology of ring spinning. Interestingly, the ring spinning remains unmatched
in terms of quality and continues to dominate the markets.
Air-jet spinning and
friction spinning are used in specific markets, while the open-end rotor system
has been quite popular in spinning of coarse counts. This can be attributed to
these systems obtaining tremendous increase in the production as compared to ring
spinning. Our principals LMW are in advanced stages of an innovative and high
technology Airjet spinning machine to the market.