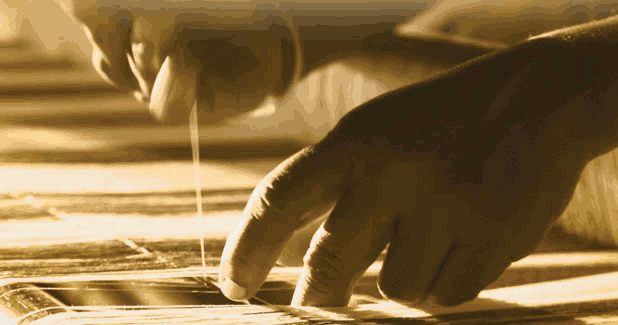
Weaving A SPELL!
Make in India initiative, launched a couple of years ago by the Modi Government, has also caught the serious attention of the textile industry, which seemed to have progressed well on this front. The ITJ takes a closer look with some highlights from the current scenario.
Make in India initiative, launched a couple of years ago by the Modi Government, has also caught the serious attention of the textile industry, which seemed to have progressed well on this front. The ITJ takes a closer look with some highlights from the current scenario.
Gottfried Abrell, CEO of the Swiss-based air engineering giant Luwa India, is a stickler of precision and quality in adopting technology. When he launched a MultiCell Filter MCV at the recently-held India-ITME 2016 in Mumbai, he beamed with a broad smile when he announced that the filter system is 90 per cent Made in India. “We have used best raw materials, quality steel, all sourced from India,†he said proudly. With many multinationals in India, setting a firm foot on the Indian soil, vowing to go all-out for Make in India, the Indian entrepreneurs are already claiming that 100 per cent Made in India textile goods are sweeping over nations across the seas.
No doubt, the textile industry in India is fast responding to the clarion call of the Prime Minister, Narendra Modi – Make in India. The new mantra is slowly and steadily penetrating through the complex supply chain of the textile industry – from fibres and spinning to the retail end.
Premium khadi! No one thought of it a few years ago!. Now Raymond recently signed a a partnership with Khadi Village and Industries Commission to promote khadi globally. “We are trying to uplift khadi from common fabric to a fashion fabric,†says Gautam Singhania, Raymond CMD. For the 11 lakh people who are employed in khadi industry, it is the beginning of a dream come true reality.
Here is another Made in India success story! Explore the world of fluid fashion with LIVA, says Aditya Birla Group, which is rewriting the history of fashion with its revolutionary fibre. Birla Cellulose is already a favourite of global brands who are delighted to be working with a fibre that is glamorous and at the same time, as close to nature as one can get. And nature never goes out of style, as the bright and beautiful in India are discovering through Liva Viscose.
Make in India has spawned an enthusiastic breed of entrepreneurs, who are eagerly hitching onto the concept. Even the not-so-glamorous machinery side shows unflagging interest. “This is a weaving machinery that we have developed with 100 per cent Indian materials and technology,†says Dilip J Dhamanwala, Director of the Surat-based Lifebond Machines Pvt Ltd. The machine does him proud since he has been selling such machines at a time when even cheap Chinese weaving machines are flooding the market.
Says Jatinder Kaul, National Sales Leader, Compressed Air Systems & Services, Ingersoll Rand: “The Make in India programme focuses on new initiatives designed to facilitate investment, foster innovation, protect intellectual property, and build best-in-class manufacturing infrastructure. It encourages companies as well as entrepreneurs, whether big or small to manufacture their products in India. Make in India campaign together with some specific steps taken like ease of doing business, phased reduction of corporate tax, government’s resolve of rolling out GST, and investments in infrastructure development will boost the Indian Economy. Air compressor is an integral part of more than 90 per cent of industries and is considered the fourth utility. So, the growth in manufacturing will fuel the demand of air compressors as well. Last year was a challenging year for Industrial Air compressor industry with the industry shrinking by approximately 10 per cent from 2013. We expect the Make in India initiative will make this industry grow at a healthy CAGR in coming years.â€
He told The ITJ Editor: “The campaign looks very promising since the time it was launched last year. Few highs about the initiative are certain measures which shall help in increasing GDP growth, tax revenue, cut on duties on various goods, aiming good quality standards and to attracting investment in India for development.
Also, global investors who were looking for a stable government to start their business in India now have that need fulfilled which will definitely help kick start FDI. To sustain and grow the flow, Indian government would need to change rules, regulations and policies to make it investor friendly. In a survey done by World Bank for 189 countries, India currently ranks 134 for ease of doing business, 186 for enforcing contracts and 179 for starting a business and this reflects on the room for improvement. With the steps taken by the Government of India, we should be able to improve this substantially.â€
The Indian Textile Accessories and Machinery Manufacturers of India (ITAMMA) has gone to the extent of setting up an Expert Panel with the special agenda of Make in India, and “setting a target to have about 400 textile technologists & engineers on this Panel, who shall support the entrepreneurs of Textile Engineering Industry in technological development and successful execution of the various schemes of the Government of India in addition to the individual projects.†ITAMMA Expert Panel consists of experts on Metallurgist, Automation, Mechanism, Heat Treatment, Surface Finishing, Systems, Oil, Engineering, Lubricant, Lean, Technologists, Company Turnaround, 3D modeling, Mechatronics, Reverse Engineering, 6 Sigma, Theory of Constrains, etc. & Textile Technologists relating to Sub-groups, spinning, weaving, process, technical textiles, etc.
Says Kishore Khaitan, President of ITAMMA, in a pre-budget memorandum to the Ministry of Heavy Industries and Public Enterprises: “The textile machinery & accessories manufacturing industry in India is not only a major contributor to exports and employment in the country but also provides a wide range of machinery, accessories and services to the Indian textile industry. Hence the fortunes and competitiveness of the Indian textile industry are inextricably linked to the textile engineering industry of the country.â€
The Indian Textile engineering industry is more than 100 years old with advanced spinning machinery, power looms, weaving preparatory machines, finishing and dyeing machines, etc. As per a Government survey, 1,446 manufacturing units with total investment being Rs 7,800 crore are operating at below 60 per cent capacity utilisation. About 70 per cent of the units are not having CNC machines and more than 80 per cent of the units are MSMEs. This reflects a weak industry structure.
Annual imports of textile machinery at Rs 10,385 crore constitutes more than 70 per cent of Indian consumption while domestic production is only Rs 6,000 crore of which exports were Rs 2,600 crore.
Says Khaitan: “Most firms are SMEs (80 per cent) having lack of access to latest technology, R&D infrastructure with academic institutions not geared up to undertake R&D projects on commercial basis, lack of innovation and zero-defects culture. India does not possess advanced technology to offer machinery and parts for knitting, garmenting, non–woven, technical textiles, embroidery, made-ups, garment accessories and we need to attract leading international manufacturers to start manufacturing in India, preferably through Joint Ventures with Indian companies. Many machines are imported at concessional or nil duty while components attract 25 per cent or more duty (including CVD). Mills prefer buying expensive machinery from manufacturers abroad due to import duty concessions and TUFS support. This acts as a disincentive for such manufacturers abroad for starting manufacturing in India.â€
Seeking incentives to give a boost to Make in India, Khaitan says that given the right policy environment, Indian TEI has the potential to grow to Rs 25,000 crore by 2025 while exports can grow to Rs 8,000 crore in the same period. He is sure that this growth will create additional employment for 2,50,000 people and will benefit the nation additionally by largely eliminating the requirement for subsidies and TUFS to support the textile industry because purchase of indigenous machinery (which will be 40-60 per cent cheaper than imports) will help reduce the capital investment of the textile industry by over 30 per cent and reduce manufacturing cost by 15 per cent.
Khaitan reiterates his stand on the scope of textile machinery industry contributing to Make in India movement: “Make In India is very relevant not only for the textile machinery and accessories sector but also for the textile sector as a whole. We import more than 70 per cent of our requirement of machinery and parts, though we are the second largest producer of textiles in the world. We need FDI and JVs to make the latest technologies indigenously available.†“Indian prices of machinery and parts is generally 40-60 per cent cheaper than imports. Using Indian machinery and spares will reduce the investment cost for the mills significantly, making them more competitive and will also bring down subsidy burden of the Government.â€
In an informal chat during the recently-concluded India ITME, M Marimuthu of Coimbatore-based Peninsula Engineers, said that his entire machine is made in India and not even a single part imported from abroad. He said that Peninsula Engineers were once having a very good market share in the segment they were into until a few European companies took a larger cut in their market share.
With a proud look on his face, RK Shah, Managing Director of Rishabh Sagar Textile Equipments Pvt Ltd, said that one will find our machine in almost every single textile industry in India. RK Shah had started his career way back in 1962 in manufacturing machine tools known as the Tiger lathe machine. He subsequently changed and expanded the horizons from machine tools to textiles spinning by developing the very first cot grinding machine in 1969 and creating the brand which is now globally recognised as Sagar.
According to some sources, in a recent search by many Hong Kong companies for alternative production bases, Southeast Asian countries like Vietnam have apparently stolen all the limelight. In contrast, the awareness of India and its relevance as an alternative production base for garment production is not considered especially high among Hong Kong companies. Nonetheless, India may justify serious re-consideration due to the force of changes emerging over the past two years, particularly after the ‘Make in India Initiative’ was launched by the Modi Government in September 2014, which is a serious attempt to give a makeover to India as a global manufacturing hub. Under the Make in India initiative, investment opportunities for foreign companies and entrepreneurs are available across the entire value chain of synthetics, value-added and speciality fabrics, fabric processing set-ups for all kinds of natural and synthetic textiles, technical textiles, garments, and retail brands.
Some of the major investments in the Indian textiles industry are as follows:
- Trident Group, one of the leading manufacturers and exporters of terry towel, home textile, yarn and paper in India, has entered into a partnership with French firm Lagardere Active Group, to launch a premium range of home textiles under the renowned French lifestyle brand Elle Décor in India.
- Raymond Group has signed a Memorandum of Understanding (MoU) with Maharashtra government for setting up a textile manufacturing plant with an investment of Rs 1,400 crore ($208.76 million) in Maharashtra’s Amravati district.
- Reliance Industries Ltd (RIL) plans to enter into a joint venture with China-based Shandong Ruyi Science and Technology Group Co. The JV will leverage RIL’s existing textile business and distribution network in India and Ruyi’s state-of-the-art technology and its global reach.
- Giving Indian sarees a ‘green’ touch, Dupont has joined hands with RIL and Vipul Sarees for use of its renewable fibre product Sorona to make an ‘environment-friendly’ version of this ethnic ladies wear.
- Snapdeal has partnered with India Post to jointly work on bringing thousands of weavers and artisans from Varanasi through its website. “This is an endeavour by Snapdeal and India Post to empower local artisans, small and medium entrepreneurs to sustain their livelihood by providing a platform to popularise their indigenous products,†said Kunal Bahl, CEO and Co-Founder, Snapdeal.
- Welspun India Ltd (WIL), part of the Welspun Group has unveiled its new spinning facility at Anjar, Gujarat – the largest under one roof in India.
- The expansion project reflects the ethos of the Government of Gujarat’s recent ‘Farm-Factory-Fabric-Fashion-Foreign’ Textile Policy, which is aimed at strengthening the entire textile value-chain.
Government initiatives:
- The Indian government has come up with a number of export promotion policies for the textiles sector. It has also allowed 100 per cent FDI in the Indian textiles sector under the automatic route.
- India’s first integrated textiles city, which will largely cater to the export market and build a brand for Indian textiles abroad, is likely to be set up in the state of Andhra Pradesh.
- The Clothing Manufacturers’ Association of India (CMAI) has signed a memorandum of understanding (MoU) with China Chamber of Commerce for Import and Export of Textiles (CCCT) to explore potential areas of mutual co-operation for increasing apparel exports from India.
- The Department of Handlooms and Textiles, Government of India, has tied up with nine e-commerce players and 70 retailers to increase the reach of handlooms products in the Indian market, which will generate better prices and continuous business, besides facilitating direct access to markets and consumers for weavers.
- The Union Ministry of Textiles, which has set a target of doubling textile exports in 10 years, plans to enter into bilateral agreements with Africa and Australia along with working on a new textile policy to promote value addition, apart from finalising guidelines for the revised Textile Upgradation Fund Scheme (TUFS).
- The Government of India has started promotion of its ‘India Handloom’ initiative on social media like Facebook, Twitter and Instagram with a view to connect with customers, especially youth, in order to promote high quality handloom products.
Subsidies on machinery and infrastructure:
- The Revised Restructured Technology Upgradation Fund Scheme (RRTUFS) covers manufacturing of major machinery for technical textiles for 5 per cent interest reimbursement and 10 per cent capital subsidy in addition to 5 per cent interest reimbursement also provided to the specified technical textile machinery under RRTUFS.
- Under the Scheme for Integrated Textile Parks (SITP), the Government of India provides assistance for creation of infrastructure in the parks to the extent of 40 per cent with a limit up to Rs 40 crore ($6 million). Under this scheme the technical textile units can also avail its benefits.
- The major machinery for production of technical textiles receives a concessional customs duty list of 5 per cent.
- Specified technical textile products are covered under Focus Product Scheme. Under this scheme, exports of these products are entitled for duty credit scrip equivalent to 2 per cent of freight on board (FOB) value of exports
- The Government of India has implemented several export promotion measures such as Focus Market Scheme, Focus Product Scheme and Market Linked Focus Product Scheme for increasing share of India’s textile exports.
- Under the Market Access Initiative (MAI) Scheme, financial assistance is provided for export promotion activities on focus countries and focus product countries.
- Under the Market Development Assistance (MDA) Scheme, financial assistance is provided for a range of export promotion activities implemented by Textiles Export Promotion Councils.
- The government has also proposed to extend 24/7 customs clearance facility at 13 airports and 14 sea ports resulting in faster clearance of import and export cargo.
- The Ministry of Textiles has approved a ‘Scheme for promoting usage of geotechnical textiles in North East Region (NER)’ in order to capitalise on the benefits of geotechnical textiles. The scheme has been approved with a financial outlay of Rs 427 crore ($63.67 million) for five years from 2014-15.
Road ahead
The future for the Indian textile industry looks promising, buoyed by both strong domestic consumption as well as export demand. With consumerism and disposable income on the rise, the retail sector has experienced a rapid growth in the past decade with the entry of several international players like Marks & Spencer, Guess and Next into the Indian market.
The organised apparel segment is expected to grow at a Compound Annual Growth Rate (CAGR) of more than 13 per cent over a 10-year period.
– S JOSEPH & M KARTHIK