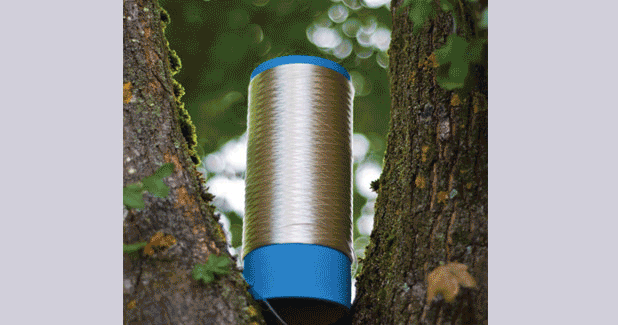
Sustainable textiles – The need of future
With awareness and demand, ecological parameters for all consumer goods gain significant importance. Market preferences have led buyers to lay down ecological specifications and eco labels have made their presence felt, feels Edward Menezes, Director of Rossari Biotech.
With awareness and demand, ecological parameters for all consumer goods gain significant importance. Market preferences have led buyers to lay down ecological specifications and eco labels have made their presence felt, feels Edward Menezes, Director of Rossari Biotech.
The textile production industry is one of the oldest and most technologically complex of all industries. The fundamental strength of this industry flows from its strong production base of a wide range of fibres/yarns from natural fibres like cotton, jute, silk, and wool to synthetic/man-made fibres like polyester, viscose, nylon and acrylic. The textile industry occupies an important place in the production of social product and the satisfaction of personal needs. Textile products are used in the manufacture of clothing and footwear and in other sectors of industry, such as the furniture industry and machine building.
Current scenario
Climate change is one of the major concerns of 21st century. Tremendous efforts are being made to tackle the climate change issue of the globe. Being one of the major polluting industries of the world, apparel and textile industry has caught the central attention. From fibre production to consumer use phase, the industry releases huge amount of carbon throughout the supply chain. Throughout the last half of 20th century, climate change issue has become the pivotal issue of discussions globally. Irresponsible human activities are primarily responsible for the ongoing climate change. Careless consumption of water, chemical and energy by industrial activities is making the situation tougher to confront. Unless we become conscious and make combined effort to ward off the threat, the world will be nearly inhabitable in the immediate future.
The world is becoming more and more energy hungry. Energy consumption results in carbon release to the environment. Carbon deposition in the environment is the main villain of climate change. Every human or natural activity that has some business with carbon release is a threat. The industrial activities have raised atmospheric carbon dioxide levels from 280 parts per million to 400 parts per million in the last 150 years.
The carbon dioxide and other gases in the atmosphere are virtually transparent to the visible radiation that delivers the Sun’s energy to the Earth. But the Earth in turn re-radiates much of the energy in the invisible infrared region of the spectrum. This radiation is most intense at wavelengths very close to the principal absorption band (13 to 17 microns) of the carbon dioxide spectrum. When the carbon dioxide concentration is sufficiently high, even its weaker absorption bands become effective, and a greater amount of infrared radiation is absorbed. Because the carbon dioxide blanket prevents its escape into space, the trapped radiation warms up the atmosphere.
The impact of this rise in atmospheric temperature results in more frequent and intense drought, storms, heat waves, rising sea levels, melting glaciers and warming oceans resulted from environmental exploitation can harm animals, destroy the places they live, and wreak havoc on people’s livelihoods and communities.
Recent natural disasters:
- Hurricane Maria in the Dominican Republic – September 2017
- Monsoon flooding in South Asia (Bangladesh, India, Nepal)
- Mudslide in Colombia – April 2017
- Hurricane Irma in the USA and Caribbean – September 2017
- Hurricane Harvey in the USA
- Gujarat, Mumbai Flood July – August 2017
- Cyclone Ockhi – December 2017
Increased awareness of the need to protect the environment and ecosystems is bringing changes to all spheres of human life. The interested parties in the environmental protection policies are no longer just environmental groups, consumers and producers but also retailers, exporters, importers, traders, technological societies and national, regional and international authorities. Rapid industrialisation and widespread use of many synthetic chemical compounds has led to many devastating realisations. Effects of their toxicity are only now being felt.
Water pollution
Humans have established communities and flourished around sources of clean, drinkable water since the beginning of time. It’s vital to our survival. Do you know that you can survive several days without food but not without water. It’s heartbreaking to know that millions of people worldwide do not have access to this most basic need, and are dying of thirst and water-borne diseases. Freshwater sources around the world are threatened by water pollution. Not only are we managing our resources poorly through wastage, we are also thoughtlessly dirtying it.
Effect of polluted water on humans
How does water pollution affect humans? Try drinking untreated water nowadays and your body will immediately react to it. You will get a stomach ache at the least. Water-borne diseases account for the deaths of 3,575,000 people a year and the majority of these are children. Infectious diseases can be spread through contaminated water. Some of these water-borne diseases are typhoid, cholera, paratyphoid fever, dysentery, jaundice, amoebiasis and malaria.
- Chemicals in the water also have negative effects on our health.
- Pesticides can damage the nervous system and cause cancer because of the carbonates and organophosphates that they contain.
- Chlorides can cause reproductive and endocrinal damage.
- Nitrates are especially dangerous to babies that drink formula milk. It restricts the amount of oxygen in the brain and cause the “blue baby†syndrome.
- Lead can accumulate in the body and damage the central nervous system.
- Arsenic causes liver damage, skin cancer and vascular diseases
- Flourides in excessive amounts can make your teeth yellow and cause damage to the spinal cord.
- Petrochemicals, even with very low exposure, can cause cancer.
Previously unknown allergies are being attributed to the use of chemical finishes on apparel. Consumers and retailers now take purchasing decisions not just on price and quality but also health, environmental and social aspects associated with the products themselves. The scope of this new requirement is through the entire life cycle of the product.
With awareness and demand, ecological parameters for all consumer goods gain significant importance. Market preferences have led buyers to lay down ecological specifications and eco labels have made their presence felt. An eco-label provides brief information on environment-related product qualities. It enables consumers to identify those products that are environmentally safe; that have been manufactured using eco-friendly materials and do not contain chemicals that are harmful to the user. Since eco-friendliness is an additional product quality, it can be used for marketing and advertising purposes.
What are the benefits of eco-labelling?
- Enhanced export market opportunities
- Improved product quality
- Financial savings
- Improved environmental performance
- Stimulating consumer awareness about environmental impact of products
- Directing manufactures for the environmental impact of their products
Some of the eco-labels are described below:
GOTS: The Global Organic Textile Standard (GOTS) is the world’s leading textile processing standard for organic fibres, including ecological and social criteria, backed by independent certification of the entire textile supply chain. The aim of the standard is to define globally recognised requirements that ensure the organic status of textiles, from harvesting of the raw materials through environmentally and socially responsible manufacturing all the way to labeling in order to provide credible assurance to the end consumer. Textile processors and manufacturers should be able to export their organic fabrics and garments with one certification accepted in all major markets.
bluesign: The bluesign standard brings together the entire textile manufacturing chain to jointly reduce the ecological footprint of a responsibly acting textile industry. Instead of focusing on finished product testing, the bluesign standard analyses all input streams – from raw materials to chemical components, to resources – with a sophisticated “Input Stream Management†process. Prior to production, components are assessed based on their eco-toxicological impact. Potentially harmful substances can hence be eliminated before production even begins. A key aspect of the bluesign standard is never to compromise on product functionality, quality or design. Using the best available technology along the entire textile manufacturing chain ensures that products meet the environmental standards without cutting back on performance requirements.
Greenpeace: Greenpeace is campaign to stop industry poisoning our water with hazardous, persistent and hormone-disrupting chemicals. The detox campaign challenges top brands to make amends by working with their suppliers to eliminate all hazardous chemicals across their entire supply chain, and the entire life-cycle of their products.
Restricted substance list (RSL): RSL is an essential first step in any serious textile safety programme. A retailer, manufacturer, association or regulatory body develops an RSL to identify the chemical substances that will be limited or prohibited in its products or industry. The value limits on hazardous substances should be set at levels that provide acceptable protection for both workers and consumers. An effective RSL must be updated regularly to capture changes in evolving manufacturing chemistry, governmental regulation and expanding medical knowledge.
Manufacturing restricted substance list (MSRL): MRSL is an innovative new approach to manage chemicals in products and supply chains. MRSL differs from a RSL because it restricts hazardous substances potentially used and discharged into the environment during manufacturing, not just those substances that could be present in finished products. MRSL takes into consideration both process and functional chemicals used to make products, as well as chemicals used to clean equipment and facilities. It addresses any chemical used within the four walls of a manufacturing facility.
The Zero Discharge of Hazardous Chemicals ZDHC group developed and published a MRSL with input from key stakeholders from the ZDHC member brands and chemical companies. A MRSL changes the way we look at chemicals management. It focuses at the beginning of the manufacturing cycle by prohibiting chemicals entering the facility and thus reduces the need to treat and clean up effluent.
ZDHC: ZDHC is a group of apparel and footwear brands and retailers working together to lead the industry towards zero discharge of hazardous chemicals by 2020. ZDHC was started in 2011, mostly as a response to the Greenpeace DeTox campaign. Part of the initial work established a joint roadmap that demonstrated the collaborative efforts and steps needed to lead the apparel and footwear industry towards zero discharge of hazardous chemicals for all products across all pathways by 2020.
OekoTex: The STANDARD 100 by OEKO-TEX is a worldwide consistent, independent testing and certification system for raw, semi-finished, and finished textile products at all processing levels, as well as accessory materials used. Examples of articles that can be certified: raw and dyed/finished yarns, woven and knitted fabrics, accessories, such as buttons, zip fasteners, sewing threads or labels, ready-made articles of various types (garments of all types, domestic and household textiles, bed linen, terry products and much more). OEKO-TEX Standard 100 therefore contributes to high and effective product safety from a consumer’s point of view. Test criteria and limit values in many cases go far beyond applicable national and international standards. Extensive product checks and regular company audits also ensure that the industry has a globally sustainable awareness of the responsible use of chemicals. With this concept, the OEKO-TEX Standard 100 has taken on a pioneering role for many years.
REACH: REACH wants to guarantee the safe use of chemical substances and preparations throughout the entire industrial production chain and therefore imposes not only obligations on the producers and importers of chemicals concerning the gathering and distribution of information on the characteristics of the substance, but also on the downstream users, such as textile manufacturers. After all, each downstream user has to assure the proper safe use of chemicals and see to it that the necessary information is sent to the chain, also about substances contained in articles.
Cradle to cradle: Applying the Cradle to Cradle design concept (C2C) leads to textile products that are healthy in a chemically defined way. Decisions regarding material and design are made aiming at additional benefits of the products by either becoming biological or technical nutrients after use.
Greenscreen: GreenScreen is a new certification standard that promotes the use of inherently safer chemicals in products. The certification meets increasing demand for: a) safer chemicals in manufacturing and b) a simple platform that enables the communication of safer chemicals in products and formulations across supply chains. GreenScreen Certified is based on the GreenScreen for Safer Chemicals, a globally recognised tool that identifies hazardous and safer chemicals through a rigorous benchmarking scoring system. GreenScreen Certified will be applied to different product categories,
with the Textile Chemicals representing the first product application.
Clean Production Action launched GreenScreen Certified Standard for textile chemicals to provide a clear and robust communication platform concerning chemicals in textile formulations. GreenScreen Certified enables formulators to communicate actions they are taking to help downstream partners manage regulatory and reputational risks related to chemicals and meet sustainability goals. And GreenScreen Certified provides brands with the platform to communicate their preferences and requirements for safer chemicals in textile formulations.
Higg Index: The Higg Index is an apparel and footwear industry self-assessment standard for assessing environmental and social sustainability throughout the supply chain. Launched in 2012, it was developed by the Sustainable Apparel Coalition, a nonprofit organisation founded by a group of fashion companies, the United States Government Environmental Protection Agency, and other nonprofit entities. Higg Index provides a tool for the apparel and footwear industry to assess sustainability throughout a product’s entire life cycle, from materials to end-of-life. The metrics created Higg Index are limited to a company’s internal use for the evaluation and improvement of environmental performance. Plans for a future version include the creation of a scoring scale designed to communicate a product’s sustainability impact to consumers and other stakeholders.
Green pathways in textile processing
Textile industry has undergone a drastic transformation as per the requirements of customers and ecology. Textile wet processing is a highly water intensive operation. The various chemicals like starch, dye-stuffs, auxiliaries, alkalies, acids, detergents, etc., that are used in the processing contaminate the water and cause pollution in terms of BOD, COD, pH, TDS, color, hardness etc., in the discharged effluent. As the stringent norms are fixed on the characteristics of discharged effluent, there is always a demand for chemicals auxiliaries, which can reduce the pollution load of effluent.
Alkali-free scouring process: The primary aim of any scouring process is to break the outer pectin layer. Once this is broken the cellulose polymers present inside the cotton fibrils are exposed. These have high affinity for water due to abundance of hydroxyl group, thus making the cotton fibre hydrophilic. In conventional scouring the entire amount of pectin is removed from the cotton fibre. This pectin serves as a binding material for the cellulose fibrils. After its removal the coherence between the fibrils decreases due to which the strength of the structure goes down. Also it leads to harshness of yarn and increased hairiness on the surface. Alkali-free scouring process removes the pectins to a level just enough that it facilitates the even absorbency of the yarn. Presence of pectin leads to strength retention, lesser hairiness and smoother surface profile. It offers cleaner processes, replaces chemicals, reduces TDS, saves time, water and energy throughout production chain.
Neutral bleaching process: Bleaching process in one of the most important pretreatment processes of textile processing by which fabric’s reflectance, whiteness and absorbency is enhanced. The fabric should be free from natural and added impurities before it goes for coloration, i.e. dyeing or printing. Improper preparation is often the cause of problems encountered in the dyeing and finishing steps. Conventional bleaching process is carried out at higher pH say 11-12 pH. As caustic works on swelling mechanism and attacks the secondary cell wall so strength loss is high which also results in decrease in tensile as well as tear strength of the fabric. Due to complete removal of the outer pectin coating of the cotton fibre, the surface profile also becomes rough. In addition to reduce the pH from 12-13 the fabric needs to be passed through several rinsing steps, which increases the demand of water ultimately creating effluent problem.
Neutral bleaching, i.e pH of 6-7, the cellulose material tends to swell significantly less than under alkaline conditions, which means better liquor penetration and more effective removal of mineral impurities and metals. It replaces caustic during process so additional neutralisation step is avoided. Since bleaching carried out at neutral condition damage to cellulose is less as compared to conventional bleaching using caustic.
Clay-based products: Clay minerals are very reactive because of their large surface area and because they commonly carry a charge. The charge that originates at clay surfaces is usually due to chemical reactions that occur at the surface of minerals, but it can also be caused by adsorption of surfactant ions. Due to large surface area of clay, it can adsorb all kind of impurities natural and synthetic. It can be very effective in removal of oil even silicone oil. The application of harmless, non-toxic clays can help to produce textile goods in a cleaner way, in a number of applications, as an alternative for products based on organic chemistry.
Denim processing
Denim is the most preferred clothing of today’s youth. Various items of denim like pants, skirts, jackets, belts and caps are available in the market. To give distressed denim look many types of washing are given to denim fabric. Stonewashing process is one of the textile manufacturing process used to give a newly manufactured cloth garment a worn-in or worn-out appearance. Stone could cause the problem of environmental disposition of waste of grit produced by stones. The process of stone washing also harms big, expensive laundry machines.
Cellulases are used to provide that distressed worn out look to denim fabric. Cellulase is environmentally friendly compared to pumice stones. It reduces the percentage of damage caused to denim caused by the rough effect of stones of them. Typical application parameters of cellulase stone washing are 50-55 degree Celsius and slightly acidic and neutral pH. Nowadays, denim fading process with no pumice stones in in demand. As no stone is used, disadvantages of pumice stone is completely avoided.
Laccase is the newest enzyme class to be introduced into denim finishing. Laccases are multi-copper oxidases that catalysed the oxidation of wide range of phenols, including indigo under simultaneous reduction of oxygen to water. It is useful enzyme for eco-friendly bleaching process of blue denim. The advantage of this enzyme is the specific treatment on indigo dyestuff and not of the fibre itself. This enzyme break down the indigo molecule, without affecting other dyestuff like sulphur, reactive or direct dyes.
Only within the past few years it has been recognised that the catalytical ability of cold-active cellulase offers huge industrial application potential. Decrease in energy consumption and increase the life of cloth are obvious benefits of cold washing. The low temperature stability of cold active cellulase has been regarded as the most important characteristics for use in the industry because of considerable progress towards energy savings. These are unique product which works at low temperature (20-35 degree Celsius) for good fading effect. Also it produces better cutting and good puckering effects.
Acid stable enzyme & protonic treatment in CBR
Pin hole damage is a serious problem faced by textile manufacturers. Pin hole damage is mainly concerned with cellulosic materials in processing while carrying out bleaching with hydrogen peroxide at high temperature. In bleaching presence of heavy metal ions and certain other impurities reduce bleaching action. Commercial amylase works at pH 6-7. But it has limitations like stability in acidic conditions, starch conversion rate, contamination risk etc. Acid stable amylase can be combined with protonic treatment which is a huge advantage for textile process house. With this combined i.e. one step desizing protonic treatment process, we can reduce consumption of energy resource and time. Acetic acid replacement: Conventional acetic acid has many disadvantages. It can damage cellulosic substrates, capable of weakening cellulose easily, special precautions are needed while handling. Besides this it has adverse effect on labours, increases load on effluent and storage hazard over a period of time. Eco-friendly buffer can be used to overcome these problems.
A few disadvantages of acetic acid:
- These acids are capable of easily weakening cellulose (cotton) fibres
- Metal corrosion
- May attack entire surrounding (spreading of corrosion area )
- Special precautions needed
- Adverse effect on the health of labour
- Storage hazard over a period of time
- Incorrect dosage can cause destruction of cotton
- High TDS so increased effluent load
Soda ash replacement: Normally soda ash is the most commonly used alkali in reactive dyeing. However, dye fixation on cellulosic fibres is generally low. This results in a highly coloured dye house effluent, which is not favourable from the environmental grounds. As much as 50 per cent of the total cost of a reactive dyeing process is attributed to the washing-off stages to remove unfixed or hydrolysed dyes and treatment of the resulting effluent. Furthermore, the higher concentrations of alkali required in cellulosic dyeing may pose additional effluent problems. Under this circumstances dyeing without conventional Soda Ash can results in much lower TDS in effluent causing much less trouble in effluent treatment.
Acidic washing off: Reactive dyes have better property in terms of fastness. Dyeing of cellulosic substrates takes place with reactive dyes under alkaline conditions. But this alkaline conditions also facilitates reaction of reactive group with the dye liquor, resulting in deactivation or hydrolysis of the dye. This hydrolyzed dye adhere onto the substrate and keep on getting removed during washing treatments causing poor wash fastness. This hydrolyzed dye must be removed by rinsing and using an appropriate Washing-off agent in order retain the fastness properties. Using acidic washing off agent we can avoid neutralization step after dyeing along with improvement in fastness properties.
Sodium hydrosulphite free reduction clearing
Dyeing of polyester is exclusively carried out by the use of disperse dyes, but due to the highly hydrophobic nature of Polyester fibre, after-treatments are required for optimal satisfactory fastness.
During dyeing, particularly of deep shades, there will invariably be some dye particles that adhere to the fibre surfaces, or are retained by yarns without penetration into the fibre. These mechanically held particles result in decreased fastness to washing, rubbing, sublimation and dry cleaning. The reduction clear process is designed to remove surplus dye and dyeing auxiliaries (e.g.migration inhibitors, carrier residues and surfactants) without altering the shade of the dyeing. But these process has many disadvantages. It is toxic process with unpleasant odour. Need subsequent neutralization step. It is not only increases TDS in effluent but it also damages effluent drainage system. Caustic hydrose replacement product can either replace hydrose caustic process or avoid separate reduction clearing step in polyester dyeing.
Amido Silicone: Fabric softeners have gained great importance in textile finishing and are widely used to provide softness, surface smoothness, good draping qualities and fluffiness. The use of silicones for softening fabrics has been well known for quite some time. Mostly amino modified silicones are used in textile industry as amino groups provide better affinity to textile fibres. But yellowing may occur when amino silicones are used on white garments due to the oxidation of amino radicals in the presence if air, heat and light energy which results in the formation of azoxy compounds.
Amido functional silicones have limited range of viscosities and nitrogen content. The benefits of amido silicones are highly effective softening, ease of ironing, water absorbency and low yellowing. They are more substantive to fabrics than polydimethylsiloxanes. Also they are biodegradable too.
All-in-one products
In recent times, many end users demand different properties in single product during processing. Such products not only avoid usage of different chemicals but also helps to reduce confusion about dosages which need to be added. Also no need to remember sequence of chemicals to be added. Possible applications in textiles are as follows
- Emulsifier cum wetting agent in scouring – removes impurities from cotton with whiteness improvement.
- Scouring Bleaching with single product – No need to add stabilizers, sequestrants, wetting agent during pretreatment
- Single bath peroxide killing and biopolishing
- Dyeing with single product – no need of seperate levelling, dispersing agent, acid buffer during dyeing like PES dyeing
- Enzyme based all in one product for denim – desizing, fading, antiback in one product Such kind of chemicals helps to save utilities like energy, time, water. Also helps to reduce load of effluent.
The Zero Discharge of Hazardous Chemicals ZDHC group developed and published a MRSL with input from key stakeholders from the ZDHC member brands and chemical companies.
Eco-friendly printing package
For many years, improving the quality of prints was the main goal in product development. Lately economic, environmental and toxicological considerations have become more important. Using more environmentally-friendly preparation and auxiliary products, for example, to reduce or to eliminate formaldehyde on fabric is currently one of the major concerns in the textile printing industry. The binder for pigment printing containing formaldehyde or formaldehyde containing or generating compounds for cross-linking with substrates. Formaldehyde is one of those chemicals that just isn’t good for humans. Recent efforts have been made to reduce the formaldehyde content of or the free formaldehyde generated by binders or totally eliminate the formaldehyde component of binders for environment reasons.
Conclusion
Everything from health and safety to waste management is surrounded in red tape. While some regulations are essential, others can be a massive burden to manufacturing companies. While it is undeniably good news for the local environment and employee, sustainability and environmental regulations can be expensive for manufacturing firms. While many regulations may be beneficial to consumers, each regulation adds an additional burden to the companies that must comply with the requirements, which often differ from country to country. Many local and regional regulations affect various aspects of the manufacturing process, from the ability to use certain materials, to worker exposure, to disposal of waste and byproducts.
We at Rossari ensure that our all operations comply with applicable health, safety and environmental laws and regulations. We undertake pollution prevention practices to minimize environment impact and consumption of the natural resources. We ensure that our products meet all international standard laws or certifications. We also ensure that we have complete visibility into global supply chains so we can prove not only our own compliance, but also that of our suppliers. Keeping equipment functioning is an essential part of running a manufacturing facility. Regular preventive maintenance helps us to increase output and ensure customer satisfaction with delivery lead times.
References
- https://www.slideshare.net/virenderchhachhiya/climate-change-40874811
- •https://www.niwa.co.nz/our-science/climate/information-and-resources/clivar/greenhouse
- •https://www.telegraph.co.uk/education/stem-awards/design/deadliest-natural-disasters/
- •https://water.usgs.gov/edu/earthwherewater.html
- •http://www.theworldcounts.com/stories/how-does-water-pollution-affect-humans
- •https://support.coyuchi.com/hc/en-us/articles/205437885-What-does-it-mean-to-be-GOTS-certified
- •http://www.ecolabelindex.com/ecolabel/bluesign
- •https://www.oeko-tex.com/en/business/certifications_and_services/ots_100/ots_100_start.xhtml
- •http://www.roadmaptozero.com/
- •https://echa.europa.eu/regulations/reach/understanding-reach
- •https://www.epea.com/c2c-sectors/textiles/
- •https://www.greenscreenchemicals.org/
- •In house product Information library
Edward Menezes, Director, Rossari Biotech Limited Address: 201-A & B , Ackruti Corporate Park, LBS Marg, Next to GE Gardens, Kanjurmarg (W), Mumbai 400 078. Tel: + 91-22- 25777604 | 05, Fax: +91-22-25796982 Email: amey.damle@rossarimail.com