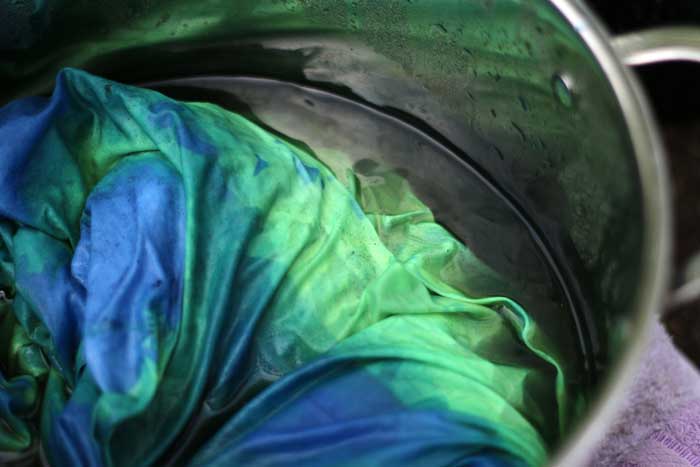
Sustainability in shades
The next decade will witness significant advancements in sustainable textile dyes and chemicals, driven by technological innovations, changing consumer preferences, and tightening regulations. Divya Shetty explores the trends poised to shape and dominate the industry in the coming years.
In a recent analysis by the World Bank, the group has highlighted over 70 toxic chemicals that stem exclusively from textile dyeing processes. This concerning revelation has spurred governments globally to take immediate action. Traditional dyeing practices not only waste valuable resources and money but also endanger freshwater sources through the discharge of harmful chemicals.
In response, rising awareness and regulatory pressures are driving companies to explore and implement innovative dyeing methods.
Innovations driving sustainability
Dyes and chemicals play a significant role in manufacturing of sustainable textile products. Although major environmental footprints of a product come from the type of raw materials being used, next to that is wet processing in which dyes and chemicals are key contributors.
Early stage technologies such as waterless dyeing using Super Critical Fluids, foam/spray dyeing/finishing, plasma/laser/ozone treatment etc. come with very high capital investment along with risk associated in investing technology which are yet to mature.
Umasankar Mahapatra, Managing Director, Pulcra Chemicals India
According to Umasankar Mahapatra, dyes and chemicals industry is transforming itself keeping pace with three key drivers;
Consumer preferences: Consumers prefer sustainable products, which needs sustainable chemical inputs. This also includes business model innovations like rentals, second life, subscription etc.
Advancements in technology: Textile wet processing equipment’s are also transforming to become more efficient both in terms of productivity and reduced energy footprints. Disruptive innovations are also coming in the market to address this aspect. Dyes and chemicals need to align accordingly to support this shift.
Compliance: Regulatory compliance requirements are evolving much faster in recent times which require dyes and chemical industry to shift towards safer chemistry. Also lot of focus is there on social compliance of manufacturing and distribution.
All these driving demands for sustainable dyes and chemicals. key innovations to reduce utility (water, steam, electricity), reduce chemical usage, improve operational efficiencies and substituting conventional chemicals to bio based / bio-degradable and resource efficient chemicals are gaining traction. Processes like digital printing, enzyme based pre-treatment, low temperature processing, bio – based finishing, Advancement in continuous processing, dyeing technologies etc have given significant benefits. In all these cases, there is a reduction of environmental footprint and made the processes more sustainable.
The conventional textile processing is witnessing a paradigm shift from the usage of petrochemical based non-renewable resources to products and processes which address the ecological balance.
Prof Ashok Athalye, Associate Professor, ITC Mumbai
By embracing these innovative approaches, the textile chemicals industry is moving towards a more sustainable future, reducing its environmental impact.
Traditional processing sector is struggling to meet the requirements of sustainability focused brands and retailers. There is no choice but to adopt sustainable products and processes to stay in business.
- Digital printing: Reduces water and energy consumption while allowing for more precise colour application.
- Low-impact dyes: New dyeing technologies and chemicals minimise environmental harm.
- Biodegradable materials: Sustainable materials are being developed to replace traditional textiles.
- Closed-loop production: Companies are adopting closed-loop systems, where materials are continually cycled back into production.
Even Prof Ashok Athalye highlights the drivers of the current textile chemical industry by saying, “Circularity and utility management have become the key drivers for the innovation in the textile industry. The conventional textile processing is witnessing a paradigm shift from the usage of petrochemical based non-renewable resources to products and processes which address the 4 pillars of ecological balance, namely;
- Replace: High volume and solid waste generating basic chemicals
- Reduce: Consumption and usage of auxiliary chemicals by process modifications
- Reuse: Pre-treatment and post colouration wash-off baths by synergistic approach
- Recycle: Post-process water and substrate by suitable segregation techniques
Waterless and bio-based technologies
Traditional textile processing is known for its massive water footprint, leading to the generation of vast amounts of liquid effluents. To address this, collaborative efforts between machinery, colourant, and chemical manufacturers are driving the development of innovative technologies designed to minimise water consumption throughout the processing chain. Some of these concepts include;
- Ultra low liquor ration dyeing machines
- Nano-bubble, nebulisation, mist, spray and foam application
- Hot-Air dyeing, super critical fluid (ScCO2) processing
- Wash-off free reactive and single bath dyeing of P/C, P/V blends
- Bio-surfactants, bio-colourants and herbal-functional finishes
Brands that take genuine effort to produce environment friendly products should be receive funding and the necessary infrastructure. The institute should upgrade the syllabus to industry 4.0 and ahead. AI should be welcomed at all levels of management.
Yogesh Gaikwad, Director, Society of Dyers and Colourists
Building on their successful launch at ITMA last year, DyStar committed to expanding its bio-based product range, featuring Dianix Disperse dyes and a variety of DyStar auxiliaries.
As contemporary as it sounds, the waterless technology is here since quite some time informs Yogesh Gaikwad. He says, “The waterless domain is not new, supercritical fluid technology has been around for one time. Some companies have now the support of brands and the technology is again gaining traction. Once limited to synthesis the technology has spread to natural fibres dyeing too. Bio Based products have already entered the market. Brands are welcoming the change. The progress is slow but steady. As countries make moves to fulfilling their United Nations sustainable goals the process of adapting this technology will speed up.”
Some companies are committed to ensuring sustainability not only in their own manufacturing processes but also in the operations of their collaborators and partners. Mahapatra adds, “Apart from state-of-the-art manufacturing facility at our global headquarter near Munich in Germany, each Pulcra affiliates producing products for domestic markets so that environmental footprints of logistics can be minimised. This also helps to develop customised products for customers, as the processing conditions and technologies differ country wise. Our plant in India is a ZLD unit and we have all necessary compliance for products and manufacturing set-up in place.
For Financial year 2022-23, export of Dyes and Pigments (D&P) stood at 7,54,235 tonne and imports were 5,48,793 tonne. For calendar year 2023, imports of D&P stood at 6,08,452 tonne and exports stood at 7,89,958 tonne.
Anuja Parikh, Associate Director, CARE Ratings
At Pulcra, we are continuously working towards giving sustainable products to industry sectors we serve textile, fibres and leather. We are moving towards more eco-friendly and resource efficient raw materials and packaging in our production. To enlarge product offerings which are bio based, Pulcra acquired Devan Chemicals (Belgium), which is specialised in biobased finishing. Pulcra is offering sustainable denim dyeing technology – Breviol DNV for several years which reduces water consumption significantly. Last year Pulcra in collaboration with Inditex brand launched innovative single bath pre-treatment and dyeing technology: Sustineri which is getting lot of attention in 100 per cent cotton and cotton blends exhaust processing. This technology helps to reduce water, steam and electricity requirements in dyeing process significantly. Pulcra also offers solutions for sustainable fibres and yarns production like recycled polyester, natural fibre spinning like flax, wool,” adds Mahapatra.
Challenges in adopting sustainable practices
Transitioning to sustainable processing and dyeing practices presents several challenges. Emerging technologies like waterless dyeing with supercritical fluids, foam or spray dyeing and finishing, and treatments using plasma, laser, or ozone require substantial capital investment. Additionally, there are inherent risks in adopting technologies that are still in their early stages of development. Many of these methods also have limitations regarding the range of products they can effectively produce. As a result, without financial support, ensuring the feasibility of such investments becomes a major challenge.
Mahapatra lists down various reasons why manufacturers find it difficult to adapt to sustainably chemicals. He says sustainable processes using innovative dyes and chemicals are relatively less challenging. But at times these are expensive as compared to their traditional counterparts. So unless customers are willing to pay for the same, adoption remains low.
In some cases, there are technical limitations as well in sustainable/bio-based products. Some of these technical challenges are as below:
- Colour inconsistency and low reproducibility associated with natural/bio dyes.
- Limited colour gamut with missing deep, bright shades in natural/bio dyes.
- Sustainable/bio-based finishes: low in wash durability.
Other challenges associated with adoption of sustainable processing are:
- Limited research and development in this space in particular or in overall textile related research funding.
- Cost of compliance (external testing, certification) is a big hurdle for small to mid-size players.
- Lack of skilled manpower in sustainability area, specially measuring and reporting of environmental footprints in precise manner.
“Green washing and fake sustainable labelling is the biggest challenge. Also ignoring the norms of effluent discharge by manufacturer who prioritise cost over environment would be catastrophic. Brands that take genuine effort to produce environment friendly products should be receive funding and the necessary infrastructure. The institute should upgrade the syllabus to industry 4.0 and ahead. AI should be welcomed at all levels of management,” elucidates Gaikwad.
Anuja Parikh, “Raw material price volatility including crude and cotton price, cyclicality associated with end-user industry mainly textile as seen over the past 2 years with subdued demand in the major textile consuming nations, competition from low-cost Chinese products, high freight cost and container availability issues etc are the challenges that we are facing because of the global uncertainty right now.
But all these challenges offer opportunities as well to the players who are committed to sustainable textile manufacturing.
Impact of consumer awareness and regulations
The consumers are the major stake holder and the key component of the textile value chain. Various Governmental regulations and the Non-Governmental organisations international brands are continuously evaluating and developing regulatory norms. The textile processors and in turn the dyes and chemical manufacturers are expected to adhere to these norms in order to remain competitive in the dynamic and evolving market requirements.
Also, consumers want to know the origin of their clothing and the environmental impact of its production. This has led to increased pressure on companies to be transparent about their supply chain and production processes. “From very beginning, we at Pulcra are committed to provide products which are environmentally compliant. A dedicated global working group has been formed to deal with Product Safety & Regulations (PSR) related points and keep all Pulcra affiliates updated with developments in this space. ESG team is monitoring environmental footprints internally and very soon we will come up with reporting those to external world,” states Mahapatra.
Gaikwad urges the regulatory body to take strict action as it is having a direct impact to the ecosystem. “The regulatory bodies have to still demonstrate the wide spread effect of their regulations. The pollution in various cities is getting worse every year. We have yet to see rivers with pure drinkable water flowing through major cities. Total dissolved solids are the major hurdle to eliminating the contamination from water. The effluent treatment companies are coming up with innovation in this area. The challenge does not only in understand the new innovations but also the eagerness to try out new technologies is missing even at the trial stages. This has to change, not doing anything is no more and option,” opines Gaikwad.
Educational institutions can play a pivotal role in shaping the minds of future textile engineers and manufacturers, fostering a commitment to creating sustainable products. Athalye suggests few measures the institutes can take, “Staying updated with emerging technologies and strengthening academic-industrial collaboration are vital for driving innovation in the textile industry. Developing skilled human resources and supporting both basic and applied research help address industry challenges effectively. Additionally, evaluating chemical testing norms and fostering communication between industry stakeholders and regulatory authorities ensure compliance and sustainable growth.”
Shaping a greener tomorrow
The next decade is poised for transformative advancements in sustainable textile dyes and chemicals, driven by technological breakthroughs, shifting consumer demands, and stricter regulations.
Circular products and business models are set to lead across all categories and price points within the textile industry. Just a few years ago, recycled fibre content and sustainable processes were less important in the technical textiles sector. Today, even technical textile products are embracing sustainable materials and methods without sacrificing functionality.
Each year, millions of tonne of textile products end up in landfills or remain stagnant in the value chain. Emerging recycling technologies, including chemical recycling, are expected to reduce the dependence on fresh fibre production—whether natural or synthetic—liberating valuable resources for alternative uses. In the premium market, bio-based fibres, along with eco-friendly dyes and chemicals, are anticipated to gain wider acceptance, further driving sustainability in the sector.
According to Mahaptra, “ Manufacturing closer to the point of consumption will drive adoption of 3D printing, digital printing, or maybe something completely disruptive which will cut short the existing value chain of textile manufacturing which is very complex and time consuming. Overall consumers will consume less quantity of textile products, but will go for products which will last longer, and will have superior functionality. This will demand high quality innovative dyes and chemicals.”
As AI is proving to be a game-changer, Gaikwad also feels that it will play a big role in transforming the textile chemical industry. He says, “Probably AI will play a big role in providing solutions to our recycling and bio-based manufacturing. The advances in AI will become beyond the comprehension of humans. Innovations will be a day to day activity. Technologies will be shaped based on the stringent regulatory norms. Human involvement will be limited to admiring the technology breakthroughs. Additionally, recycling is creating new perspectives in the way materials are remoulded after their life cycle is over. We need to prepare for a zero virgin manufacturing ZVM. This is probably a new term I am creating. There will be a day when there will be no more fossil fuel based raw material for manufacturing left. Garbage, agriculture and animals will become the new source of materials for manufacturing. ”
With the development and commercialisation of new technologies, the textile industry is expected to see a significant rise in the adoption of alternative natural fibers such as bamboo, banana, Napier grass, and polylactic acid (PLA). Additionally, single-step dyeing combined with functional finishing and advancements in digital pigment printing are set to revolutionise efficiency and eco-friendliness in textile production.