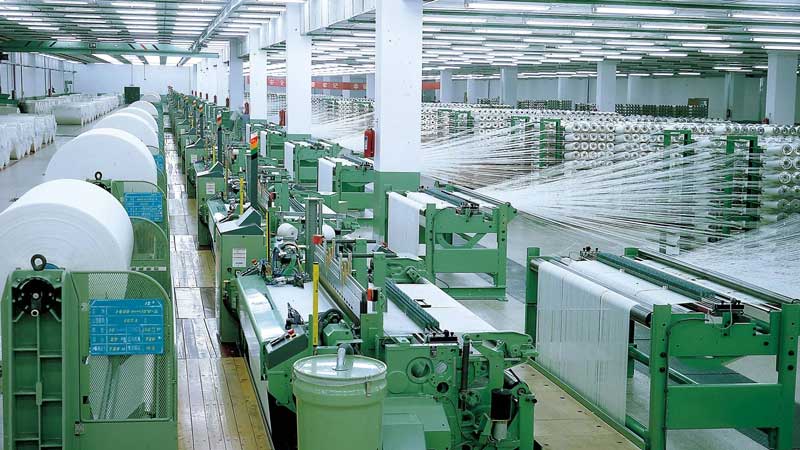
Spinning a recovery?
The emphasis on Make in India, Aatmanirbharta (self-reliance) and the rollout of the Production-Linked Incentive (PLI) scheme for the sector in recent times may enable the Indian textile and apparel (T&A) industry to reclaim its rightful share globally, says Manish Pant.
In 77 CE, when India had nearly 30 per cent share of the global GDP, Roman historian Pliny the Elder described the country as “the sink of the world’s gold”. He was particularly miffed at the Roman Empire’s treasury being emptied by the ever-growing demand for Indian textiles.
Fast forward to the 21st century, and the country has seen its legacy industry losing out to even newbies like Bangladesh and Vietnam. Factors such as prohibitive electricity costs, relatively expensive labour and the competitor nations’ success in attracting FDI, all contributed to the decline.
“The three ‘Ps’ of people, products and processes available played a major role in driving away the business from India,” Brajesh Singh, India President at the global advisory Arthur D Little tells ITJ.
But the industry may now be prepping for a comeback. The emphasis on Make in India, aatmanirbharta (self-reliance) and the rollout of the Production-Linked Incentive (PLI) scheme for the sector in recent times appear to be having an impact.
One of the foremost ways to reclaim the country’s position as a global textile hub is through technology.
“Digitalisation is a major event and India needs to move up the curve there. Its adoption in terms of reducing human error during production is what needs to be focused on,” observes Samir Joshipura, Group CEO of paper to apparel manufacturer Trident Group.
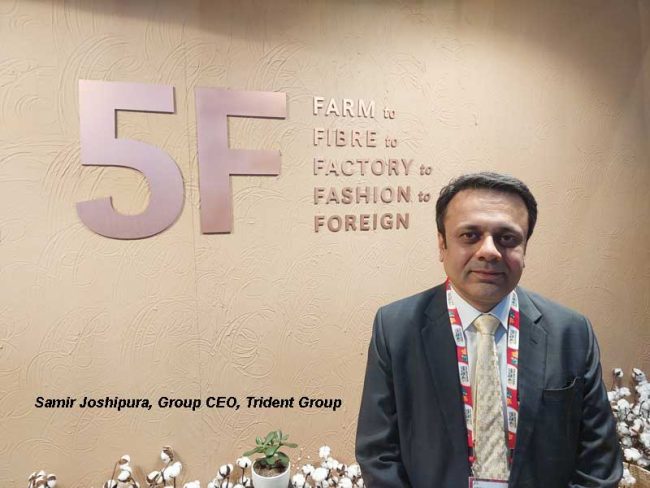
The company is putting cutting-edge technologies in everything from Enterprise Resource Planning (ERP) to plant machinery to mobility to make its processes smarter. Joshipura feels the industry also needs to stand out by also focusing on sustainability and moving up the global value chain.
“Being the world’s second-largest producer of cotton, rather than looking at exporting to the lower side of the value chain, the country must progress to exporting full garments.”
Joshipura is echoing a sentiment that has been gaining currency in the world’s fifth-largest textile and apparel manufacturer. While competing on cost may not be entirely feasible, the country can potentially offer immense value in several other areas.
Arthur D Little’s Singh thinks this can be best achieved by equally focusing on different pieces of the value chain. “The textile sector is highly fragmented as it’s not just about garments but also home furnishing, bed linen, jute, etc. We need to, therefore, ride a couple of wagons like sustainability, innovation and cost, all at the same time!”
Currently, the domestic apparel and textile industry contributes 2 per cent to the country’s GDP and 7 per cent of the industry output in value terms, according to Ministry of Commerce data. The share of textiles and apparel in the overall export basket of India was 10.33 per cent during FY21-22. The country has targeted to achieve $250 billion in textile production, with $100 billion for the export market by 2030.
Take sustainability for instance. Trident Group has been aggressively investing in the area to lower long-term costs. “We have zero liquid discharge in textiles and have already put up 28 megawatts (MW) of renewable energy, with another 12 MW in the pipeline, to meet 50 per cent of our total power demand,” says Joshipura.
The company also utilises agro wastes such as wheat straw and rice husk to produce electricity. Other than meeting their commitments to sustainability, these measures also help substantially reduce electricity bills. They are also promoting Better Cotton (BC), to reduce pesticide use as part of the country’s 5F strategy encompassing farm to fibre, fibre to factory, factory to fashion, and fashion to foreign markets.
The company has also incorporated the country’s rich craftsmanship and social tapestry in its Atulya Bharat range of products to showcase diversity from Gujarat’s lippan mud work to Kashmir’s pashmina designs to Mumbai’s bustling crowds.
The sustainable opportunity
Another potentially high-growth segment within the sector is technical textiles, which have specialised applications in areas such as construction; transportation; medicine and hygiene; industrial products and components; agriculture, horticulture and fishing; and home textiles. With a current market size of about $22 billion, the country is its fifth-largest producer globally and hopes to expand this to $300 billion by 2047. This segment has been particularly boosted by the growing concerns around climate change as well as the increased production of nonwoven sustainable fibres.
“While our fibre was earlier used only in spinning yarn it is now also being used in making technical textile products such as geostextiles, carpets, filters, spun lace fabric, etc., all of which have a big market. In our view, the business of technical textiles can multiply by up to 4x as it’s still in its infancy,” avers BP Sultania, Joint President of one of India’s largest polyethylene terephthalate (PET) bottle to polyester yarn recycler, Ganesha Ecosphere.
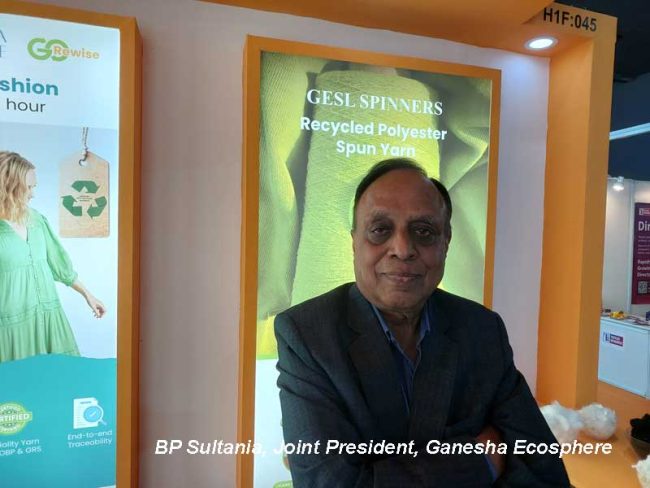
Dinesh Chuomal, Senior Marketing Manager at recycled polyester fibre maker BLS Ecotech seconds this view. “Due to government incentives for nonwoven and technical textiles, we are witnessing healthy growth,” he says, adding, “While the spinning sector has been largely dull, the nonwoven technical textiles segment is growing well.”
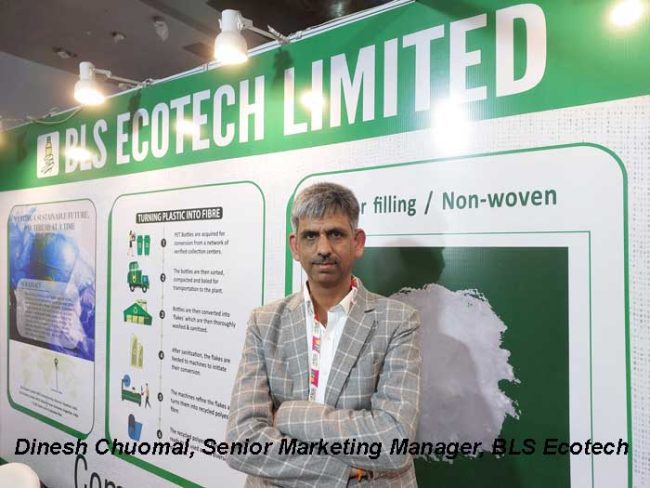
Choumal who started his career in the industry in the mid-1990s informs that for a long time manufacturers would be hard-pressed to sell even 25 tonnes of recycled fibre a month.
“Till 2008, only coarse denier had a market as a felt filling. But things have started improving with the adoption of new machines capable of producing lower denier fibres, and in the times to come, the sale of recycled fibres can potentially exceed that of virgin fibres!” he observes.
“A lot of work is being done in the area of sustainable fibres, with active participation from the recycling industry. Today, leading textile brands are emphasising recycled fibres, spun yarns and filaments,” says Sultania.
The growth is also evident in the capacity expansion being undertaken by the recyclers. Rules notified by the Ministry of Environment, Forest and Climate Change mandate the use of 30-50 per cent recyclates by all packaging manufacturers or brands in rigid packaging applications by 2025. This will progressively increase to 60-80 per cent by 2028. And so will the production of recycled fibres.
For instance, Ganesha Ecosphere’s combined recycling capacity is around 15,000 MT per month. “Proposed expansion over the next five years may take up our capacity to 25,000 MT per month. Two production lines installed at our Warangal (Telangana) plant are already working at full capacity and we will be adding a third line this year,” remarks Sultania.
“We are presently working on another plant to eventually reach 500 MT production capacity per day. This is being done to enhance capacity in technical and nonwoven textiles,” informs Choumal.
In recent years, customers in major export markets such as Europe and the US have not only started demanding textiles and apparel made from sustainable materials but are also willing to pay more for them. This has resulted in leading lifestyle brands such as IKEA, H&M and Zara gradually shifting to products made from recycled materials.
In February, Ludhiana-based integrated plastic recycler Rudra Ecovation (formerly Himachal Fibres) launched a versatile wearable material under the brand name Anaura at India’s largest textile exhibition Bharat Tex 2024 held in New Delhi. Made from recycled plastic, currently, 320,000 meters of the fabric is being produced daily.
“Anaura is all about the aura of wearing sustainable, where the wearer is enjoying fashion, comfort and acting responsibly, all at the same time. It can be used for making fashionable garments, home furnishings, carpets, etc.,” informs Akhil Malhotra, Chairman & MD, Rudra Ecovation.
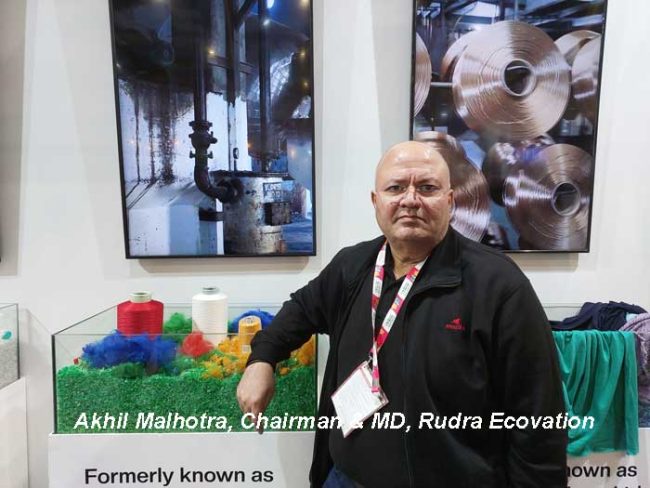
Following the merger of the group company Himachal Fibres, the company’s three plants – two in Punjab and one in Himachal Pradesh – will be utilised to manufacture carpets, acoustic panels, technical textiles and Anaura.
“We have already announced plans to double our fibre and filament capacity in four months and are simultaneously looking to massively expand Anaura’s production,” notes Malhotra.
This focus on becoming globally compliant is expected to provide the domestic industry an edge over the competition. However, while manufacturers bet big on sustainable textiles, certain challenges need to be addressed in the near to medium term. The first is about improving the supply of raw materials. Removal of curbs on the import of plastic waste will go a long way to help recyclers, according to some in the industry.
“The government must look at allowing the import of raw materials because manufacturers face shortages in winter. Today, all recycled fibre manufacturers have fully automated effluent treatment systems (ETPs), so no amount of harmful waste will be generated,” assures Ganesha’ Ecosphere’s Sultania.
As demand picks up, there is also a need to ramp up the number of plastic recycling plants manufacturing products such as granules, pellets and flakes. While China is believed to have around 3,000 recycling plants, in comparison India has a little over 200.
“We need more processing units to come up in India,” urges Rudra Ecovation’s Malhotra.
Another emerging concern among industry players is the hoarding of plastic waste. An official with a recycling company requesting anonymity told ITJ, “Financiers start hoarding raw materials if they anticipate a shortage. This often results in manufacturers increasing the prices of finished products and buyers shifting to virgin materials.”
The industry suggests strict enforcement of Harmonised System of Nomenclature (HSN) code to curtail the practice.
Making machines for the world
Meanwhile, plant equipment makers are also gearing up for the impending boom. New Delhi-headquartered family-run Jogindra Industries, which manufactures yarn dyeing, conditioning, laundry and dyeing machines, has significantly increased production by 20 per cent. With repeat orders coming from the countries of the Far East, including China, and the Commonwealth of Independent States (CIS), the company plans to further boost production by 30 per cent.
“Textile companies are now adopting fully automated machines, while earlier they used to go for either semi-automatic or manual ones. As a result, equipment makers like us are adding more features to our products to bring them to par with machines from the best European manufacturers,” says Harmeet Singh, Director of Sales & Marketing, Jogindra Industries.
For the past few years, the company has also started investing heavily in innovation, setting aside 10 per cent of its budget for R&D.
“Simply importing technologies would have made our products costly. That’s how we ended up allocating a significant percentage of our expenditure to make them globally acceptable,” says Inderpal Singh, Director of Technical, Jogindra Industries.
The company is 9001:2015 ISO certified and their products are also CE marked, which means they can even be sold in the EU.
Dismissing the notion of foreign-made machines being better, Harmeet emphasises, “Going forward we will start offering even better products. We are already competitively priced, have lower overheads and provide better after-sales support.”
“Due to the increased demand for automation, we have started focusing on Industry 4.0, improving the efficiency of the machines and sustainability. We are currently working with German automation systems supplier SedoTreepoint to further improve our high-end products,” reveals Inderpal.
With India projected to become the world’s third-largest economy by 2027, the textiles and apparel sector will continue to play an important role in the country’s GDP growth.
“We must create products, services and other materials with which to compete globally, while also paying attention to incentivising the industry in terms of skilled labour, cheaper electricity and access to capital,” states Arthur D Little’s Singh.
The concerned departments in the central and state governments must, therefore, work proactively to effectively address some of these macro issues.
Concurrently, Trident Group’s Joshipura feels that companies will also need to enhance their focus on the domestic market. “The earlier perception of exports as a large market and the domestic market as a filler is fast changing. We are looking at tripling our domestic sales over the next few years.”
He proposes to do that with new products to complement their exports and domestic basket as well as designing and branding to cater to the higher end of the market, asserting, “We are confident that textile sales will once again start earning India a lot of gold in foreign exchange!”
It seems that more than 1,900 years after first raising an alarm over Indian textile imports, Pliny’s soul may not find solace anytime soon.
Ways to reclaim Indian T&A industry’s lost glory: 5F Focus: Farm, Fibre, Factory, Fashion and Foreign marketsCreating sustainable products and adopting cutting-edge production technologiesDeveloping high-end products for both exports and the domestic marketTarget 2030: $250 bn in textile production, with $100 bn of exportsExpand Technical Textiles market size to $300 bn by 2047 |