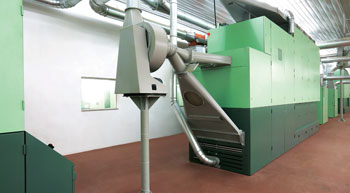
Raw material saving in blowroom & carding
The most important factor in the area of blowroom and cards is the raw material. A saving of 1% good fibres shows considerable effects, writes Simon Urrutia. At a customer in southern India, the rare opportunity presented itself to carry out a direct comparison of the blowroom and card waste. Running parallel there are a Rieter blowroom and carding section as well as a preparation line from another manufacturer, each with practically the same year of construction and almost the same production rate.
The most important factor in the area of blowroom and cards is the raw material. A saving of 1% good fibres shows considerable effects, writes Simon Urrutia.
At a customer in southern India, the rare opportunity presented itself to carry out a direct comparison of the blowroom and card waste. Running parallel there are a Rieter blowroom and carding section as well as a preparation line from another manufacturer, each with practically the same year of construction and almost the same production rate. With this comparison, card production was in focus. The aim was a 75 per cent higher performance of the C 70 card with qualitively equal yarn.
Framework conditions
The test was based on a blend of various Indian cottons with a trash content of 3 per cent. The card sliver produced by both lines was spun on the same downstream machines – draw frames, roving frames and ring spinning machines – to a carded knitting yarn of Ne 30 count.
Significant results:
The results are impressive. The Rieter line with VARIOline and C 70 cards achieved the following values compared to the other manufacturer:
- 75 per cent higher production of the card
- equal sliver and yarn quality (the values are within the fluctuation rate usual in the spinning mill)
- 27 per cent energy saving
- 1 per cent waste saving.
How are these excellent results achieved?
The Rieter fibre preparation guarantees gentle opening, efficient cleaning and intensive mixing of the fibres at highest production, based on the following features:
- microtufts for efficient cleaning
- progressive cleaning in several stages
- bypass option of the clearer module according to fibre material
- VARIOset for easy adjustment of the setting during operation.
An outstanding feature of the C 70 card is the largest active carding area for high performance with excellent quality. The efficient cleaning at high production is achieved by selective trash elimination at various points:
- on the licker-in
- in the pre- and post-carding zones
- by the continuously adjustable flats speed.
Effective savings
In this particular case, the Rieter line with blowroom and card with the lower energy requirement achieves yearly savings of around $32,500 at a line production of 1,000 kg/h and an electricity rate of 10 US cents per kWh.
The 1 per cent waste resp. raw material savings with a line production of 1,000 kg/h and a cotton price of $1.48 per kilogram result in a yearly saving of around $1,20,000.
The article is authored by Simon Urrutia, Head – Product Management Blowroom, Card at Rieter. He can be contacted at: simon.urrutia@rieter.com