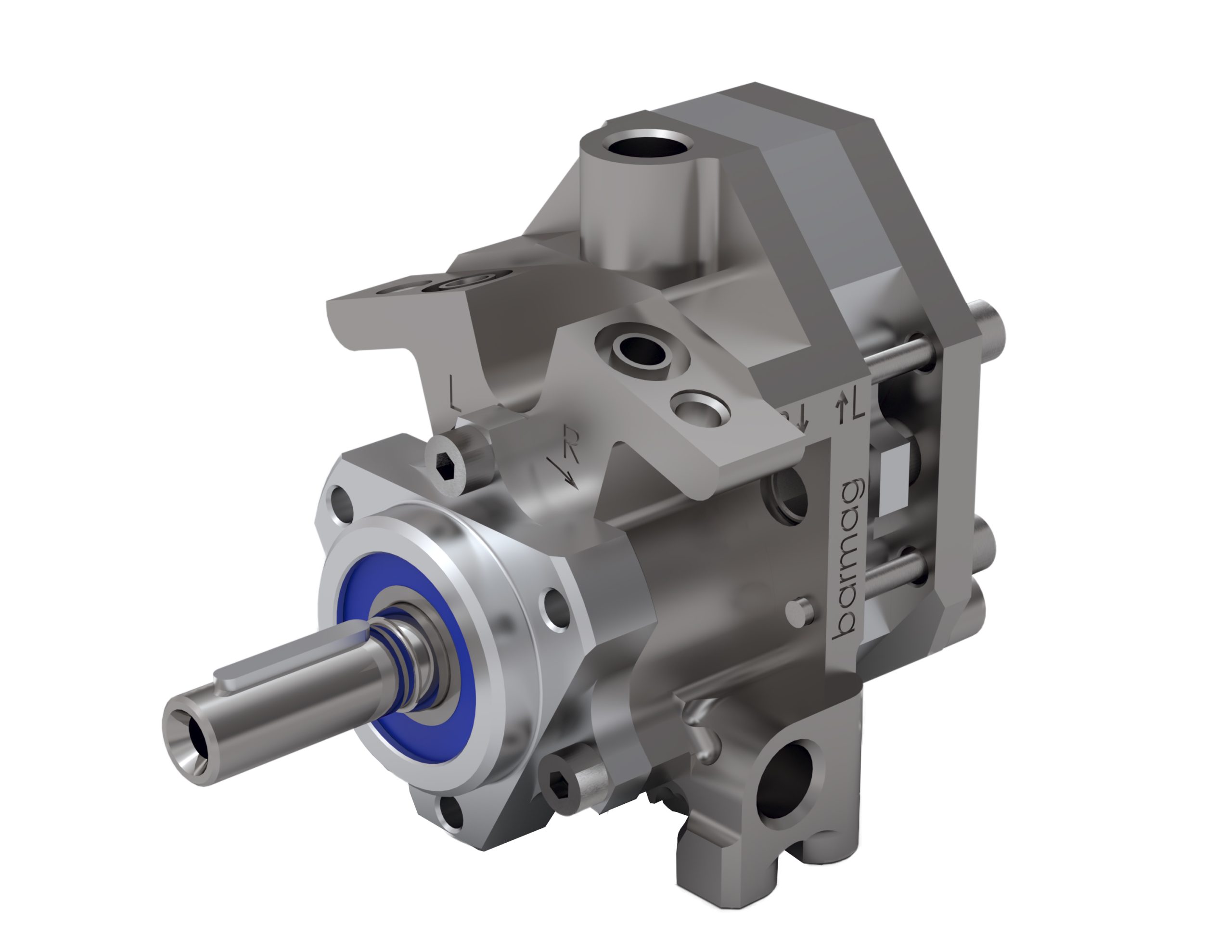
Oerlikon Barmag’s metering pump improves productivity
Developed especially for increasingly compact robot arms deployed in paint and lacquer systems, the pump enables efficient, high-precision paint application
Extremely low weight, improved productivity and increased service life – these features will be making Oerlikon Barmag’s GP451C paint metering pump stand out at this year’s PaintExpo 2022, taking place in Karlsruhe between April 26 and 29. Developed especially for increasingly compact robot arms deployed in paint and lacquer systems, the pump enables efficient, high-precision paint application in automobile production, in the aerospace industry and in the manufacture of components for generating renewable energy, for instance.
Paint application is frequently one of the most challenging manufacturing processes. Growing requirements in terms of the durability of end products demand highly-efficient paint and lacquer systems that apply paints and lacquers perfectly with regards to both look and feel, ensuring they provide the toughest and most wear-resistant surfaces possible. Oerlikon Barmag has been producing gear metering pumps for metered surface coating and painting since 1985. The high-precision pumps allow the paint and lacquer system atomizers to carry out their task reliably.
Long service life and extreme flexibility
Coming in at less than 1,000 g, the GP451C excels as a result of its particularly low weight. This considerably reduces the wear on the arms of the painting robots used. “The GP451C’s already low weight can be additionally reduced if produced by means of additive manufacturing. The innovative technology permits total design freedom when adapting the pump to the production system’s periphery,” explained Thorsten Wagener, the Sales Manager responsible for pumps.
The pump has a wide speed range (20 – 240 rpm), hence covering a large application area, which means that manufacturers do not have to deploy several pumps of varying sizes. At the same time, they save time and costs for product conversion, logistics and parts inventories.
The DLC wear-protection layer and the use of ball bearings considerably increase the pump’s service life. Furthermore, the pump is clearance volume-optimized in design, which dramatically shortens the required purging and product conversion times, hence helping to increase productivity.
Oerlikon is a global innovation powerhouse for surface engineering, polymer processing and additive manufacturing. Its solutions and comprehensive services, together with its advanced materials, improve and optimize the performance, function, design and sustainability of its customers’ products and manufacturing processes in key industries. Oerlikon has been a technology pioneer for decades. All developments and activities have their origins in the passion for supporting customers in achieving their objectives and increasing sustainability. Headquartered in Pfäffikon, Switzerland, the group has two divisions: Surface Solutions and Polymer Processing Solutions. The group has a global footprint of more than 11,800 employees at 207 locations in 38 countries and generated sales of CHF 2.65 billion in 2021.
With its Oerlikon Barmag, Oerlikon Neumag, Oerlikon Nonwoven and Oerlikon HRSflow brands, the Oerlikon Polymer Processing Solutions Division is focusing on manmade fibers plant engineering and flow control equipment solutions. Oerlikon is one of the leading providers of manmade fiber filament spinning systems, texturing machines, BCF systems, staple fiber systems and solutions for the production of nonwovens and – as a service provider – offers engineering solutions for the entire textile value added chain. Furthermore, Oerlikon has a high precision flow control components business that offers a large selection of gear metering pumps for the textile and other industries, including the automotive, chemical and paint markets. With Oerlikon HRSflow the division develops innovative hot runner systems for the polymer processing industry. In cooperation with Oerlikon Balzers, highly-efficient and effective coating solutions are offered here from a single source.
As a future-oriented company, the research and development at this division of the Oerlikon Group is driven by energy efficiency and sustainable technologies (e-save). With its range of polycondensation and extrusion systems and their key components, the company caters to the entire manufacturing process – from the monomer all the way through to the textured yarn and other innovative polymer processed materials and applications. The product portfolio is rounded off with automation and Industrie 4.0 solutions.
The primary markets for the product portfolio of Oerlikon Barmag are in Asia, especially in China, India and Turkey, and – for those of Oerlikon Neumag and Oerlikon Nonwoven – in the USA, Asia, Turkey and Europe. Oerlikon HRSflow is particularly at home in the core automotive markets. These include Germany, China, Korea and Brazil. Worldwide, the division – with more than 4,500 employees – has a presence in 120 countries with production, sales and distribution and service organizations. At the Research and Development centers in Remscheid, Neumünster (Germany), San Polo di Piave, Treviso (Italy) and Suzhou (China), highly-qualified engineers, technologists and technicians develop innovative and technologically leading products for tomorrow’s world.