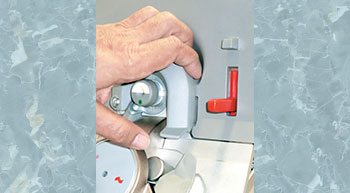
Latest rotor spinning technology with new R 66
The innovative spinning geometry has already proved its worth with the S 60, which is the only spin box to influence trash extraction during the opening process by means of the BYpass, says Stephan Weidner-Bohnenberger. The new S 66 spin box is the heart of the R 66 rotor spinning machine and the core of innovations. Further developed from the S 60 box, it allows higher yarn tenacity and better yarn evenness. With the new CHANNELpass, it is additionally more flexible. The improved ergonomic design makes operation even easier and more time-saving.
The innovative spinning geometry has already proved its worth with the S 60, which is the only spin box to influence trash extraction during the opening process by means of the BYpass, says Stephan Weidner-Bohnenberger.
The new S 66 spin box is the heart of the R 66 rotor spinning machine and the core of innovations. Further developed from the S 60 box, it allows higher yarn tenacity and better yarn evenness. With the new CHANNELpass, it is additionally more flexible. The improved ergonomic design makes operation even easier and more time-saving.
The central function of the R 66 is to produce a yarn which meets the requirements of the various markets.
The yarn quality is the basis for the success of a spinning mill. An appropriate yarn quality allows the spinner to organise the raw material selection very flexibly or to increase the productivity.
Low spinning tension & high delivery speed
The innovative spinning geometry already proved its worth with the S 60. With the compact TWISTunit comprising of CHANNELinsert, take-off nozzle and TWISTstop, the take-off tube is eliminated. This results in a significant reduction of the spinning tension and the spinning stability is thereby increased. Without isolating covers, the TWISTunit conducts the frictional heat from the nozzle more efficiently. This “COOLnozzle†technology enables high speeds to be achieved, especially with temperature-sensitive fibres, without leaving melting points in the yarn. The open construction of the S 66 spin box also reduces accumulation of trash.
Integrated precision for better yarn quality
At every closure of the S 66 spin box, the middle axis of the take-off nozzle is automatically centred to the middle axis of the rotor. That ensures not only the precise feeding of the fibres from the fibre guide groove into the rotor but also the perfect take-off point of the fibres from the rotor on the take-off nozzle. And that from spin box to spin box, over the entire machine length. The S 66 box thus guarantees high yarn tenacity and better yarn evenness. The construction of the TWISTunit is accordingly designed, so that the existing vacuum on the spin box permanently fixes the position of the CHANNELinsert at the right spot. With spin boxes of other suppliers, the vacuum draws this element undefined out of its ideal position.
Unique innovation for flexibility
The S 66 is the only spin box to influence trash extraction during the opening process by means of the BYpass. With the production of very fine cotton or man-made fibres, the BYpass remains closed to prevent any fibres being lost. With the spinning of heavily soiled slivers or waste material, the BYpass is half or fully opened.
The SPEEDpass is an energy-saving solution for the spinning of denim or very coarse yarns. With these applications, the spin box must deal with a greater fibre mass. The unique SPEEDpass accordingly allows an increased airflow rate without higher vacuum.
An innovation in respect of flexibility is the CHANNELpass. This exchangeable element can precisely adapt the air conditions in the fibre channel to different raw materials. More information on the CHANNELpass and the new S 66 spin box were provided by Rieter at the ITMA.
The advantages of the S 66 spin box in relation to yarn tenacity and evenness can also be exploited at the lower end of the raw material spectrum. The adjustable BYpass and an optional adapter in the trash elimination support the process. With the R 66 high quality yarns can be created from suitable waste blends.
Experiences of various customers
Customers confirm the advantages of the modern spinning technology and the high productivity that is thereby obtainable. Several practical production examples:
- 230 m/min for an Ne 18 knitting yarn from 100 per cent cotton in the USA
- Rotor speeds of 148 000 min-1 for an Ne 32 woven yarn from 100 per cent cotton in China
- 224 m/min for an Ne 20 knitting yarn from a polyester-cotton blend in the USA.
Save costs with O&M
Better spinning stability with the R 66 rotor spinning machine leads to better running conditions and therefore to fewer ends down. Fewer ends down reduce operator workload, also with automatic machines. The disassembly and installation of the spinning elements without tools, the good accessibility of the box and the simple operation make it considerably easier for the maintenance and operating personnel.