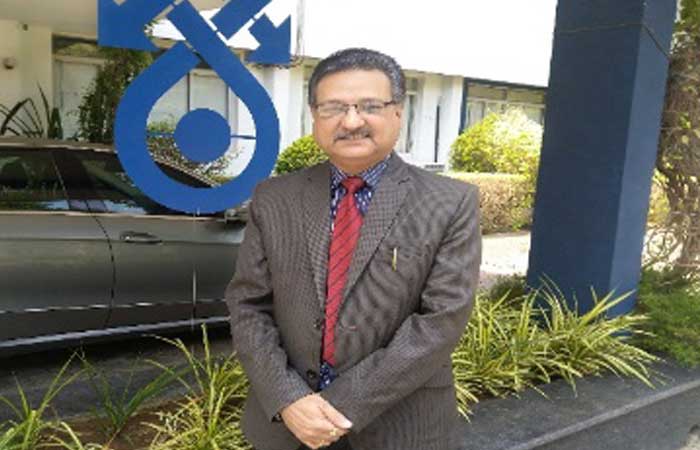
Kusters Calico aims to expand wet processing textile machinery in India
Kusters Calico is built up on an area of 11,400 sq m on 42 acre of land and was established in 1997 as a Joint Venture of Eduard Kusters Maschinenfabrik GmbH & Co KG of Germany and Calico Industrial Engineers (Calico) of India. At present, it is a 100 per cent subsidiary of JAGENBERG AG, Germany. Sushil Verma, Managing Director, Kusters Calico Machinery, shares emerging trends in machinery manufacturing.
How has been the journey of Kusters Calico Machinery since its inception?
We are world leader in manufacturing of wet processing textile machines. Thanks to our product performance, we are having global presence. We have supplied our machines to top class textile producers at Turkey, Egypt, Bangladesh, Turkmenistan, Uzbekistan, Indonesia, Germany, South America and India.
We export 60 per cent of our machines and have excellent network of business partners and all our export customers are giving us repeat orders. During last four years, we have expanded our operations by adding 2 more sheds and aggressively promoting our products in India to various customers by investing in new technologies to produce best machines. We are having excellent growth rate of 20 per cent year on year.
Last year, Kusters Calico Machinery started construction of its fifth plant in India. What is the significance of this for the company?
We have one of the best modern manufacturing facilities in India in the textile segment.
As I mentioned, for wet processing textile machinery we want to increase our footprint in pan India. To continue our market presence in world market and to offer latest technology to our Indian customers we have to increase our productivity. In 2018, we inaugurated our 4th assembly line and now we are inaugurating our 5th Assembly line. We are also extending our existing two sheds to increase space for Machining & Fabrication. We are also installing 3 new CNC Turnings, 2 Grindings, 2 CNC VMCs, Double Column Machining Centre and host of other machines to modernise the shops.
What are key challenges before the textile manufacturers today? How is Kusters Calico Machinery helping textile makers to overcome some of these challenges?
Key challenge for textile producing company is treatment of effluent generated and its impact on mother nature as today there are very stringent laws governing effluent treatment.
It is imperative for all textile producers to invest in advanced technology wherein they can reduce utility consumptions in the machines and here is where Kusters Calico comes into picture as our machines generate less discharge and consumes less water & power.
Recently, the government finalised locations for PM Mitra parks for textiles. How will this move benefit the industry and lead to more business opportunities for Kusters Calico Machinery?
As India is one of the largest cotton and man-made fibre producers, however India is less competitive against other countries. With PM Mitra scheme, Indian textile producers will be having better infrastructure and can compete in the world market with lesser logistic costs and improve its competitiveness. If textile producers are doing good then definitely we are doing good.
What are some of the key emerging trends in the industry?
There will be no sustainability with old technologies to produce textile fabric. Automation and new technologies to reduce carbon footprint will be the future.
How do you intend to take your growth story forward? (in terms of expansion, exports growth, new product launches, new opportunities/segments to tap, etc)
A: Diversification and research in product is the key for continuous growth. At Kusters Calico, we are making machines for converting and textile. In both verticals, we are seeing lot of demands for our machines. We are using our know how of coating and laminating of converting and will be coming with state of the art coating machines for textile. As well as we are investing in resources for improving our knits concept of dyeing and wet finishing. In coming ITMA, we will be exhibiting state of the art open width washing compartments for knits.