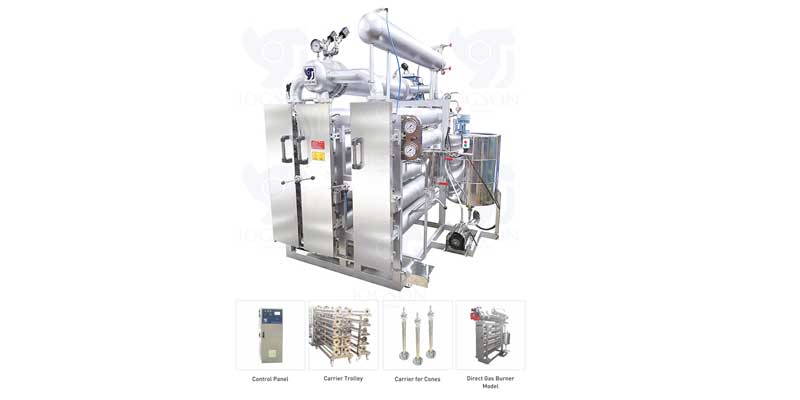
Jogindra Industries’ offers Dyeing Machine for higher productivity
The Horizontal Tubular Dyeing Machine is offered with capacities From 20 kg up to 720 kg per batch.
Jogindra Industries is offering a HTHP Horizontal Tubular Dyeing Machine which is a front loading, low MLR dyeing machine suitable for dyeing of polyester, cotton, viscose, nylon, acrylic, texturized, silk, wool, etc. in various forms like cone, tape, narrow fabrics, etc. It caters to the needs of high productivity textile Industries.
These machines are offered with capacities from 20 kg up to 720 kg per batch. However two or more machines of identical capacities can be coupled to give larger batch size up to 2000 kg. The coupled machines can be run as independent machine also at the press of a button.
Salient features
- Machine body and all parts coming into contact with the dye liquor are made of AISISS 316Ti/316L, highly corrosion resistant
- Bi-direction Turbo Pump For double stage liquor circulation (In-Out & Out-ln) with Inverter Drive For varying speed
- Control Panel with PLC and Touch Interface
- Ultra Low MLR of 1:3
- Air pad System to minimize the liquor ratio
- Colour dosing tank with Injection Pump For dozing the dye liquor into the machine
- High efficient internal heat exchanger For internal heating/cooling which has no energy loss to the ambient
- Variable loading with Flexible loading spindles or capacity reducing dummies up to 50 per cent capacity
- HT Drain – the machine can be drained at 130° C. without cooling
- Sampling pot to check the dyeing result while machine is in operation
- Pneumatically operated Front door locking / unlocking
- Human/Machine safety interlocks
- Safety locking device
- Safety level sensor For turbo pump and heating
Advantages
- Compact arrangement of JOGSON turbo pump, Heat exchanger and piping is the main key to floor space saving
- Bi-direction Turbo allows the packages to expand and contract by pressure changes, increasing the effectiveness and evenness in dyeing
- Ultra Low MLR of 1:3, consumes less dyestuff, chemicals, steam, water & produces less effluent discharge, hence it’s ECO friendly (leads to global savings of water and chemical) & reduces the production cost resulting in faster Return on investment
- Inverter driven turbo pump for variable flow control; saves up to 40 per cent power consumption hence more Energy Efficient
- HT drain at 130°C for oligomers elimination during polyester dyeing process, shortens batch time, effectively removes excess water from the package
- Variable loading with dummies maintains constant MLR & flow rate
- Working platform is not required as the top most tube in which the carrier is to be loaded is at the height of 1.5 mtr approx
- Overhead hoist need not to be installed as the carriers are loaded from front in the machine. Low roof height/any floor installation possible
- Excellent dyeing result and levelness, reduces yarn loss. High Right First Time (RFT)
- Water level, pressure, distinctive temperature multiple safety interlock ensures operational safety
Technical data
- Maximum design pressure 5 bar
- Maximum design temperature 140° C
- Heating gradient 25° C – 130° C approx at 5 C/ min. (Dry Saturated steam pressure at 7 bar)
- Cooling gradient 130° C – 85° C approx at 3.5 C/ min. (Cold water of 25° C at 3 bar)
Optional features
- Multiple drain, multiple fill
- Various heating mediums such as electric heaters, thermic fluid, steam & gas/diesel burner
- 100 per cent capacity stock tank with heating, mixing stirrer and transfer pump
- ph metre
- Hydro extraction device
- DPT for ration fill/ metred fill
- Linear and progressive dosing
- Multi with coupling option