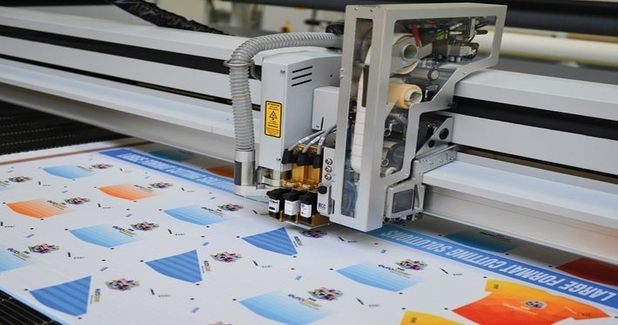
Eurolaser to show textile cutting tech at Texprocess
Eurolaser, a manufacturer of CO2 laser machines for cutting, engraving and marking, is set to present the latest technology in the field of textile cutting at the Texprocess fair in hall 4.0, stand D91.
Eurolaser, a manufacturer of CO2 laser machines for cutting, engraving and marking, is set to present the latest technology in the field of textile cutting at the Texprocess fair in hall 4.0, stand D91. The leading international trade fair for processing textile and flexible materials will be held from May 14-17, 2019, in Frankfurt am Main, Germany.
The focus is on automation for Industry 4.0. This year, the cutting of textiles on the L-1200 and 3XL-3200 systems will be demonstrated live on-site. The emphases of the exhibition will be on the automatic feeding of textiles from the roll, on the cutting of printed textiles including the camera and QR code recognition as well as on the labelling of the individual pieces in a single operation, the company said in a media statement.
Eurolaser has revolutionised large-format textile processing with the laser cutting machine 3XL-3200. However, size alone is not the key to success. With the conveyor system, Eurolaser delivers a market proven solution especially for the automated processing of textiles. For this purpose, a special table concept is used. It consists of a stainless steel rod mesh and is particularly suitable for thin and flexible materials, such as textiles. It serves as a material carrier for the processing and at the same time as a transport element for the conveyor system. The material is fed via an automatic feeding unit. The automatic edge control of the feeding unit ensures a constant material alignment and thus, continuously precise high quality cuts – meter by meter. Due to the automated material feed while relieving the operator, the load factor increases. With sensors, the unwinding unit is controlled so that the previously defined position on the work surface is exactly maintained. This ensures optimal material utilisation and less material waste.
The material is fed directly from the roll by the conveyor belt to the laser system and processed there. The stress-free material feed does not cause any fabric distortion and the non-contact processing by the laser leads to excellent results. For synthetic textiles, a slight melt seam (cut & seal process) is created at the cut edge, which prevents fraying and saves additional work steps such as linking. During the laser processing, the already cut material can be removed from the laser system via the unloading table. The table extension has the additional advantage of enabling the material to be removed from three sides, which boosts flexibility in the production process even further. If necessary, a winding unit can be added to the unloading table. The unit ensures even winding of already processed textiles. For optimal results, retaining cutting bridges may have to be worked into the cutting contours in order to keep the cutting results in combination with the cutting edge material. The winding unit is positioned at the end of the cutting process thus, enabling full automation of the entire process.
CATEGORIES Industry Update