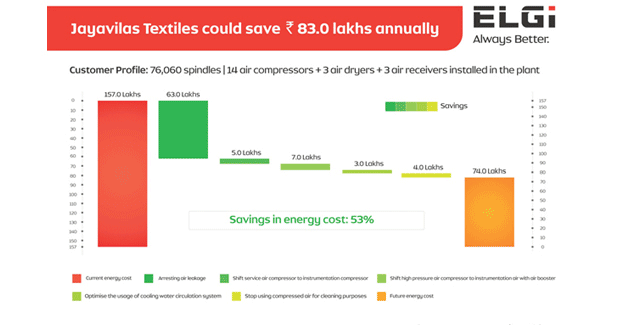
ELGi helps Sri Jayavilas Textiles save Rs 43 lakh
Sri Jayavilas Textiles saves Rs 43 lakh in annual energy costs by implementing measures identified in air audit. After completing all the changes, the company expects to save another Rs 40 lakh. Aleading name in the textile market in South India, Sri Jayavilas Textiles produces combed and carded single and double cotton yarn. Its plant in Aruppukkotai, near Madurai, produces 7,200 tonnes of cotton yarn and has an annual turnover of Rs 120 crore.
Sri Jayavilas Textiles saves Rs 43 lakh in annual energy costs by implementing measures identified in air audit. After completing all the changes, the company expects to save another Rs 40 lakh.
A leading name in the textile market in South India, Sri Jayavilas Textiles produces combed and carded single and double cotton yarn. Its plant in Aruppukkotai, near Madurai, produces 7,200 tonnes of cotton yarn and has an annual turnover of Rs 120 crore.
Sri Jayavilas Group has business interests in textile, transport, non-conventional energy (wind mills) and financial services. Sri Jayavilas Textiles, with a spindle capacity of over 70,060, has 14 air compressors, three air dryers and three air receivers, with a total installed capacity of 584 kW at 3,037 cfm.
The company’s actual power consumption was 275 kWh at 1,391 cfm, which generated a power bill of Rs 157 lakh per annum. An air audit identified opportunities to reduce consumption to 146 kWh at 656 cfm, with potential savings of Rs 83 lakh per year. After implementing some of the recommendations, Sri Jayavilas Textiles has already saved 75 kWh at 356 cfm, which amounted to Rs 43 lakh. The company is currently working on the rest of the recommendations, which are expected to bring an additional Rs 40 lakh savings in energy costs.
The purpose of an air audit
The energy efficiency of air compressor systems tends to reduce over time. To retain optimum efficiency, users need to monitor their performance and power usage, and conduct regular maintenance. Energy can be saved by changing the type of compressors being used, modifying the line design, arresting leaks and optimising usage.
Air audits help identify specific problem areas in the air compressor system and provide users a comprehensive report on what they need to do to reduce energy usage. ELGi has been conducting air audits for not only companies that use ELGi products but also those using other compressor brands. Since 2011, when ELGi started conducting air audits, it has completed over 250 air audits and proposed savings worth Rs 62.51 crore. For the textile industry alone, ELGi has conducted around 130 air audits.
The audit team uses flow meters, power analysers, water flow meters, digital pressure gauges, anemometers, infrared thermometers and condition monitoring equipment to evaluate an operation’s air usage. Following the technical analysis, the team submits a report with a summary of potential savings, along with recommended changes and associated costs. Some unique problems the team sees are incorrect compressor size, inadequate air distribution system, incorrect positioning of downstream accessories and air receivers, and poor regulation of pressure.
Proposals to reduce energy consumption
ELGi conducted a comprehensive air audit at Sri Jayavilas Textiles that revealed leakage points across departments, wasteful consumption patterns and incorrect system designs. Following the study, ELGi recommended a slew of measure that had the potential to save up to 42 per cent of its current power consumption without any change in the plant’s operating schedule of 8,160 hours per year.
Together, these measures could lead to a total of 146 kW per hour of potential savings, which translates to Rs 83 lakh per year in energy savings.
The study revealed that a significant part of the potential savings – to the tune of Rs 83 lakh a year – could come with leakage control measures. Some of the recommendations were to replace all the rubber hoses and polyurethane tubes with hydraulic hoses with good quality crimping joints and fittings; replace all leaking filter regulator lubricator units, drain valves and pressure regulating valves; install solenoid control valves in the main inlet in the airline; annual servicing of pneumatic cylinders, solenoid valve controls and air pressure regulators; and replace all union joints with flange with gasket joints. ELGi also recommended that the compressor control system be re-evaluated and adjusted, if necessary, after all the leakage control measures are implemented.
ELGi also recommended changes in the air pipeline design to make optimum use of instrumentation air; the installation of air pressure regulators, air boosters, air receivers and variable frequency drive at various points; and the use of venturi nozzle operated air guns for cleaning purposes.