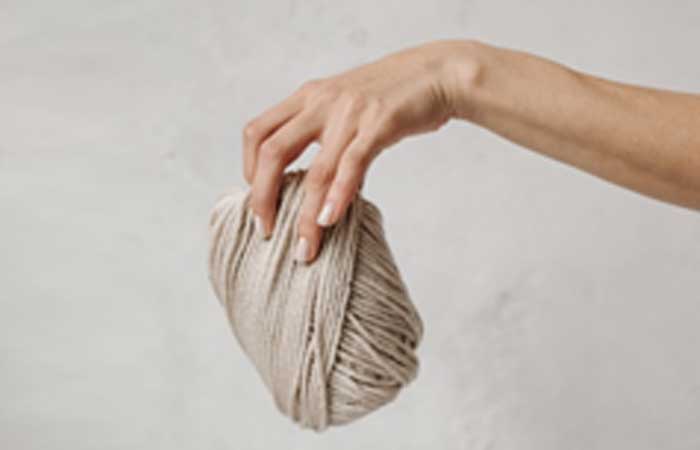
Achieving Balance: Harnessing the potential of man-made fibres and cotton
To increase consumption of synthetic fibers, there needs to be an increase in production of synthetic fiber and filaments by increasing capacity for raw materials such as PTA and MEG, and polyester staple fiber, suggests, Balkrishan Sharma.
The Indian textile industry is currently facing a pivotal moment as it navigates through new opportunities and challenges brought about by geopolitical changes and shifting trends in the global market. To become a leader in the industry, India must focus on achieving top-notch manufacturing capabilities and streamlining processes to improve customer service. The country stands to benefit from the growing demand for alternative sourcing locations beyond China, as India possesses a complete value chain, unlike other nations such as Bangladesh and Vietnam.
Challenges for MMF vs cotton
The Indian man-made fibres (MMF) industry is a major player in the global market, but it still faces various obstacles. These include higher production costs for materials such as polyester and nylon in comparison to cotton, as well as energy-intensive production processes. Additionally, imported products pose a significant threat in terms of competition, and a lack of technological innovation and consumer awareness about MMF products make it harder for manufacturers to market and sell them. The Indian government has traditionally been more supportive of the cotton industry, making it even more challenging for MMF manufacturers to compete. Another issue is that MMF fibres are not as breathable and comfortable as cotton, which makes them less appealing to consumers.
Opportunities for MMF
Despite the challenges, the MMF industry in India is also being presented with new opportunities, such as a growing demand for sustainable and eco-friendly products. Additionally, innovation in MMF production allows for a range of different forms, such as microfibers and smart textiles, which can open up new markets for manufacturers. The durability of MMF fibres also makes them more attractive to consumers for certain uses, such as outdoor clothing. Furthermore, MMF fibres can be more environmentally friendly than cotton, as they require less water and land to produce and can be recycled more easily.
Recent trends in MMF
In recent years, there has been an increasing awareness of the impact of textile production on the environment, particularly in the MMF industry. This has led to a shift towards more sustainable and eco-friendly fibres, such as recycled and regenerated fibres. These fibres are made from post-consumer or post-industrial waste like plastic bottles or textile scraps, which are collected, cleaned, and processed to create new yarns or fabrics. This process reduces waste in landfills and lowers the need for new raw materials, thus reducing the environmental impact of textile production. Regenerated fibres are made from natural raw materials like cellulose from wood pulp. These fibres are also processed to make new yarns or fabrics, which is considered environmentally friendly as it reduces the use of non-renewable resources like petroleum. Companies in the MMF industry are focusing on research and development to enhance the performance and properties of the fibres. They are developing new methods to produce fibres with improved features like moisture management, UV protection, and durability. Moreover, they are exploring ways to improve recycling and regeneration processes to make them more efficient and eco-friendly. Overall, the shift towards sustainable and eco-friendly fibres is vital for reducing the environmental impact of textile production and promoting a more sustainable future for the MMF industry.
Production Linked Incentive (PLI)
The PLI scheme is divided into two parts, PLI-1 for synthetic textile & apparel & technical textiles and PLI-2 for garment manufacturing. In my opinion, this scheme will have a positive impact in various ways, providing a solution to the challenges of limited scale and product diversity. It will promote the domestic manufacturing sector, create jobs, and attract investment. Additionally, the scheme will lead to cost reduction by encouraging companies to increase their scale of operations and improve their performance through financial incentives, ultimately increasing competitiveness.
Challenges in cotton cultivation
The cotton spinning industry in India is known for its low levels of productivity, making it challenging for manufacturers to compete with other countries. India’s cotton yield per hectare is significantly lower than other countries such as China, Brazil, and Turkey. To improve this, India needs to adopt global best farming practices to increase production and productivity. This can be achieved by revolutionising seed development, improving fibre quality through advancements in ginning, and investing in research and development throughout the entire value chain. Additionally, steps must be taken to protect crops from pests like pink bollworm, and promoting practices such as drip irrigation and high density planting. The cotton industry is also vulnerable to weather and pests, leading to fluctuations in availability and price. To mitigate this, India should explore the use of Artificial Intelligence (AI) based technology, rainwater harvesting, inter-cropping and other practices to increase cotton yield.
Challenges for cotton yarns
India is known for its strong cotton industry, with a wealth of knowledge, skills, and resources at its disposal. However, current geopolitical tensions, energy market disruptions, and monetary policy changes by central banks around the world have led to a decline in exports, particularly in the spun yarn sector. Retailers and brands have been reducing orders in the early months of fiscal year 23, leading to a 55 per cent decrease in exports of spun yarns from April to November of 2022, from 1184 million kgs to just 527 million kgs. If this trend continues, the exports of spun yarns will be the lowest in the past five years.
Balance between cotton and a manmade fibre is the need of time for holistic growth of Indian Textiles
To boost textile exports from India, there needs to be equal opportunities for both man-made fibres (MMF) and cotton to grow. Currently, the textile industry in India is heavily dominated by cotton, making up around 75 per cent of total fibre consumption. However, globally, MMF fibres make up 70 per cent of total fiber consumption. The importance of MMF for the growth of the Indian textile industry needs to be recognized as a vital growth engine and job-creating sector. The domestic industry is starting to embrace MMF as a means of growth, especially due to the high prices of cotton in recent years. To increase consumption of synthetic fibers, there needs to be an increase in production of synthetic fiber and filaments by increasing capacity for raw materials such as PTA and MEG, and polyester staple fiber. Currently, raw materials like PTA and MEG attract 18 per cent GST, polyester filament and polyester spun yarn attract 12 per cent GST while cotton dominated yarns attract 5 per cent GST. At the fabric stage, whether it’s cotton or polyester, there is a uniform GST of 5%. These inverted duty structures create huge input tax credit at various stages along the chain and is a big roadblock for investment as duty on capital expenditure is sitting as a credit which can’t be refunded or utilised. A uniform GST will remove these fiscal anomalies and will help the textile and apparel industry to grow. Ultimately, sustainability, circular economic business models, transparency, traceability, digitisation, overall competitiveness, scale, and balance between MMF and cotton will remain at the core for the Indian textile.
About the author: Balkrishan Sharma is a Joint President & Business Head at Ginni Filaments and is a recognised thought leader in textile industry with 3 decades of versatile experience in diverse domains like export & domestic marketing, commercials, operations, process control, supply chain management to name a few. He is widely travelled across 28 countries and enjoys PAN India network. In past, he has worked with Vardhman Textiles, Spentex Uzbekistan and SEL Manufacturing before moving to Ginni Filaments.
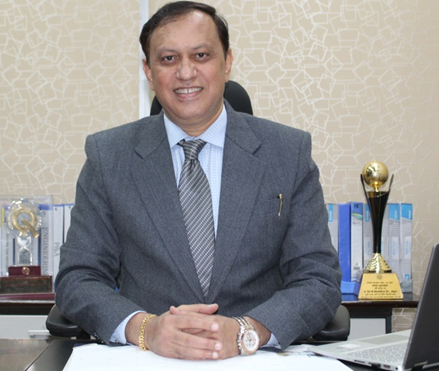