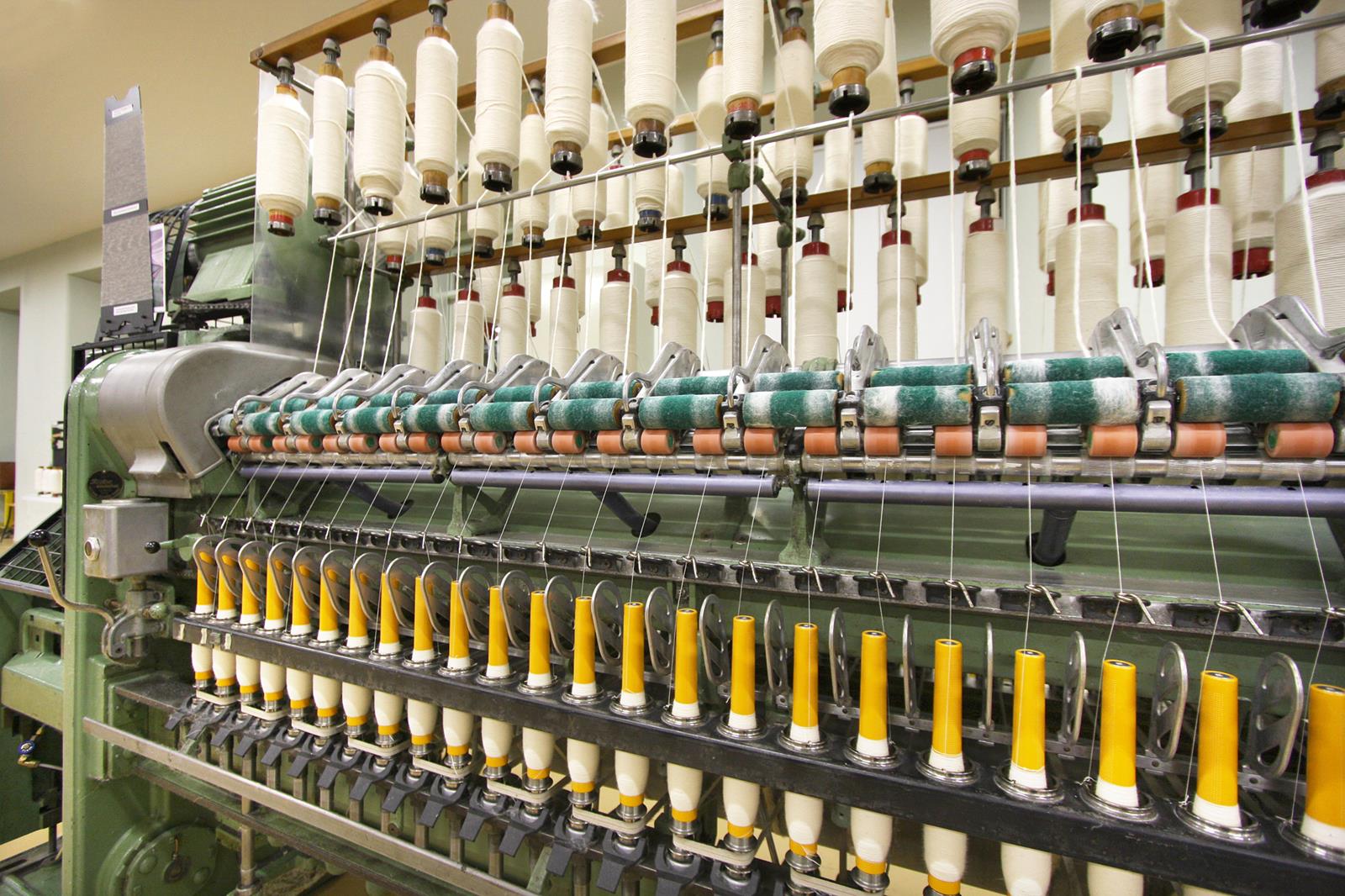
Effect of apron surface modification in ring spinning
D Jayaraman and S Balamurugan presents the use of surface modified aprons and their effect on yarn quality in the ring frame.
1.0 Introduction
In a double apron drafting arrangement, a set of aprons (bottom apron and top apron) are used to control the fibre movement in the main drafting zone. The top apron is driven by the bottom apron through frictional contact. To guide the fibres in the drafting zone, the top apron must be pressed against the bottom apron with a controlled force. It has been established that the slippage between bottom apron to top apron disturbs the movement of fibres in the apron zone, which results in deterioration in yarn quality
In the main drafting zone, the primary condition of controlling the movement of fibres between the aprons is that both the aprons should move at the same speed. If this happens, the fibre strand will also have a streamlined movement between the aprons and one can expect a controlled movement of fibres in the main drafting zone. As there is no positive transmission of motion from the bottom apron to top apron, controlling the movement of the fibres between them seems to be difficult. Due to this, there is every possibility of stick- slip effect i.e. top apron moving at a slower speed than the bottom apron, resulting in an uncontrolled movement of fibres in between the aprons. Although many research papers have been published on the effect of apron slippage on various process factors such as the influence of roving hank, break draft, etc., use of surface modified aprons and their effect on yarn quality in the ring frame has not been studied so far.
In ring frame drafting, majority of the fibres accelerate only near the leading edge of the apron cradle. At this point, if the friction is too high or low, then the fibre movement would not be uniform and can result in variations in yarn quality. In general, the coefficient of friction is higher with the materials having smooth surface at slow sliding speeds. This phenomenon was observed on the new rubber surfaces provided the surfaces are clean, dry and free from any coating like wax. Further, the explanations reveal that the highest frictions are observed on clean, smooth surfaces where the maximum actual area of contact is possible. Another phenomenon has been studied in SITRA by using Zwick instrument on the smooth surface aprons which has shown that higher stick-slip effect was observed when compared to that of the surface modified aprons.
2.0 Materials and methods
Considering this aspect, an attempt has been made to study the effect of surface modified bottom aprons of two different types and compare the same with existing regular aprons, on yarn properties such as imperfections, hairiness, tenacity, elongation and infrequent yarn faults.
Yarn samples, using three different apron combinations, are produced from 100% combed cotton material in a ring frame for warping end use. The quality attributes of the cotton used in this study are given in Table 1.
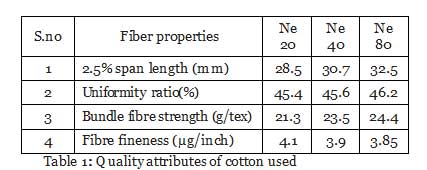
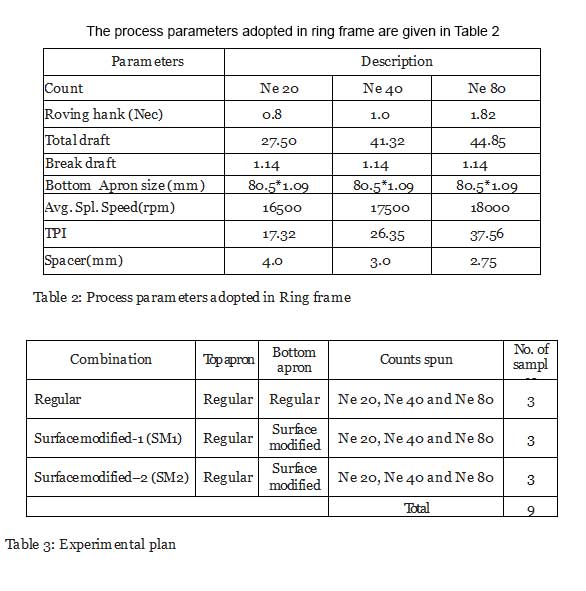
Three combed warp yarn counts (Ne 20, Ne 40 and Ne 80) are produced. In total, 9 yarn samples are produced from these three counts from each combination. For the ‘Regular’ combination, the top and bottom aprons used are of regular surfaces and for the ‘Surface modified’ combination (SM-1&SM-2) bottom aprons with modified surface and top apron with regular surface are used.
3.0 Results and discussion
The frictional characteristics of the surface modified aprons were measured using Zwick testing instrument. The testing was carried out according to DIN EN ISO 8295 standard test method. The testing speed and the gauge length were 50 mm/min and 200 mm respectively. The instrument measures the coefficient of static friction (µS), coefficient of dynamic friction (µD) , static force (FS) and dynamic force (FD). The test results of coefficient of dynamic friction (µD) for different apron surfaces with and without material are given in Figure 1.
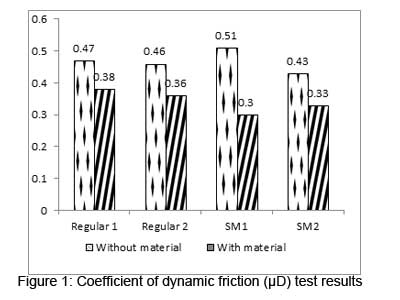
Yarn Properties | Ne 20 CW | Ne 40 CW | Ne 80 CW | ||||||
REG | SM-1 | SM-2 | REG | SM-1 | SM-2 | REG | SM-1 | SM-2 | |
U% | 8.57 | 8.6 | 8.58 | 10.63 | 10.57 | 10.71 | 13.26 | 13.38 | 13.22 |
CV m | 10.82 | 10.87 | 10.85 | 13.44 | 13.37 | 13.53 | 16.82 | 16.96 | 16.74 |
Thin-50% | 0 | 0 | 0 | 1 | 2 | 3 | 113 | 111 | 101 |
Thick +50% | 16 | 15 | 18 | 57 | 59 | 56 | 239 | 230 | 217 |
Neps+200% | 37 | 35 | 37 | 65 | 73 | 70 | 344 | 309 | 285 |
Total normal imperfections/km | 53 | 50 | 55 | 123 | 134 | 129 | 696 | 650 | 603 |
Thin-40% | 4 | 6 | 4 | 98 | 90 | 113 | 952 | 953 | 933 |
Thick +35% | 139 | 156 | 153 | 482 | 476 | 499 | 1228 | 1234 | 1178 |
Neps+140% | 131 | 126 | 133 | 316 | 323 | 350 | 1574 | 1464 | 1320 |
Total extra sensitive imperfections/km | 274 | 288 | 290 | 896 | 889 | 962 | 3754 | 3651 | 3431 |
Hairiness index(H) | 5.88 | 5.88 | 5.92 | 4.65 | 4.69 | 4.82 | 3.74 | 3.78 | 3.77 |
Zweigle S3 hairiness | 1039 | 1423 | 1342 | 941 | 1044 | 1061 | 1039 | 1113 | 1342 |
Tenacity RKM (g/tex) | 19.27 | 19.19 | 19 | 19.39 | 19.51 | 19.33 | 17.02 | 17.15 | 16.8 |
RKM CV% | 5.36 | 6.1 | 7 | 7.06 | 7.49 | 8.57 | 12.39 | 12.07 | 13 |
Classimat 5 | |||||||||
Raw material faults | 533 | 410 | 485 | 824 | 781 | 666 | 7086 | 5959 | 5817 |
Objectionable faults | |||||||||
10 class (Short thick) | 136 | 111 | 114 | 95 | 86 | 58 | 230 | 208 | 171 |
Long thick faults | 30 | 8 | 15 | 34 | 19 | 8 | 69 | 56 | 52 |
Long thin faults | 10 | 5 | 0 | 8 | 7 | 2 | 555 | 543 | 489 |
Total classimat faults/100 km | 697 | 530 | 610 | 945 | 883 | 728 | 7918 | 6748 | 6518 |
Table 4: Yarn quality results of SM-1, SM-2 & regular aprons
REG: Regular apron;SM-1 Surface modified apron 1; SM-2 Surface modified apron 2
Yarn unevenness and imperfections
Table 4 shows the yarn quality results obtained with the three combinations of surface modified aprons and regular aprons in three yarn counts. Test results reveal that in Ne 20 CW, Ne 40 CW & Ne 80 CW counts, no major difference is observed in yarn unevenness (U%) and imperfections both in normal and extra-sensitive levels between the three count combinations and aprons. A similar trend was also observed in the case of Hairiness index (H) and Zweigle hairiness (S3) values.
Yarn tenacity
Single yarn tenacity of the yarn samples are given in Table 4. Test results reveal that no major difference is observed in all the three yarn counts, Ne 20, Ne 40 & Ne 80, between the trials.
Classimat yarn faults
In-frequent yarn faults of the yarn samples were evaluated in Classimat 5 test instrument and the results are given in Table 5. It is observed that in Ne 20 CW, the total classimat yarn faults in SM-1 apron and SM-2 apron are lower by about 26% & 13% respectively than that of the regular apron. In Ne 40 CW count, the total classimat yarn faults of SM-1 & SM-2 are lower by about 7% and 23% respectively than that of the regular apron process. Similarly, in Ne 80 CW count, the total classimat yarn faults of SM-1 & SM-2 are also lower by about 14% and 17% respectively.
Short thick objectionable faults (10 classes) in all the three yarn counts (Ne 20 CW, Ne 40 CW & Ne 80 CW) are lower by 18%,16% & 10% using surface modified apron (SM-1) than that of the yarns produced using regular aprons. Similarly, surface modified apron (SM-2) has also shown lower yarn faults in all the three yarn counts by about 16%(Ne 20), 39%(Ne 40) & 26 %(Ne 80) than that of the yarns of the same counts produced using regular aprons.
Long thick faults in all the three yarn counts (Ne 20 CW, Ne 40 CW & Ne 80 CW) were lower by 73%, 44% and 18% using surface modified apron (SM-1) than that of the yarns produced using regular aprons. Similarly, surface modified apron (SM-2) showed lower long thick yarn faults by about 50%, 76% & 25% than that of the regular aprons.
Long thin faults in all the three yarn counts (Ne 20 CW, Ne 40 CW & Ne 80 CW) using SM-1 are lower by about 50%, 13% & 2% than that of the yarns spun using regular aprons respectively. Similarly, in surface modified apron SM-2 has shown lower long thin faults by about 100%, 75% and 12% than that of the regular apron respectively.
Industrial trial results
Trials were conducted outside SITRA in an industrial set-up for various counts using SM-2 bottom apron and regular bottom aprons and the results are given in Table 5. For these trials Ne 40 KH-Comp., Ne 60 C-Comp. and Ne 100 C-Comp. counts were spun.
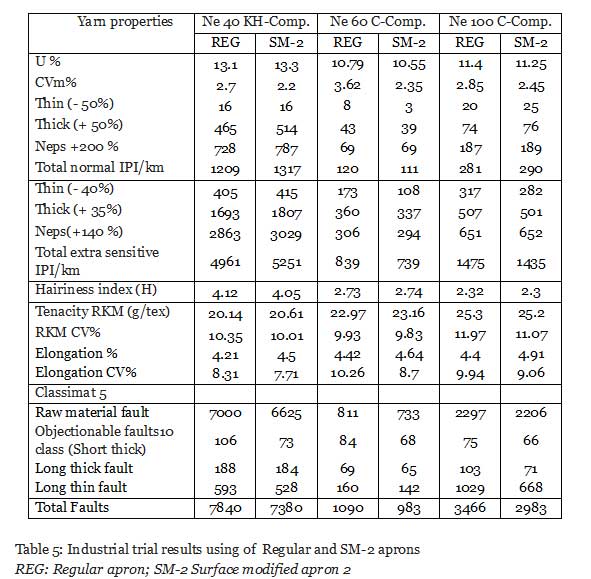
Yarn unevenness and imperfections
No major differences were observed in yarn unevenness (U%) and imperfections both in normal and extra-sensitive levels between the three count combinations and aprons. A similar trend among the three different combinations was also observed in the case of Hairiness Index (H).
Yarn tenacity
Single yarn tenacity of the yarn samples are given in Table 5. From the test results, it is observed that in all the three yarn counts, Ne 40 KH-Comp., Ne 60 C-Comp. & Ne 100 C-Comp., no significant difference is observed in yarn tenacity between the trials.
Classimat yarn faults
In-frequent yarn faults of the yarn samples evaluated in Classimat 5 test instrument are given in Table 5. It is observed that in Ne 40 KH-Comp. count, the total classimat yarn faults in SM-2 apron was lower by about 6% than that of the regular apron. In Ne 60 C-Comp. & Ne 100 C-Comp. counts, the total classimat yarn faults of SM-2 is lower by about 10% &14% respectively than that of regular apron.
Short thick objectionable faults (10 classes) in all the three yarn counts (Ne 40 KH-Comp., Ne 60 C-Comp. and Ne 100 C-Comp.) were lower by 31%,18% & 12% in Ne 20, Ne 40 and Ne 100 respectively using surface modified apron (SM-2) than that of the yarns produced using regular aprons. Long thick faults in all the three yarn counts were lower by 3%, 5% and 31% in Ne 20, Ne 40 and Ne 100 respectively using surface modified apron (SM-2) than that of the yarns produced using regular aprons. In case of long thin faults in Ne 40 KH-Comp. and Ne 60 C-Comp. counts, SM-2 apron was lower by about 10% and in Ne 100 C-Comp. count it was lower by about 35% than that of the regular apron process.
4.0 Conclusion
The following are conclusions of the study,
- A noticeable reduction in total classimat faults was observed in all the trials conducted using surface modified aprons.
- Surface modified aprons registered lower short thick objectionable faults (10 classes) than that of the regular aprons in the range of 10% to 39% between various counts.
- Surface modified aprons showed lower long thick faults in the range of 3% to 76% between different trials than that of the regular aprons.
- Surface modified aprons showed lower long thin faults in the range of 2% to 100% than that of the regular aprons in all the trials.
- No major differences were observed in yarn unevenness, imperfections, hairiness index (H) and yarn tenacity between the yarns spun out of surface modified and regular aprons.
About the author:
D Jayaraman has 36 years of textile industry experienxe in spinning mills, textile machinery manufacturer and Research organisation. He is currently working as the Deputy Director & HOD spinning division and HOD in-charge of weaving & knitting division in SITRA.
S Balamurugan holds 25 years of industrial experience and presently working as a Senior Scientific Officer in a world renowned textile research institute in south India.