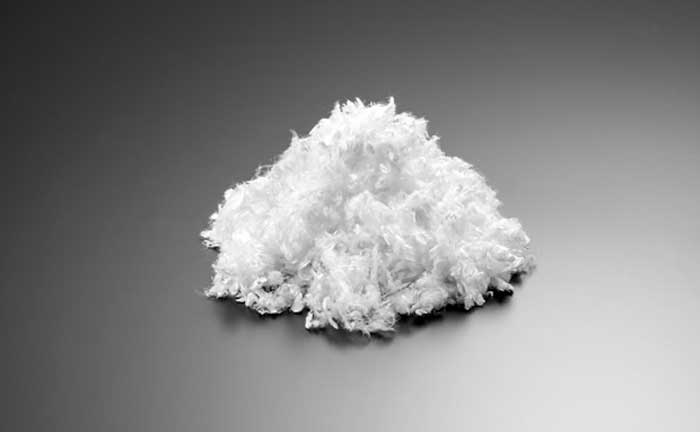
Exploring Polyolefin Fibre Applications
Polyolefin fibres are primarily aliphatic polymeric hydrocarbons that are composed of at least 85 per cent by mass of olefin units.
The word “olefins” derive from the French “oléfiant” (oil-forming) and commonly known as “alkenes” (ethylene, propylene, isoprenes, butenes, etc.) are the hydrocarbon with at least one carbon–carbon double bond in their structure. The molecules with a double bond at the first (alpha-) carbon are denoted as alpha (α-) olefins. Polyolefins are thermoplastic polymers formed by the addition polymerisation of these reactive double bonds of olefins. The natural carbon supplier crude oil and gas are the main resources of these monomers. Polyolefins are commonly perceived as commodity polymers, have a diverse range of unique features, are inexpensive, and have a large variety of applications. The chemical nature of polyolefins is more advantageous to other plastics, such as polyurethanes, polyamides, and polyvinyl chloride (PVC) for their very simple composition of carbon and hydrogen.
Polyolefins derive their excellent physical properties from a large variety of molecular chain arrangements with branching. Branching is caused by the radical transfer that highly influences the physical properties and ensures a variety of olefinic polymer sets with varied expedient functionalities. The recyclability of polyolefins is one of the key advantages, which is accelerating the zero-landfill milestone of modern sustainable earth. Among various types, polyethylene (polymerised ethylene) and polypropylene (PP) (polymerised propylene) are well-known as widely used polyolefins. Worldwide abundant resources of crude oil and natural gas ensure an easy and large volume supply of raw materials for polyolefin production, however, depletion of resources might be an issue in the future. The global demand for polyolefins is increasing day by day due to their low cost, availability with a huge volume, lightweight, large variety of functionalities, high chemical resistance, and promising physical properties. With a clear tendency of growth, around 63 per cent of annual global polymer demand is fulfilled by polyolefins that cover the daily needs of nearly every aspects of our modern lives. Only a mere change in fibre diameter to nanometre ranges results in an sharp increase in specific surface area, surface functions, cohesiveness, and even mechanical properties. During filtration or separation, the outstanding surface covering provided by the nanofibre’s high surface-to-volume ratio serves as a potential barrier against the targeted fine particles and microorganisms. Due to these characteristics, polyolefins have demonstrated their promise as nanofibres and have been used in various high-performance applications, including oil–water separation, bio-filtration, personal protective equipment, drug delivery, power storage, etc. where the smaller fibre diameter is highly valued.
There is a perceived dearth of review papers on polyolefins in the scientific literature, despite their rising demand. Brown and co-workers have completed a full review of melt-electrospun polyolefin nanofibres. A thorough overview of the developments in melt-electrospun nanofibres and their potential uses was provided by Zhang et al. However, melt electrospinning of polyolefin nanofibres has been the subject of a few reviews, but the discussion about solution electrospinning for this material has not been investigated. This is a significant area for possible review studies since solution electrospinning has the potential to give distinct benefits in terms of fibre morphology control and the capacity to integrate diverse functionalities. So, a comprehensive review of developing advanced polyolefin nanofibre should discuss both melt and solution electrospinning and their benefits and drawbacks. Furthermore, numerous books on polyolefins have been published. However, a comprehensive discussion of all classes, forms, and areas of application in a single frame is noticeably absent.
Polyolefins are an active area of research; nevertheless, there is a significant shortage of published comprehensive review papers. This discrepancy highlights the need for an up-to-date and in-depth overview of recent advancements and the state-of-the-art techniques in polyolefins. The objective of this review paper is to present a comprehensive analysis of two significant research advancements in the field of polyolefins: the synthesis and novel applications of polyolefin fibre and nanofibre. This review paper can fill a void in the literature by providing a comprehensive analysis of these critical areas. Besides, the major advancements and applications of polyolefins in various areas, including home, industry, automotive, agriculture, filtration, bio-medical, protective clothing, and power storage have been summarised in this study. Moreover, this review concludes with a concise overview of recent developments in polyolefin electrospinning and their potential implementation in the form of polyolefin nanofibres. A meticulous discussion of the challenges, potential remedies, and prospects in the electrospinning of polyolefins has also been delineated in the current review.
Polyolefin fibres
Polyolefin fibres are primarily aliphatic polymeric hydrocarbons that are composed of at least 85 per cent by mass of olefin units. The US Federal Trade Commission defined polyolefin fibre as “A manufactured fibre in which the fibre-forming substance is any long chain synthetic polymer composed of at least 85 per cent by weight of ethylene, propylene or other olefin units”. Among the polyolefin fibres, commercially PP is considered the most significant fibre, and to a lesser extent, polyethylene (PE). Polyolefin fibres are well-known in the field of textiles due to their inherent high tensile strength (both wet and dry) and hardness, good abrasion resistance, and excellent chemical and stain resistance properties. Therefore, these fibres replaced both natural and other existing manmade fibres rapidly in various potential textile applications from the very beginning of their commercialisation. In recent times, the development of advanced and innovative textile products based on polyolefin fibres has been eagerly welcomed by the majority of global consumers. The polyolefin fibres are mostly made of isotactic polypropylene, ultra-high molecular weight polyethylene, and high-density PE. In commercial textile applications, however, the significance of other alpha-olefin polymeric fibres compared to PP is very low. According to the report of the China Chemical Fibre Association, about 95 per cent of polyolefin fibres are PP, including staple fibres and filament yarns, which fulfill at least 6 per cent of global annual fibre production demand.
Polyethylene fibre: Polyolefin monofilament extruded from low-density polyethylene (LDPE) was the first textile fibre developed in 1930s. However, these LDPE fibres gained limited attention initially for commercial purposes due to their coarseness and poor mechanical properties, as the fibres were derived from the low molecular mass polymer. Some high-density polyethylene (HDPE) fibres and ribbons were commercialised at that time namely, “Courlene” and “Reevon”. However, the expedient applications of HDPE monofilaments as a general textile fibre were restricted due to their low resilience, poor softening range, and high deformation against stress (creep). Nevertheless, these coarse monofilament/ribbon-like polyolefin fibres were widely utilised as outdoor fabrics, protective clothing, filter fabrics, ropes, webbing, nets, cordage, conveyor belting, and seamless medical tubes. Linear low-density polyethylene (LLDPE) monofilaments, ribbons, and slit-film weaving tape were also introduced in a small quantity for non-textile applications. Since various types of ropes, nets, and cordages that were generally manufactured from natural fibres were replaced by HDPE monofilament, and its weaving tapes became popular for fabricating diverse industrial fabrics like tarpaulins, shade mesh fabrics, and geotextile membranes.
Although the theoretical evidence of high modulus polyethylene fibres has been available since the 1930s, the ultimate outcomes were found in the mid-1980s, when the commercial ultra-high molecular weight polyethylene (UHMWPE) fibres were developed with suitable spinning techniques. Research and development of high-performance UHMWPE filament fibres have continued on many fronts. In 1970, high-modulus polyethylene fibres were commercialised by Ward et al. and received their license as Tenfor and Certran. However, during the production, the high melt viscosity and intermolecular entanglement of UHMWPE significantly hampered the extrusion and subsequent drawing for the orientation of fibres. Therefore, the gel spinning process was introduced, which solved all of the deficiencies, and successfully developed high-strength, high-modulus polyethylene fibres in 1981. The revolution in the PE fibre industry was then initiated, and to date, the UHMWPE fibres are commercially renowned as Dyneema and Spectra in the global market. The development of ultra-high modulus fibres and yarns like Dyneema, Spectra, and Tensylon extended the scope for using polyolefins in a high strength demanding applications, including antiballistic fabrics, deep-sea mooring ropes and braids, and highly efficient medical devices. The common trade names of UHMWPE include, Dyneema, DyneemaPurity by DSM, Spectra by Honeywell, and IZINAS by Toyobo.
The SEM illustration of commercial Dyneema fibre is shown in Fig. 1a. The gel-spun UHMWPE fibres are lightweight with zero moisture regain and have high strength, which is generally considered as a strong competitor of carbon and kevlar fibres in the application field of protective clothing and high-performance sails as shown in Figure1g. Fibrous armor plates are more promising for bulletproof vests where the perpendicular direction of fibre arrangement can perfectly resist fast projectiles. Indeed, Dyneema fibres have many successful applications as a typical armor material. Using the easy creeping property of gel-spun UHMWPE, the helmet shell has been made by cross-ply fibre arrangement and creep-forming process at about 130 ℃ as shown in Fig. 1b, c, d. Here, the low melting temperature drawbacks of UHMWPE are turned into an advantage as easy shaping, fusing, and simultaneous cutting of edges. The chemical and abrasion resistance makes the ropes made of these fibres more attractive and a good alternative to cables and metal wires in corrosive environments. Metal shackles are widely used as connections and load-bearing materials; however, they are hard, heavy, permanent, and environmentally hazardous. Soft shackles made from gel-spun UHMWPE fibres are a potential alternative for their high tensile strength, extreme damage tolerance even light and slippery properties. Moreover, such soft shackles can easily be opened even after a heavy loading, as shown in Fig. 1e, f. Mooring ropes of IZINAS are much lighter than wire, safer to handle, and can be used without greasing, making them ideal for use on ultra-large vessels like ore carriers, crude oil tankers, and LNG tankers as shown in Fig. 1h. The thermal conductivity coefficient of IZINAS is approximately four times higher than that of standard materials. In laboratory tests, the ICEMAX fabric formed by combining IZINAS with special fibres provides twice the cooling sensation of traditional materials as shown in Figure 1.
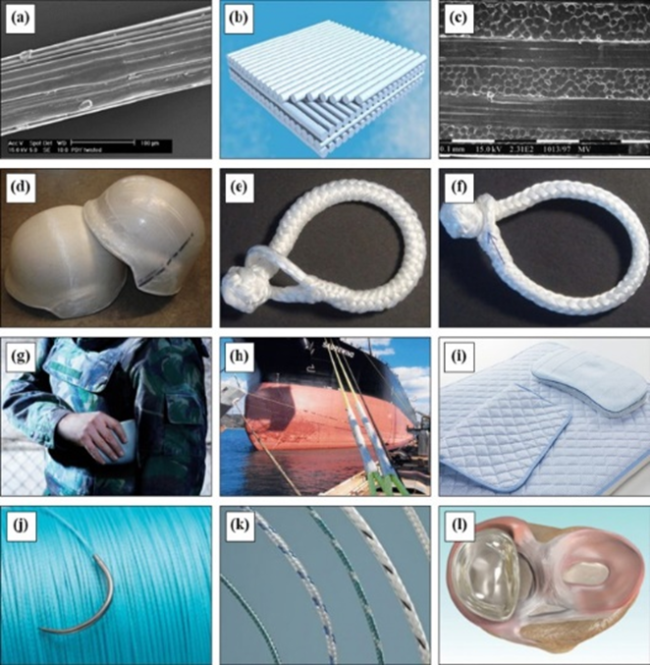
Figure 1: a-SEM image of a Dyneema monofilament, b-illustration of fibre cross plies for armor, c-SEM micrograph of a cross section of Dyneema monofilament, d-Two helmet shells made by creep-forming of gelspun UHMWPE fibres, e-Soft shackle made with UHMWPE h-Mooring rope of IZINAS used for ultra-large ships. Courtesy of Toyobo, Japan, i-ICEMAX fabric made by combining IZINAS with special fibres for high sensation of coldness. Courtesy of Toyobo, Japan, j,k, Braided surgical suture from blue Dyneema Purity fibres. Courtesy of DSM, Netherlands, l-Dyneema Purity fibre reinforced implant used for meniscus replacement. Courtesy of Active Implants
The medical grade gel-spun UHMWPE fibre is known as Dyneema Purity as shown in Figure 1 j, k, l. This fibre is considered as a gold material for medical applications because of their fitness, high strength, abrasion resistance, low elongation and good compatibility with human body over the longer lifespan. Very common and recent surgical applications of Dyneema Purity fibre includes surgical sutures, surgery of the spine, arthroscopic procedures, ligament repair, trauma, and implant reinforcement.
Polypropylene fibre: Polypropylene was first discovered in 1951 and commercially appeared as a superior plastic material in 1957. The first PP monofilaments for textiles, however, began to appear in the market in the late 1950s. In the early 1960s, PP in the form of staple fibres and multifilament was produced in small quantities in Italy, UK, and USA for use in textiles. The first commercial multifilament and staple fibres from isotactic polypropylene were melt-spun employing similar equipment and techniques that were commonly used for polyamide and/or polyester fibres. The innovative use of PP in textiles was started when continuous PP tape yarns (ribbon) with high strength were invented from the extruded film in the late 1960s. In the early 1970s, the revolutionary growth of PP tape and nonwoven fabrics ultimately eliminated the use of traditional jute yarn and fabrics and supplanted it with the new polyolefins in the textile industry. Consequently, the most renowned jute carpet backing and sacking cloth was substituted by PP tape fabrics. Moreover, the cords, rope, and twines prepared from natural fibre spun yarn was replaced by PP tape yarns in many cases. This revolution of polyolefin tape yarns crossed the border of Europe and North America within a short period and spread to the whole world.
However, the PP tape yarns prepared from the extruded film were not considered as textile fibre or yarn due to their irregular cross-section, size and shape, less luster, and rough textures. Subsequently, the continuous filament tows were prepared from polymer melt of solid PP granules using a spinneret plate with cooling air stream. ‘James Mackie & Sons’ company introduced a system to prepared PP staple fibre and commercialised rapidly, through which in-house PP fibre supply was easily available globally to the spinners. The industrialisation of PP textile products through weaving, spinning, and carpet manufacturing, was initiated in the mid-1970s and well established by the late 1970s. During the 1980s, the industrial expansion of PP was stimulated by a wide range of innovative products utilising industry-oriented innovative research and development.
The PP fibre available in a variety of renowned textile forms is mainly prepared from isotactic PP. Currently, PP fulfills approximately 6 per cent of global annual fibre production demand in a weight of 4.3 million tons; mostly filament yarns and a lesser amount of staple fibres. Textile fibres made of PP, in particular, have been progressively well-known to consumers and manufacturers because of their huge applications in carpets and nonwovens. Replacing nylon and jute, PP aggressively captured the largest market of carpets and nonwovens for use in a large variety of products, including wet wipes, baby diapers, hygiene fabrics, and adult incontinence fabrics. PP fibres also have prominent textile applications, such as disposable hospital equipment, geotextiles, automotive fabrics, and industrial wipes.
Polyolefin blend fibre: Polyolefin blend fibres are another types of fibrous material prepared by adding another polymer to polyolefin solution before spinning in order to enhance or improve some aspects of targeted functionalities, physical characteristics, degradability, and applicability. Polymers having miscibility with polyolefin can easily be employed to develop blend fibres with desired characteristics, but in practice, a few miscible polymer pairs are available for such purposes. Hence, the addition of compatibiliser for immiscible polymers, as a third particle, is considered the best technique for fabricating the alloy fibres with enhanced physical properties. The melt blending a mix of ‘additive master batches’ to the main polymer is a long-established and renowned method for the manufacturing of polyolefin textile materials. To prevent the longitudinal fibrillation of PP slit film yarns, 2–3 per cent PE is commonly added from long time ago. The addition of 20 per cent polyethylene terephthalate (PET) to PP has enhanced the tensile properties of PP/PET alloy tapes which are more prominent as carpet backing, ropes, and engineering fabrics. In 2007, a Chinese patent first demonstrated PP/PET blend fibres with a 30 per cent increment in tensile strength of alloy fibres compared to pure PP fibres. Likewise, melt blend fibres of 92 per cent PP and 8 per cent atactic polystyrene significantly improve the creep resistance and rigidity of the developed fibres. Another potential PP/polystyrene melt blend fibres with only 5.0 per cent polystyrene demonstrated the reduction of undrawn fibre crystallinity, which was employed to assist the texturising of PP multifilament yarns. A variety of alloy fibres was also drawn using different ratios of PP/liquid crystal polymers, PP/HDPE, iPP/aPP, and iPP/polylactic acid (PLA) blends for enhancing mechanical properties and biodegradability of fibres.
About the author:
- Dr N Gokarneshan is from the Department of Textile Chemistry, SSM College of Engineering, Komarapalayam, Tamil Nadu.
- S Karthikeyan and K Sakthivel are from the Department of Petrochemical engineering, SSM College of Engineering, Komarapalayam, Tamil Nadu.
- M Sakthivel and R Devaki are from the Department of Textile Technology, KSR Institute of Technology, Tiruchengode, Tamil Nadu.
- Dr U Ratna is from the Department of Textiles and Clothing, Avinashilingam Institute of Home Science and Higher education of women, Coimbatore, Tamil Nadu.
- Dr D Anita Rachel is from the Department of Fashion Design, Footwear Design and Development, Noida, Uttar Pradesh.