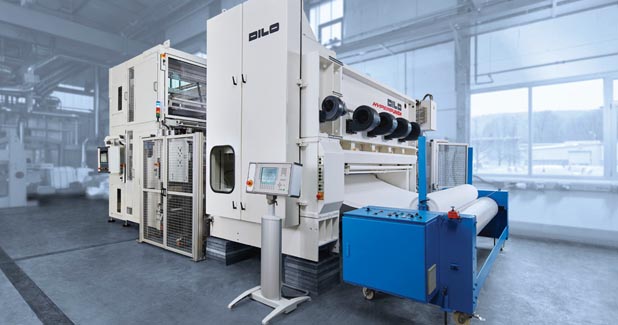
DiloGroup’s revolutionary innovative technology
DiloGroup, consisting of DiloSpinnbau, DiloTemafa, DiloMachines and DiloSystems, offers production machinery for complete processes to make needled staple fibre nonwovens, from fibre preparation, to carding, crosslapping or aerodynamic webforming, needlepunching or other consolidation technologies for any fibre material.
like DI-LOUR, DI-LOOP and Hyperpunch have created
new markets for the nonwovens industry and have contributed to continuous growth.
With its recent developments DILO is continuing
this strategy of high-quality engineering and revolutionary innovative technology. The H Alpha loom
is a new variation of Hyperpunch technology. By
reducing detrimental draft, increasing throughput
speed and lowering costs, it is of interest for
universal applications.
The surface quality of nonwovens is an important parameter and highly influenced by the needle pattern. The new needle pattern “8000X†can be considered
a breakthrough for realising very uniform stitch distributions over a wide range of line speed. The related “6000X†is suitable for Hyperpunch needle looms.
The Hypertex technology combines a grid of endless fibres and nonwoven fabric as a sandwich using the needlepunch process. An additional weaving process becomes unnecessary. The grid improves the tensile strength of products such as filters or roof sheets and
will lower costs and production time.
In the field of “textile additive manufacturing†the “3D-Lofter†will offer further chances of fibre savings
for needle felts used in the automotive and other applications because topologically distributed fibre masses can be positioned in the felt where needed by
so called “individual web forming spotsâ€.
“diloline 4.0†includes a wide variety of “smart manufacturing†actions in collaboration with Siemens which all aim at further simplifying operation, increasing transparency in web forming and consolidation thereby increasing efficiency. Production data are stored, documented and compared. An “alarm monitor†indicates irregular behaviour. A production analysis documents
the reasons for standstill times. This data can be used
to avoid irregular behaviour. Numerous information modules can be recalled via mobile apps and cloud data (mindSpheres). All these methods to control the machines and to generate production data will be helpful to further secure the complex functions within the production system independently of personnel and shift.