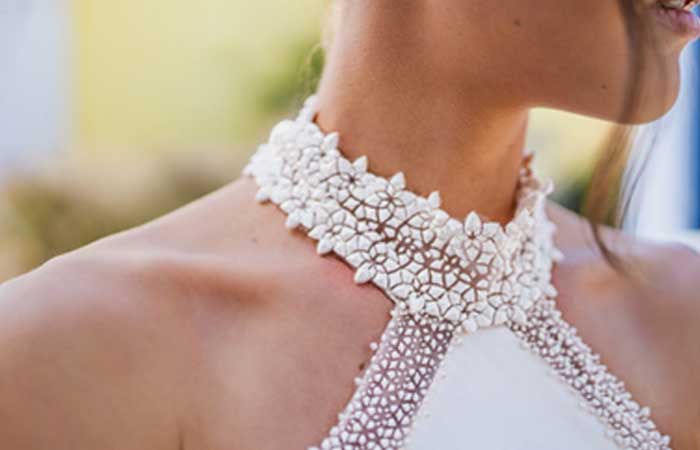
3D printing for sustainable fashion
Collective efforts from fashion designers and material scientists can bring in scalable 3D printing techniques for textile production that are economical and eco-friendly at the same time, says Dr Ashok Athalye and Shriyasha Tari.
3D printing is a computer-controlled manufacturing technique that deposits layers of materials to create three-dimensional objects. As the layers add up sequentially to create 3D objects, it is also called Additive Layer Manufacturing (ALM) or Additive Manufacturing (AM). This technique has revolutionised several industries by cutting down the manufacturing setup and reducing resources, manpower, and waste.
The apparel and clothing industry is not an exception to the notable advancements made by 3D printing. The features of 3D printing like minimum waste generation, raw material optimisation, and the ability to create specific customisations in designs have garnered the interest of fashion designers worldwide. The 3D printing technique was invented in the 1980’s but its integration into the textile industry started in the early 2000s. Conventional textile manufacturing is known for its highly energy-intensive and water-consuming processes. The fashion industry is also infamous for its solid waste generation and textile waste dumping, landfilling and incineration. Amidst all these challenges, 3D printing has proved to be a boon for the fashion industry.
This article summarises how 3D printing is transforming fashion and helping brands and fashion designers to achieve sustainable development goals. Right from the lab innovations made in 3D garments to their display at the recent Cannes Film Festival and MET Gala 2024, it is evident that 3D printing technology is set to revolutionise the textile and fashion industry. Some limitations of 3D printing technology for bulk-scale textile production are also discussed.
Recent developments have focused on material and process improvement in garment making. Researchers are constantly working on creating sustainable wearable materials for 3D printing. Thermoplastic materials like polypropylene, acrylonitrile butadiene styrene (ABS) plastic, nylon, and thermoplastic polyurethane (TPU) are the preferred choice for 3D printing. The focus on creating biodegradable materials has encouraged the widespread use of biodegradable polymers like Poly Lactic Acid (PLA).
So far, techniques like Fused Deposition Modelling (FDM) and Stereolithography (SLA) have been explored for textile 3D printing. These techniques enable the printing of single thermoplastic or thermoset polymers under the effect of heat or light. Objects made from single kinds of thermosensitive polymers or photo-curable resins could be manufactured using these conventional 3D printing techniques. Some of the machinery manufacturers and systems enabling fashion designers to integrate 3D printing in textile and apparel designing are enlisted below:
- WASP 2040 PRO- Small scale FDM 3D printer used for ABS, PLA, polyamide, carbon, and polyethylene terephthalate glycol fibres.
- Sinterit’s Lisa Pro System based on selective laser sintering.
- Stratasys’s J55 Prime PolyJet system is capable of processing five different types of materials directly on fabric and printing more than 640,000 color combinations using the Pantone System and cyan, magenta, yellow, and key (CMYK) model
Researchers are working on further optimising these techniques by making advancements in multi-material 3D printing. Multi-material 3D printing allows simultaneous printing of different materials of varying textures and properties within a single garment. Developments in high-resolution 3D printing techniques like Digital Light Processing (DLP) and Selective Laser Sintering (SLS) techniques are promising solutions to produce finer and more intricate textile patterns that were previously difficult to achieve. These are very helpful in creating functional fabrics.
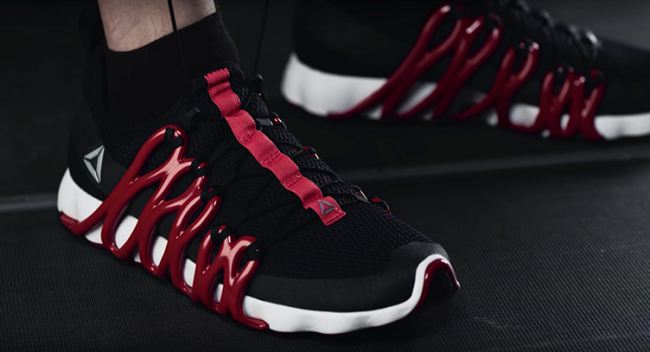
Reebok’s Liquid Factory 3.0 uses 3D printing technologies to produce shoes with minimum material waste.
Due to the ease of quick prototyping, 3D printing has gained wide attention in the footwear industry. Rothy’s 3D-Knit Footwear, Ecco’s Quant-U Custom Shoes and Nike’s VaporFly Elite Flyprint are some shoe collections that depict the potential of 3D printing in the footwear industry. The problem of micro-plastic pollution in oceans and their bioaccumulation is a major environmental concern. To address this challenge, Adidas collaborated with Parley for the Oceans to create 3D-printed shoes using recycled ocean plastics. Similarly, Reebok’s Liquid Factory 3.0 uses 3D printing technologies to produce shoes with minimum material waste. This process significantly reduces material waste and the carbon footprint compared to traditional shoe production. The fashion brand Phable utilises 3D printing to reduce waste during garment production. The brand designs clothes that are printed in a single piece, thus eliminating fabric scraps and waste cloth cuttings.
In recent years, scientists have explored biomaterials that mimic nature and tend to be more resilient. Such biomaterials are created by incorporating biological cells within a non-living matrix. Researchers from Post Carbon Lab have developed photosynthetic textiles using algae 3D printing. The applied layer of algae on clothes allows the textile material to breathe like plants. The algae on the textile surface inhale oxygen and exhale carbon dioxide mimicking trees during daytime. Such textiles can contribute to carbon sinking.
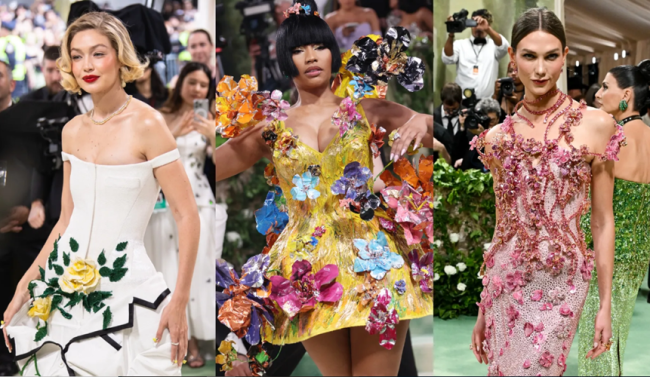
3D floral dresses at Met Gala 2024.
There’s no doubt that 3D printing has inspired brands and fashion designers to achieve sustainability. The very recent Cannes Film Festival and MET Gala 2024 showcased the world’s first fully 3D-printed wedding dress designed by Iris van Herpen. The Dutch designer is well known for experimenting with 3D printing in the fashion industry. Sustainable characteristics like on-demand production and minimum waste generation have also inspired brands like Zara and H&M to manufacture 3D-printed fashion accessories and embellishments. Apart from conventional apparel manufacturing, 3D printing is also being used for producing smart textiles like wearable electronics and clothes embedded with sensors for health and wellness monitoring.
Though the 3D printing technique brings sustainability in manufacturing and gives creative liberty to fashion designers there are certain challenges still prevailing around this additive manufacturing technique.
- The production of garments using additive manufacturing is still in its infancy stage
- 3D printed textiles often lack the required comfort of wearable garments
- Replicating fabric-like properties in 3D-printed textiles
- Reproducibility and consistency of results
Conventionally manufactured garments are desirable because of their softness, feel, and breathability. Although, the developments in multi-material 3D printing are appreciated the same multi-materials are a challenge for separation and effective recycling at the waste management stage. The major used materials for 3D printing are plastic-based filaments which add to the existing problem of plastic pollution. Scaling up 3D printing technology is thought to be not so feasible because of factors like expensive 3D printing machinery, the need for techno-savvy personnel and a slower production rate. Also, the existing 3D printing machinery is suitable for bespoke and small-scale production. Variations in 3D printing can produce inconsistent batches which is undesirable in textile production.
Though 3D printing gives creative freedom to designers to customise designs there are certain limitations. Some 3D printing software is complex and may require specialised skills. Designers accustomed to conventional designing techniques need specialised training to effectively use 3D printing for textile designing. The support structures needed during 3D printing are dissolved using solvents and removed once the main design is created.
3D printing is known to be a sustainable technique to minimise waste during production, however, it can be highly energy intensive. High temperatures and intense light radiations are used to solidify the 3D-printed textiles. Thus, 3D printing is a promising solution to address some of the challenges of the fashion industry. Collective efforts from fashion designers and material scientists can bring in scalable 3D printing techniques for textile production that are economical and eco-friendly at the same time. Innovations that can change the consumer’s perceptions towards garments manufactured using 3D printing technology are needed for wide acceptance of this additive manufacturing technique specifically for textile production.
Acknowledgment
The author would like to thank the Institute of Chemical Technology (ICT) Mumbai for providing this opportunity to share relevant information.
About the author
- Shriyasha Tari is a Doctoral Research Scholar and a DST Inspire Fellow.
- Dr Ashok Athalye is a Professor of Textile Chemistry and Vice-President of Technological Association (ICT- Mumbai), Fellow of the Society of Dyers and Colourists (FSDC-UK) and Fellow of the Indian Chemical Society (FICS)