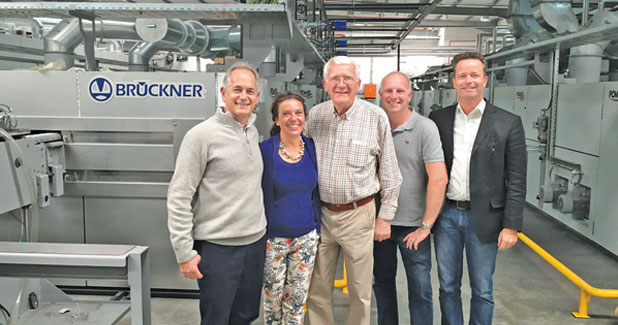
SA firm rises like Phoenix with Bruckner stenters
The South African company Rotex Fabrics recovers with Brückner stenters rapidly from a terrible fire and is now stronger than ever.
The South African company Rotex Fabrics recovers with Brückner stenters rapidly from a terrible fire and is now stronger than ever.
Rotex Fabrics (Pty) Ltd is a knitter, dyer and finisher of high quality fabrics for fashion and sports-wear, who believe in establishing meaningful, long-term relationships with customers and suppliers. The purpose built production facility is situated in the Atlantis industrial area, 50 km north of Cape Town CBD/ South Africa. The company was incorporated in 1980. Rotex prides themselves in the fact that they are constantly developing new fabrics to keep up with the ever-changing fashion and technical requirements of their customers. The fabrics are circular knitted in house, exhaust dyed and then finished in open width. The majority of the fabrics produced contain elastane with a combination of cotton, viscose, polyester, nylon or acrylic. All cotton/elastane fabrics are bio-polished using enzymes.
In October 2016, there was an unfortunate fire where the complete dye house and finishing departments were destroyed, but fortunately nobody was injured. After re-constructing the damaged buildings, the company started with the installation of the new machinery by the end of April 2017, with the last of the new machines being commissioned exactly one year to the day after the fire. Three months prior the fire, Rotex started their partnership with Brückner, and commissioned a new 8-chamber, thermal oil heated stenter to complement the two existing lines.
The Technical Director, Martin Rohner says: “We were impressed with the new machine, as well as the service and back-up from Brückner, so much so, that when we had to replace the damaged machines, it was an easy decision to make, with the result that we installed two identical Brückner stenters. The new investment has enabled us not only to install the latest technology throughout our dyeing and finishing facility, but also to optimise the plant layout and grow our capacity to meet our customers’ growing need for high quality, fashion forward, quick response fabrics.â€