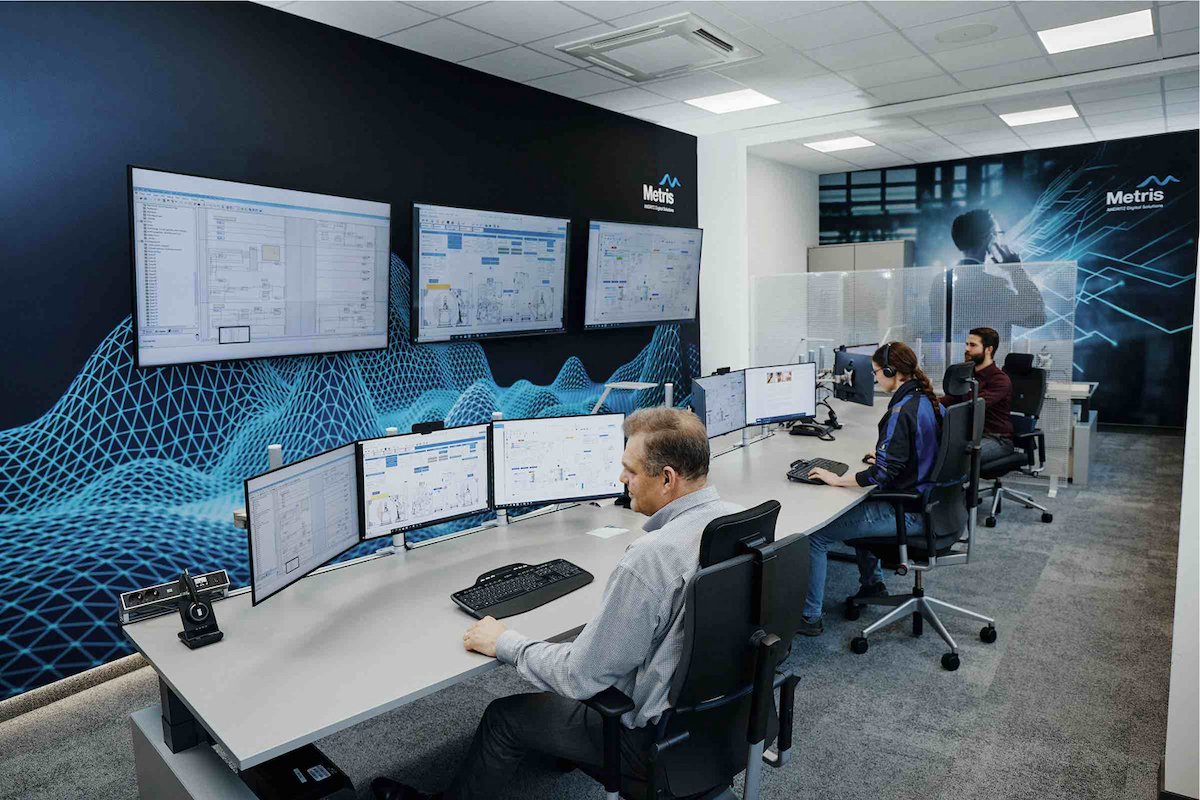
Energy remains a top priority
Despite a fall in energy prices from the highs of 2022, they will remain a major topic at INDEX 23, in parallel with the push to achieve further CO2 reductions across the supply chain, according to members of the show’s advisory board.
On the technology front, Andritz Nonwoven is among machine builders continuing to develop new solutions to support customers in saving energy.
One example is the company’s patented neXecodry system which optimises the dewatering process after hydroentanglement and ensures faster drying of the solidified web, while simultaneously reducing energy consumption throughout the drying process.
“The aim is not to leave the heat energy produced in the manufacturing process unused, but to use it in a loop,” explains the Laurent Jallat, Head of Marketing. “This achieves two things – savings in energy consumption of up to 22 per cent and a faster drying process to increase production capacity.
The system is available for any of the company’s Spunlace and Wetlace line configurations and can also be retrofitted to existing lines.
Data
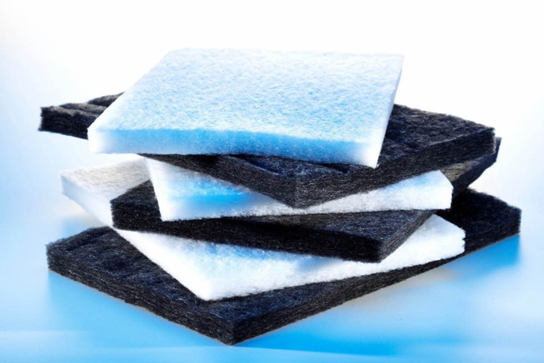
“Our Metris digital solutions are also a game changer for whatever nonwovens process a customer operates for enhancing line efficiency to reduce raw material consumption and waste generation,” Laurent Jallat adds. “The Metris UX platform can retrieve all necessary data relating to energy consumption and control it more efficiently, whether we talk about water, electricity or gas. At INDEX 23, visitors will have the opportunity to attend live demonstrations of the Metris portfolio at our stand.
“Our R&D department focuses on searching for innovative sustainable solutions for energy savings and using valuable resources as economically and efficiently as possible to help our customers to contribute towards decarbonisation or carbon neutrality.”
Alternatives
As a leading nonwovens rollgoods manufacturer Germany’s Sandler AG has energy management systems in place which make it possible to determine energy costs in relation to individual product groups and technologies.
“This offers opportunities to work on alternative solutions in close cooperation with our customers which we look forward to discussing with them in Geneva,” says Dr Ulrich Hornfeck, Member of Sandler Management Board. “Despite all the turmoil on the energy market last year, we succeeded in ensuring security of supply for our customers by preparing for and quickly reacting to the aggravated situation in Germany at an early stage”.
“Being an energy-intensive company, it is our responsibility to make our production processes highly efficient through the use of energy-efficient modules, state-of-the-art production and measurement technology and online monitoring systems.”
Digital monitoring
As a supplier of adhesives for nonwoven-based disposables, Henkel also continuously evaluates measures to reduce its energy consumption across all of its sites globally.
“These measures are an integral part of our sustainability strategy,” says the Michel Verstraeten, Global Smart Diaper Business Manager. “For example, we have integrated a digital monitoring system at our headquarters in Düsseldorf to precisely measure energy and water consumption which helps to further identify savings potential. In addition to process optimisations, we continuously upgrade our machines, air conditioning and lighting systems with regards to energy efficiency”.
Easyflow
Visitors to INDEX 23 will discover a number of Henkel solutions aimed at alleviating their current energy problems, such as Easyflow, a hot-melt adhesive in a new pressure sensitive form which enables safe and efficient delivery in production. It also breaks new ground in process performance and efficiency by offering melt-on-demand capabilities, closed system integration to eliminate foreign materials in hot-melt tanks, and auto-feeding to keep production moving. The Easyflow auto-feeding process not only minimises the melt history of the adhesive and the time allowed for any build-up of VOCs and odours, but also enables energy savings calculated at 23 per cent.
Henkel’s Technomelt DM Cool adhesives for diaper construction meanwhile operate at lower temperatures which optimises energy usage in the production line and reduces the environmental footprint. The application temperature is reduced by around 20°C compared to standard application temperature products.
Reduction
By 2030, Henkel aims to achieve a Scope One and Two climate-positive carbon footprint for its production sites.
“We are still pursuing our target of making a 65 per cent reduction in the carbon footprint of our production sites by 2025 compared to the base year 2010,” Michel Verstraeten says. “We are taking steps to cut energy consumption at all of our sites worldwide, including designing sustainable factories, improving our energy efficiency and switching to renewable energy. We are aiming to source 100% of the electricity we purchase for production from renewable sources by 2030 and planning to replace the fuels we need to generate thermal energy at our sites with CO2-free alternatives such as biogas or biomass. The sites will become climate-positive in terms of carbon balance when surplus CO2 -free energy that Henkel does not need for its own purposes is supplied to third parties.”