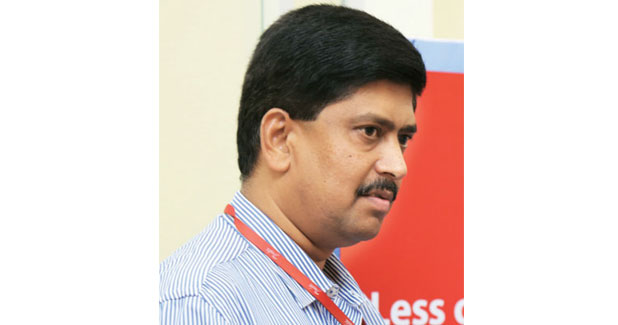
Variable frequency drives: Making Indian textile more sustainable
With the ´Make in India´ thrust gaining ground across industries, our focus today should be on the textile industry where India is touted to be second largest producer of textiles and garments in the world. The Indian textiles and apparel industry is expected to grow to a size of $223 billion by 2021, according to a report by Technopak Advisors.
Dr Paramasivam Shanmugam, Senior Manager, R&D-Power Electronics and Controls-IDC, Danfoss India
With the ´Make in India´ thrust gaining ground across industries, our focus today should be on the textile industry where India is touted to be second largest producer of textiles and garments in the world. The Indian textiles and apparel industry is expected to grow to a size of $223 billion by 2021, according to a report by Technopak Advisors. While we strive to make the maximum garments in India for various countries and our own consumption, there is a need to look at the sustainability aspect of this whole initiative. There is a dire need to be efficient while utilising energy resources for the textile machinery. Over the years, there has been growing concern about the environmental impacts of textile manufacturing process which include; energy consumption by the machinery, greenhouse gas (GHG) emissions, nutrients releases (leading to eutrophication) and ecotoxicity from washing (water heating and detergents) and dying of textiles. While it is impossible to negate energy consumption and pollution factor completely, steps can be taken at the manufacturing stage that reduce energy consumption and costs for the manufacturer. The elementary purpose of achieving energy efficiency is to get high energy savings and reduce costs. Increasingly, variable frequency drives (VFDs) are being utilized in many applications in this sector to reduce energy consumption. It is a product or subsystem extensively used to adjust the speed and torque characteristics of the motor to suit the applications needs. The energy consumption of 5 Kw motor at rated voltage in blower application is 43,800 units if it´s run by a direct supply (runs throughout the year). When one uses a VFD drive at 80 per cent speed, it 5 kW VFD plus suitable motor consumes about 25,404 units which is close to savings of 18,396 units. Therefore, the overall energy savings achieved is 42 per cent.
VFDs have tremendous potential to penetrate in various operations of the textile industry and as on today the missing part is lack of awareness about VFD and its benefits, especially among the decision makers in the industry. While the Installed capacity of industrial loads is 44.3 per cent wherein only 3-4 per cent motor loads are using VFDs and remaining motor loads runs directly form the supply.
Hence, the textile industry should wake up to the calling of energy efficiency sooner rather than later and help in reviving itself to Make in India for India and the world.