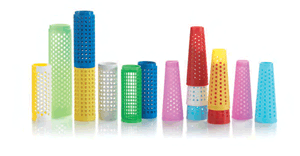
Debut of the new Thies yarn dyeing machine iCone
Yarns are made from different fibre types and weights for the different application purposes. Yarn can be wound by various methods, namely random winding, step precision winding and precision winding. The spindle speed, package format, structure and design, as well as the stroke can be adjusted individually.
Yarns are made from different fibre types and weights for the different application purposes. Yarn can be wound by various methods, namely random winding, step precision winding and precision winding. The spindle speed, package format, structure and design, as well as the stroke can be adjusted individually. Colleges and universities are searching for methods to simulate and to convert the density spread within the packages. At present, the winding density can be measured with the help of a mathematical formula:
The assumption is that bobbins with the same winding diametre have identical winding densities. Subject to the existing machines the package formats and designs are inherited in many cases. As a consequence, dyeing technologists are limited in choosing the optimal package format and design due to the surrounding conditions. Consumption of water and hence waste water, chemicals, dyes, electricity, and thermal energy are the main cost factors of dyeing processes. Due to the pre-set winding geometry and winding density, in general the potential for optimisation is limited. Therefore, Thies calculates the optimum diameters of the dyeing vessel and the optimum arrangement of the spindles in accordance to the pre-set number of packages per carrier. Then, the same liquor ratio can be ensured within a yarn dyeing factory, even with different batch sizes and different vessel sizes. Consequently, there is no need to adjust the parameter settings.
The concept of the flow reversal system, namely from inside to outside and from outside to inside, is proven and considered to be the best overall design. The new Thies iCone is based on an analysis of the liquor flow. As a result the redesign of the distribution system enables significant savings. The new flow reversal system enables the liquor flow to reach the yarn with minimal losses. Furthermore, it offers a quicker change in direction. An enlarged draining system and the energy-efficient functions allow rapid draining processes at a reduced level of bath entrainments. Consequently, the amount of water for rinsing can be reduced considerably. The liquor will be heated up with the help of a newly developed heating coil system, which it located below the material carrier.
All in all, these design optimisations lead to a significant reduction of the required space. With regards to the same level of dyeings per time unit, the production output is about 23% per square meter higher than in the established eco-bloc series. iCone offers ultra-short-liquor-ratio technology by providing the function DynamicDyeing. For example, at a winding density of 380g /l the liquor ratio is 1:3.6, while the liquor circulates from inside to outside. With regard to the same sample, the liquor ratio is 1:5.6 in a fully flooded vessel.
Considering the overall process, the pre-and after treatment processes (washing, bleaching and rinsing) can be identified as the most time consuming and the most resource allocating phases. An increased number of rinse bathes is used to achieve the required color fastness. Therefore, iCone is equipped with a new function, DynamicRinsing.