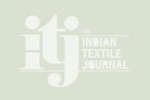
Cotton yarn: Quality depends on mixing strategy
A systematic mixing plan by maintaining the lowest possible variation in cotton quality parameters ensures trouble-free yarn production with consistent yarn quality, affirms Sunil Kumar Sharma.
A systematic mixing plan by maintaining the lowest possible variation in cotton quality parameters ensures trouble-free yarn production with consistent yarn quality, affirms Sunil Kumar Sharma.
In a spinning mill control over cotton quality is involved in the three steps stated below:
1. Approval of cotton bales: It is very important to purchase the right quality cotton bales according to defined quality standards. As cotton is a natural fibre and also a commercial commodity, its availability, prices and quality vary time to time based on supply and market demand, and therefore it is very important to select the required quality cotton bales at reasonable prices which should be viable for spinning industries. Approval of cotton bales should be very strict against its standards, otherwise this will result in stock of huge quantity of off-standard bales.
2. Grading of cotton bales: After reaching cotton bales in mill, these should be tested and properly graded according to mill standards. If possible it should be stacked in warehouse grade-wise.
3. Mixing planning: According to grade-wise, cotton bales stock and spinning count pattern, cotton bales must be selected for mixing plan with minimum possible variation.
Critical cotton properties
The following are the most common cotton properties, which are measured at the time of selection of cotton bales:
1. Length: Measured either in inches or in mm.
2. Fineness: Cotton fibre fineness usually measured in micronaire, ie, weight of fibres in microgram per inch.
3. Strength: Measured as fibre bundle breaking force in gms per tex.
4. Maturity: Measured either in term of maturity coefficient or in maturity ratio.
5. Uniformity: Measured either in % or as an index.
6. Short fibre content: Measured as %.
7. Trash content: Measured as %.
8. Moisture content: Measured as %.
9. Brightness: Represents as Rd value against degree of reflection.
10. Yellowness: Represents as value.
11. Colour grade: Colour grade is determined with conjunction of Rd & value.
All in one single value – SCI
Spinning Consistency Index (SCI) is a calculated value based on a regression equation. This equation takes into account all HVI properties and calculates one value to be used on each sample tested. The SCI is an index derived with data from a large number of cotton samples having a wide range in properties that is related to test data from yarn spun from each sample. By multiple regression analysis the contribution of each fibre property to yarn properties is revealed. Consequently, a single SCI value is influenced by inherent relationships of cotton micronaire, length, uniformity, strength, Rd and .
The following are SCI equation for the most important HVI measurements including colour:
For HVI Calibration Mode:
SCI = – 414.67 (2.9 x Strength) – (9.32 x Mic) (49.17 x Length in inch) (4.74 x Uniformity Index) (0.65 x Rd) (0.36 x )
If no colour module is installed then SCI equation is as follows:
SCI = – 322.98 (2.89 x Strength) – (9.02 x Mic) (43.53 x Length) (4.29 x Uniformity Index)
For ICC Calibration Mode:
SCI = – 414.67 (2.9 x Strength) – (9.32 x Mic) (49.17 x Length) (8.61 x Uniformity Ratio) (0.65 x Rd) (0.36 x )
If no colour module is installed then SCI equation is as follows:
SCI = – 322.98 (2.89 x Strength) – (9.02 x Mic) (43.53 x Length) (7.79 x Uniformity Index)
Effect of fibre properties
Each cotton characteristic imposes its own influence on spinning process and ultimately on<