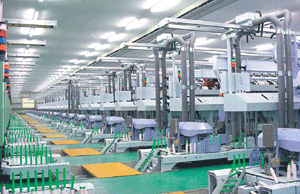
Package winding: A new wave of automation rolls in
With the Autoconer X5 and its new modular automation options, Schlafhorst offers spinning mills worldwide an optimal opportunity to ride this trend successfully.
With the Autoconer X5 and its new modular automation options, Schlafhorst offers spinning mills worldwide an optimal opportunity to ride this trend successfully.
Since 2012, Schlafhorst has been experiencing a sharp increase in demand for customised automation solutions in the package winding department. A new wave of automation is rolling through the global textile markets that will change the industry significantly in the next few years. With the Autoconer X5 and its new modular automation options, Schlafhorst offers spinning mills worldwide an optimal opportunity to ride this trend successfully.
Automation becoming more individual
There are basically three factors that trigger major automation initiatives in the industry: rising labour costs, a shortage of skilled staff and growing quality requirements. Rapidly rising investment in automation of the package winding department is currently marking a new trend. Until recently, the main markets of China, India, Pakistan, Bangladesh and Vietnam invested primarily in the Autoconer RM manual machine type. Since 2012 the proportion of automatic Autoconer X5, type D and V winding machines has been increasing steadily and perceptibly. Thanks to an intelligent material flow linked to the ring spinning machine, the type V machine in particular offers substantial savings in terms of staff. It also has an innovative quality assurance system in the SPID automated spinning position monitoring facility.
China and India above all are proving to be trendsetters. The degree of automation in these markets is growing dramatically. It is noticeable that the trend towards automation has become much more individual. For this reason Schlafhorst now offers its customers made-to-measure process automation solutions, which are optimally coordinated to the profile of requirements of each market and company, with the modular machine concept of the Autoconer. Gradual automation in differentiated stages is just as feasible as the complete integration of the material flow of the ring spinning machine and package winding department for maximum efficiency and quality. With this extensive range of solutions for spinning mills across the globe, Schlafhorst is the ideal partner in the current wave of automation.
Autoconer: The name says it all
Competence in creating innovative automation solutions is a tradition at Schlafhorst. The Autoconer 107 in 1962 was the first machine for automatic package winding to be ready to go into series production. Its automated sequences for eliminating yarn breaks and for bobbin changes were groundbreaking at the time. Time-consuming manual joining of the yarns and changing every single bobbin by hand were thus consigned to history. In the years following, the name Autoconer became synonymous with automation in the package winding department. Operation was simplified continuously, and more and more sequences were automated. An important impetus for automating the material flow and processes came during the 1980s from the then main markets of the textile industry in Europe and America, where rising labour costs led to a strong shift towards automation. With its caddy transport system for the Autoconer system 238, a feature that is unsurpassed even now, Schlafhorst created a milestone for the entire industry.
A holistic view of automation
The major strength of Schlafhorst was and is its ability to look at processes in the spinning and winding mill as a whole in order to be able to introduce functional innovations into the individual process stages. Automation was thus looked at from a wide variety of angles too. It is found in different sequences in the winding process, for example:
- in package handling
- in the winding process itself and its operation
- in bobbin t