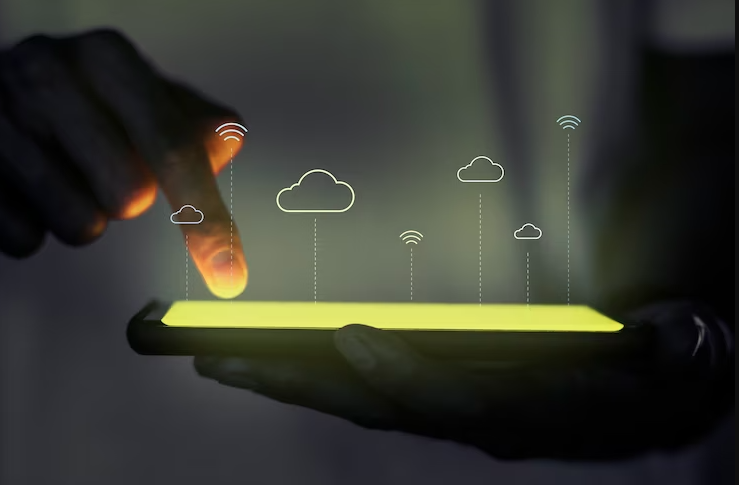
Emerging concepts in soft computing methods for the textile sector
Cloud computing looks promising in the textile and apparel industries considering its simplification of various business operations, but it needs more clarification with regard to the services it provides, says Dr N Gokarneshan and V Srimathi
Disclaimer: The first part of this article appeared in ITJ’s February issue.
The textile industry has come a long way – from the good old days of handcrafting to today’s highly technology-driven industry, the industry has transformed itself.
Internet of things
The textile industry has always been a very labour intensive industry and with advancements in technology, especially technologies such as IoT (Internet of Things), artificial intelligence, it has been able to achieve a high degree of automation over the complete textile fabrication process – right from design, fabric creation to finishing.
Being an industry which relies heavily on fine details such as equipment monitoring, stock management for dyes and raw material, supply chain visibility, workforce management and coordination, and analysis, textile is the most suited industry for digital transformation. The industry also needs to provide a quick response to deviations from Standard Operating Conditions to minimize the revenue loss and ensure effective use of skilled manpower. Very rightly so, it is at the forefront of the adoption of latest technologies.
Remember the last time our drone did a round of a manufacturing plant ? Now, fascinated by the digital transformation in the textile industry, it has decided to take a deeper look at one of the leading textile manufacturing plant which is IoT-enabled let’s see what it finds there and if it impresses the drone.
Spinning
The drone starts its review from the Spinning unit. For those who think that spinning is a simple process, let me share with you that it involves eleven (yes eleven) different intermediate processes such as – Bale Inventory Warehouse, Blow Room, Carding Department, Pre-Drawframe, Lap Winder, Comber, Drawframe, Roving Frame, Ring Spinning/Speed Frame/OE spinning, Winding, and TFO. Across all these processes, it is important to collect the data in real-time, monitor the production and quality, ensure appropriate scheduling, and have an interface with the ERP system. The drone sees that this unit uses automation to ensure real-time visibility of the manufacturing process. The IoT integration is helping this unit in highlighting the weak points in the production process and thereby reducing the machine stop time/down time. With reduced paperwork and automated data collection, the ‘decision support’ is optimal and the unit has optimised scheduling and logistics.
In the overall automation within the spinning unit, silver breaks and mending time analysis, specific energy analysis, linking of actual energy utilisation with production for good and reject quantity as well as per kg production, doff analysis, breakdown analysis, and OEE alongwith productivity/efficiency of workforce, are the things which the drone is specifically impressed with.
Weaving
Next, the drone hovers over the weaving unit. It learns that this unit monitors and synchronises all the manufacturing and logistics activities within the weaving mill – right from yarn purchasing and inventory up to the shipment of the finished fabric. It has various sub-units including Sectional Warping, Sizing, Weavers Beam Stock, Weaving Loom, loom shed of variety looms of different make, configurations, versions, customisations, and Cloth Bean Stock. The drone notices that through IoT-enabled automation, the unit is able to gather real-time data, do production monitoring, analytics, bench-marking and scheduling, manage yarn inventory management, and also do the ticket printing. Through optimised production schedule, real-time visibility of the manufacturing process, and automatic data collection, the unit has been able to increase its efficiency by as high as 10 per cent as compared to manual processes.
The drone is convinced that the overall efficiency enhancement is because of the unique features in the IoT solution such as weft and warp break analysis, OEE, water, air, electricity and energy consumption analysis, loom and style analytics, and breakdown analysis.
Processing
The drone understands that the next unit, which is the processing, is probably the most complex unit with processes such as Batching, Desizing, Dyeing, Sanforization, Singeing, Stenter, and Mercerization. But the automated system here is doing a perfect job of automatic monitoring (and analytics on the top of same) of the number of beams produced, recipe management, individual production vs target, machine monitoring, and stoppages, and overseeing the overall machine health. The plant-level daily MIS reports including production efficiency, actual production, conversion and invisible loss, specific energy consumption per kg of yarn (or fabric) and waste percentage are helping the stakeholders in optimizing the performance of the unit.
The highlight of the IoT solution is batch/equipment bench-marking, batch-wise energy, utility, and chemical consumption analytics, report of batch set parameters vs actual set parameters, and batch-wise stoppage analytics.
MES for Textiles
MES (Manufacturing Execution System) is the flexible tool that enables managers to achieve operational excellence and rapidly respond to changing conditions. Through IoT integration, the drone notices that the system is able to do real-time production and quality monitoring, production management and production scheduling on all machines even including air jet texturising machines. The yarn monitoring sensors ensure a 100 per cent quality assurance without having to do the time-consuming and inaccurate laboratory tests.
The drone is stunned to see the superior yarn quality without the need of any quality sampling.
One of the many things which impress our drone is the energy management at the unit. The IoT solution maps different energy consumption (such as electricity, gas, compressed air, water, steam etc.) for further analysis and optimization. The integration with the MES systems provides a perfect insight into energy consumption and production and has helped the unit in 3 per cent to 7 per cent energy savings through real-time energy consumption monitoring.
As identified by IDC, Smart Manufacturing (with digital factory, asset management, and integrated plant management), Connected Products (with IoT as a service, self-healing products, and product as a service) and Connected Supply Chains (with fleet management, connected transportation and track & trace) are the various layers of use cases of IoT in textile manufacturing.
As per our drone, considering the phenomenal benefits of IoT and automation in the textile industry, we will see more investments and attention to big data analysis, cloud, IT-OT integration, M2M and IoT in the coming future. These systems are set to help the textile mills in responding to changing customer demands with more accuracy and thereby boosting customer relationships and brand loyalty.
Mobile computing
The purpose of this review is to address the gap that exists in understanding fibres, yarns, fabrics, and apparel that form part of wearable technologies, specifically fabrics and garments as sensors. Interactions between the functionalised apparel and the human body in which transient conditions are experienced are highlighted. This is achieved by critically reviewing the published scientific literature on electrically conductive fabrics/fabric sensors. Given that wearable technology is one of the fastest-growing areas in clothing and textiles, a review focused on this fabric/garment-specific area is timely. While several reviews related to wearable technologies have been published since the beginning of the 21st century, their foci differed from the aim of the present review (e.g., a broad summary and overview; applications and/or end-use—for example, tennis, medical care, electrocardiographic monitoring, neurobiological rehabilitation, gait recognition, a smart textile suit, flexible lithium batteries, motion sensors, and human activity monitoring; properties of functionalising substances, including electrically-conductive polymers and carbon-based materials; processes for functionalising, such as e-broidery; and methods to determine performance properties. Each of these reviews is written from a perspective other than fabrics. Where fabric has been considered, the differences in structure and fibre composition have been highlighted; however, the effects on the performance properties of fabrics and apparel are often not determined.
This review is organised into sections on fabric structure, processes for applying functionalising substances to yield electrical conductivity, and properties essential for apparel. Being based on peer-reviewed published scientific papers and book chapters, the review represents up-to-date knowledge. The published literature reveals a need to focus on fabrics and methods to determine the performance of functionalised fabrics. The review excludes self-contained devices (e.g., sensors, actuators, and batteries) integrated in apparel/textiles; functionalised fibres and yarns not processed to fabrics; and issues related to data production, collection, transmission, and management. Fabrics, electrically-conductive substances, application processes, and designated end use identified in the research are described and referenced throughout the review.
Omitting specifics related to fabrics, experimental details, and results of studies limits our understanding of the research findings. Despite this, some comprehensive descriptions and studies have been carried out that exemplify detail needed. Diverse processes for functionalization can be used with varying success to impart electrical conductivity. Minimizing the changes to apparel properties (i.e., changes to thermal and moisture transfer, elasticity, flexural rigidity), ensuring durability, and managing the environmental effects of production are ongoing challenges. Standard test methods for determining fabric performance are rarely used and the acceptability of conventional fabric test methods is not clear given the addition of non-textile components. A multidisciplinary approach involving experts from the fields of chemistry, electronics, and textiles, and those involved in development of standard methods, is required to meet this challenge.
Robotics
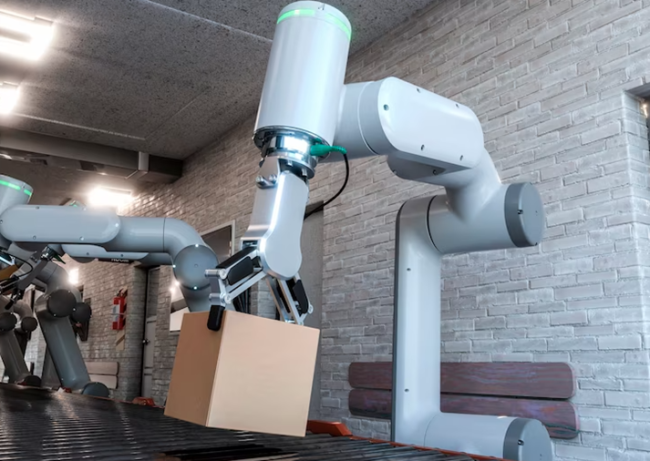
Application of Robotic automation in the textile industry provides so many benefits like labour savings, reduced cycle times, improved part quality, improved safety, increase productivity and efficiency. The application of such Robotic automation has resulted in significant benefits to the textile industry. High levels of consistency and precision in work pieces and high levels of repeatability and accuracy in manufacturing equipment have been required. Economic Justification can be shown only for large quantities of production. To achieve this, we need adaptive manipulation systems having some “Artificial Intelligence”. This article shows a wide range of automation in the textile process by using robots which ultimately increase the both basic requirements of the textile industry i.e. productivity and efficiency. Robots are being used in textiles today with substantial developments already being made and the future use of this new technology will develop as the economics of each area of manufacturing dictates. These are machine systems that can be conveniently directed to change their mode and sequence of operations by means of software instruction. Ideal examples are numerical controlled machine tools and industrial robot arms. These programmable systems still require high levels of consistency, precision, repeatability and more importantly, adaptability. More people in industry are becoming aware of the technology & aware of its potential for useful applications. The technology of robotics will improve over the years in such a way as to make robots more user friendly, easier to interface to other hardware & software and easier to install. Automation and robotics are two closely related technologies. In an industrial context, we can define automation as a technology that is concerned with the use of mechanical, electronic and computer based systems in the operation and control of production. Examples of this technology include transfer lines mechanics, assembly machines, feedback Control systems (applied to industrial processes), numerically controlled tools and robots. Accordingly, robotics is a form of industrial automation.
Areas of application include the following:
- Handling of bales in blow room
- Carding
- Splicing in autoconers and other winders
- Nonwovens
- Cleaning of textile industry
- Garment manufacturing
- Air bag manufacturing
- Fabric handling
- Simulator in fabric handling
- Welding in textile machines
- Folding and packing
The impacts of robotics are demand driven and quality driven.
Advantages are as follows:
- Robotics and automation can, in many situations, increase productivity, safety, efficiency, quality and consistency of products.
- Can work in very critical situations i.e. in hazardous environments without the need of life support.
- It needs no environmental comfort such as lighting, air conditioning etc.
- Much more accurate than human Work consistently, tirelessly Speed of operation is fast Robot will not ignore the work.
The disadvantages are as follows:
- Robots are more costlier
- Experts are required to maintain them
- Threat to employment in population crowded country like India
Robots are being used in textiles today and substantial developments are already being made. Since we operate in what may generally be described as a free enterprise economy, the future use of this new technology will develop as the economics of each area of manufacturing dictate. No doubt about it, all of us can look forward to exciting developments in this field. Current industrial robots are generally used for simple ·repetitive tasks of low added value, which substitute for unskilled factory workers. Such robots have value only if they are less expensive and used in mass production to achieve higher speed and yield. However, mass production is not the only form of operation in manufacturing industries. There are various types of manufacturing crafts that only experienced artisans can perform. Such crafts are usually of small quantity but can create high value added products. A new market for robot technologies might develop if robotics researchers were attracted to such areas, utilising the potentials of accumulated techniques, e.g. sensory feedback control, to achieve valuable application tasks for which even expensive intelligent robots can be worthwhile.
Automation
The textile industry, which has been around for centuries, has made many strides thanks to the advent of automation. The term automation is defined as the use of equipment and machinery to help make production easier and more efficient. Textiles such as cloth, yarn, cotton, and other fabrics have been made easier to produce thanks to automation. Let’s take a look at the advantages, disadvantages, and transformation automation has had in the textile industry. The advantages of automation as listed below:
- Fewer work hours for the same production
- Safer working conditions
- Higher quality product
Automation made it possible for the same tasks to be performed but with fewer hours of labour for employees. For example, inventions such as Eli Whitney’s cotton gin made it possible to separate the seeds from cotton without using manual labour. Similar inventions of automation were created with the purpose of making textile-related jobs easier to perform and with less human labour.
Automation in the textile industry has provided safer working conditions for employees. The textile industry is known for transforming various cloths and fibres into fabrics. This process often includes dyeing and spinning which are textile processes that can be relatively dangerous to an individual. Automation has created equipment to handle the bulk of these processes, making working conditions safer for all in the textile industry.
As with any industry, high quality products stand above all. The same goes for the textile industry, and automation makes this possible. When humans are tasked with a duty, there is always room for error for various reasons: they don’t feel well, personal company vendettas, etc. Although there are times when mistakes may occur with the equipment, there is still a much lower probability for error than when humans perform the same job.
For example, if an employee were to separate the seeds from cotton manually, there may always be the possibility that the person may become fatigued or perhaps simply not vested in completing the job properly. This means that it may not be done to the best of their ability.
The disadvantage is the high investment involved.
Big data analytics
Modern manufacturing facilities are data-rich environments that support the transmission, sharing and analysis of information across ubiquitous networks to produce manufacturing intelligence. The potential benefits of manufacturing intelligence include improvements in operational efficiency, process innovation, and environmental impact, to name a few. However, similar to other industries and domains, the current information systems that support business and manufacturing intelligence are being tasked with the responsibility of storing increasingly large data sets (i.e. Big Data), as well as associate the real-time processing of this ‘Big Data’ using advanced analytics. The predicted exponential growth in data production will be a result of an increase in the number of instruments that record measurements from physical environments and processes, as well as an increase in the frequency at which these devices record and persists measurements. The technologies that transmit this raw data will include legacy automation and sensor networks, in addition to new and emerging paradigms, such as the Internet of Things (IoT) and Cyber Physical Systems (CPS) and Artificial Intelligence (AI). The low-level granular data captured by these technologies can be consumed by analytics and modelling applications to enable manufacturers to develop a better understanding of their activities and processes to derive insights that can improve existing operations. Big data, as the name suggests, is an enormous amount of data. It can be defined by the 4V’s – Volume, Velocity, Variety, and Veracity. This 4V’s are responsible for complete functioning and analysis of data to obtain required output. The ability to analyse this enormous amount of data is known as big data analytics. The analysis of big data makes valuable conclusions by converting the data into statistics, that otherwise could not be exposed using less data and old-style methods.
To deal with this, the industry has experienced a shift from mass production to mass customisation, which is simply customisation at mass production efficiency. There are many technologies that help the industry in creating new ways for satisfying the ever-growing and ever-changing needs of the customer. There are, however, many challenges when it comes to adapting the production process as complexity increases with the level of customisation. Another problem with mass customisation is that, the customer is unaware of her/his needs and mostly lack professional design knowledge. Due to this, most mass customised products are not as desired, and hence, the customer is rendered dissatisfied. Thus, the requirement of a personal style advisor arises; to help the customer in finding a garment that satisfies her/his needs. Since, everything is going on the web, so there are virtual style advisors available. Most of them are not affordable by every customer. For this, the recommendation systems were introduced. These systems offer the customer recommendations during the process of designing. They can be based on collaborative filtering, wherein the system recommends on the basis of the preferences of a group of users; content based filtering, wherein the system uses user profile to match an item. This requires ratings given to a product directly by the user.
Importance of big data
The importance of big data does not revolve around how much data a company has but how a company utilises the collected data. Every company uses data in its own way; the more efficiently a company uses its data, the more potential it has to grow. The company can take data from any source and analyse it to find answers which will enable:
Cost savings: Some tools of Big Data like Hadoop and Cloud-Based Analytics can bring cost advantages to business when large amounts of data are to be stored and these tools also help in identifying more efficient ways of doing business.
Time reductions: The high speed of tools like Hadoop and in-memory analytics can easily identify new sources of data which helps businesses analysing data immediately and make quick decisions based on the learnings.
New product development: By knowing the trends of customer needs and satisfaction through analytics you can create products according to the wants of customers.
Understand the market conditions: By analysing big data, you can get a better understanding of current market conditions. For example, by analysing customers’ purchasing behaviours, a company can find out the products that are sold the most and produce products according to this trend. By this, it can get ahead of its competitors.
Control online reputation: Big data tools can do sentiment analysis. Therefore, you can get feedback about who is saying what about your company. If you want to monitor and improve the online presence of your business, then, big data tools can help in all this.
Textile big data
All the data associated with a textile product is hence called as textile data. This data can have used for trend analysis, customer behaviour analysis, forecasting etc. Textile industry generates and creates various sources of data. All these data come in various forms like words, images etc. Since it is the era of fast textile, the data is rapidly growing and changing. Hence, this data can be termed as fabric big it portrays all the features of big data. Following is a broad classification of the textile data.
Material: This includes the fabric that is used to make a textile product. The fabric has various characteristics like yarn type, yarn count, yarn twist, weft & warp density, weave structure etc. To achieve different types of fabric, one or more of these are changed. This enormously changes the appearance and had of the fabric, which correlate to emotions, textile themes, colours etc.
Textile design: It is the knowledge about the elements & principles of design, which combined together, gives the design of a textile product. The design of a product is mostly influenced by human emotions, textile themes, occasion of wear etc.
Body data: The body data can be in the form 2D or 3D data. For 2D, it is collected using the conventional method of body measurement. For 3D, it is collected 3D body scanners. These data can provide information like body measurement & body type.
Colour: Colour preference is an important aspect that influences a gamut of human behaviour. Kobayashi’s colour image scale states that colour can have three attributes – warm or cool, soft or hard, clear or greyish, which associate with hue, chroma & value. These attributes can be linked with the emotion
Technical/ production design: The technical design allows the producer to understand that how the product will be made. This makes the design of a product production friendly. It includes knowledge of pattern making, sewing etc. To extract knowledge from these data, they have to be linked together. The next section describes the proposed system that will use this data.
Goal of big data tools
Big Data tools are used for the analysis of the huge and complex data. Many organisations have now taken big data not just a buzz-word but a new technique for improving business. Organisations have to analyse mixed structured, semi structured or unstructured data. This is done in search of useful business and market information and insights. Big data analytics helps organise this data for the organisations. Organisations have to analyse mixed structured, semi structured or unstructured data. This is dons in search of useful business and market information and insights. Big data analytics helps organise this data for the organisations. Big data analytics is the process of examining large data sets containing a variety of data types — i.e., big data to uncover hidden patterns, unknown correlations, market trends, customer preferences and other useful business information. The analytical findings can lead to more effective marketing, new revenue opportunities, better customer service, improved operational efficiency, competitive advantages over rival organisations and other business benefits.
The study introduces the term textile data and why it can be termed as big data. It also presents the classification of the data and briefly defines each one of them. In addition to this, a system is proposed that will use this data to provide the customer with a mass customisation service. This methodology and working of the proposed system is briefly described. The future work involves the collection of the textile data, creating knowledge bases, establishing a link between those knowledge bases and connection it to the search engine.
Besides textile industry people, technology vendors are playing significant role in transforming the digital textile industry. Leaving behind popular social media forums, firms like SAP offer high-speed analytical tools which allow you to turn good volume of data into real business value, in just a blink of an eye. Big Data Analytics of textile product suppliers can also be leveraged to have good understanding on trends and ideas, which are persisting among audience, and those which are on the verge of being forgotten. Using such insights, designers make necessary adjustments in their products, change their marketing strategies, and then launch their fine collections in the market. Thus, Big Data influences key decisions related to manufacturing textile products, and helps both the industry leaders and their targets to know each other, and jointly cooperate in taking the digital textile industry accelerative.
Conclusion
Considerable developments have taken place in the application of soft computing techniques in the textile, apparel and fashion sectors. Some emerging concepts have been elaborated. Cloud computing on the one hand looks promising in the textile and apparel industries considering its simplification of various business operations, but on the other hand it needs more clarification with regard to the services it provides. Augmented reality is a refinement of virtual reality and dates back to about seven decades. It has undergone revolutionary changes during the years. Outlining AR technology can help designers to put technical data of apparel and provide a mesh framework of the apparel which may help designers to make any further modification very easily. Automation offers many advantages such as reduction of labour, time, better work conditions and safety, but involves high installation cost. Robotics relates closely to automation and offers many advantages to textile industry. But its adoption is a matter that needs careful consideration. It has the problem of implementation in labour oriented countries in India.
About the author:
Dr N Gokarneshan and V Srimathi are from the Department of Fashion Design and Arts Hindustan Institute of Technology and Science, Chennai.