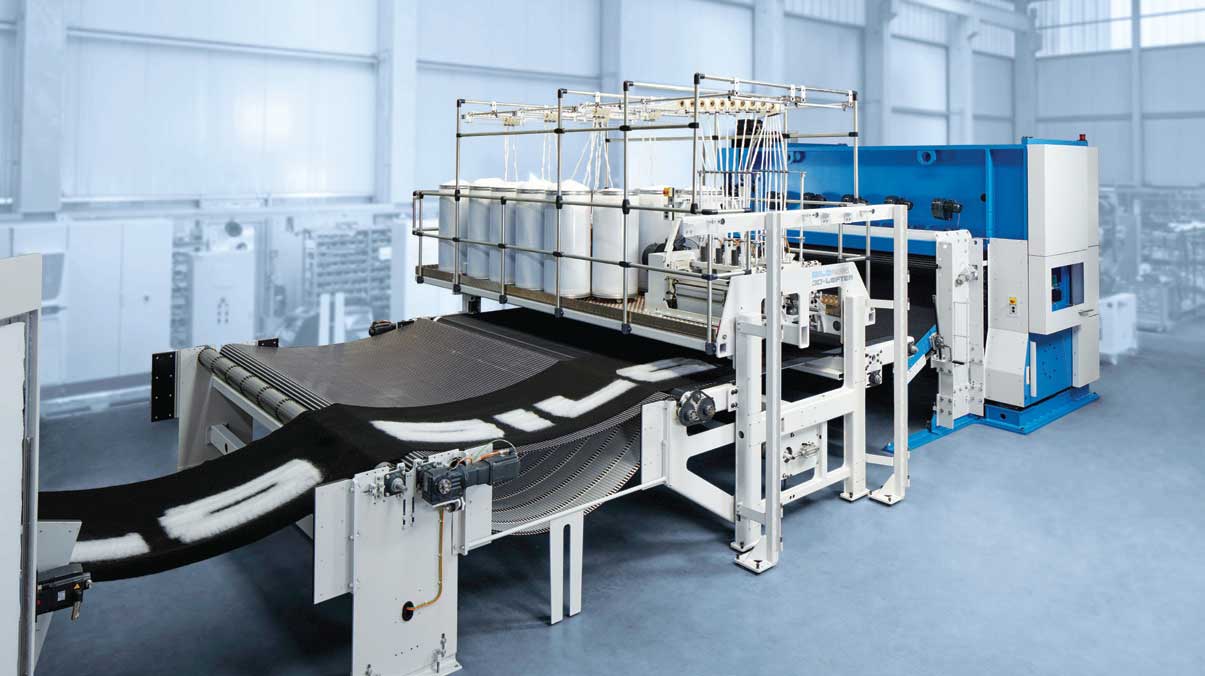
World of needling technology
In the course of the nonwoven industry’s history, Dilo has repeatedly succeeded in initiating steps by innovations and inventions and strongly contributing to competition in this sector.
Based on surveys of production, growth rate and market share of needlefelts, needling technology as the most important staple fibre web forming and consolidation technology has been raised in public awareness during recent years. The average of the past years has shown a continued production growth of more than 5 % p. a. Although other technologies may have enjoyed greater public interest, staple fibre web forming together with needling is still the leader in production volume. Only needled products, however, can claim universal usage properties and application fields.
Overall, it seems that needled staple fibre felts are in the fast lane compared to filament fibre felts. The basis for this high importance of needlefelts made from staple fibre is the processability of almost any fibre type: all natural fibres, all organic man-made fibres, all mineral and metallic fibres. Fibre fineness from below 1 dtex up to several hundred dtex is no problem. Staple lengths from below 20 mm to approx. 150 mm can be processed. The area weights of the needled semi-finished product can vary from approx. 30 g/m² to several kg/m².
The parameter range of raw material and machines allows a wide variety of combinations for product characteristics which range from light and fine needle felts used in medicine and hygiene applications to heavy technical felts. The great number of diverse needled products covers numerous applications: textile floor coverings, automotive interior linings, natural fibre felts for the mattress and bedding industry, wipes for household and industry, voluminous felts for heat and sound insulation, filter media for environmental protection, geotextiles for the construction industry, artificial leather for shoe and apparel production, high-tech felts for paper production and an almost endless range of further fine special applications. The worldwide market, which also includes shoddy processing, enjoys a stable and solid growth in numerous countries, with focus on the USA, European Union and China, ultimately on all continents.
DILO in a field of strong competitors is in the leading position of European machine building companies for the worldwide nonwoven industry This has been achieved by concentrating and specializing on the important sector “needling technology” where customers increasingly rely on complete solutions which include fibre preparation, cards, crosslappers and many different styles of needleloom. Working widths range from 0.6 – 16 m, needle densities are available up to several multiples of 10.000 needles/m/board and throughput speeds reach ca. 150 m/min. Technologies for structuring surfaces, in patterns or as velours, show a great variety of applications including interior material made of moulded composite parts for the automotive industry where needlefelts are in demand due to their weight saving characteristics.
In the course of the nonwoven industry’s history, Dilo has repeatedly succeeded in initiating steps by innovations and inventions and strongly contributing to competition in this sector. In the recent past, a new needle arrangement, the “8000X” design, has been created which can be considered as a breakthrough on the way to more even needlefelt surfaces with almost no stripes and undesired patterns. The “8000X” produces an even stitching distribution with less dependency on advance per stroke compared to classical random needle arrangements.
The latest research work at Dilo concentrates on a completely new sector for web forming and needling which may be best defined by the term “additive textile manufacturing”. The basis is an even needlefelt which gets a topologically varied fibre mass distribution in 3D by the controlled placing of fibres. This 3D web forming technology allows the placing of fibres directly where they are needed: as stock for subsequent moulding, to provide support for further strength and stiffness, sound insulation or as protection in case of accidents. The new “3D-Lofter” shows us the future of current needlefelts as a homogenous semi-finished product where textile lightweight constructions as in the automotive industry can meet further weight saving challenges.