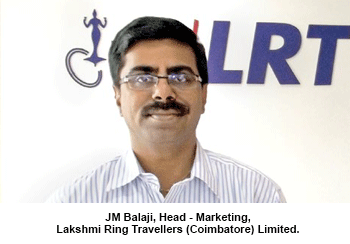
We hold 70% market share in travellers
Lakshmi Ring Travellers (Coimbatore) Limited (LRT), a group company of reputed Lakshmi Machine Works Limited (LMW), is situated in Coimbatore. Incorporated in 1974, LRT´s operation has been organised into independent business specific clusters.
Lakshmi Ring Travellers (Coimbatore) Limited (LRT), a group company of reputed Lakshmi Machine Works Limited (LMW), is situated in Coimbatore. Incorporated in 1974, LRT´s operation has been organised into independent business specific clusters. Each of this business unit has its own facilities for market coverage and service to customers. The difference business units: ring traveller division, engineering division, CNC profile cutting machine division, foundry division and surface coating division. LRT´s associated companies include Lakshmi Caipo and Lakshmi Energy and Environment Designs Limited (LEED). In an interaction with the Editor of the Indian Textile Journal, JM Balaji, Head-Marketing, Lakshmi Ring Travellers (Coimbatore) Limited, shares how LRT has been faring in the recent years and how has LRT responded to the technology shift.
Excerpts…
ITJ Editor: Ring travellers have moved from west to east, and in this scenario, how has Lakshmi Ring Travellers (LRT) been faring in the recent years?
JM Balaji (JB): Yes, you are absolutely right. In textile accessories business, textile machinery and accessories manufacturing is moving from Europe to places like India and China. Asia being a major market for textiles, it makes sense to do the production closer to the markets where it is used.
In Europe, the cost of production is increasing substantially. India has a definite advantage in terms of cost of manufacturing. As far as ring travellers are concerned, there is no technology difference between products manufactured outside India and in India. Testimony to this would be the fact that LRT is the largest ring traveller manufacturer in the world. We manufacture nearly three times more than our nearest competitor worldwide.
I think in future, for all textile accessories manufacturing, the production base is going to shift to Asia , especially India. India being the spinning capital of the world, India is surely a quality supplier of accessories for textile spinning industry to the global industry.
ITJ Editor: Has there been any technology shift in the production of ring travellers? How has LRT responded to it?
JB: In spinning industry, the demands of the customers are increasing day by day. People are looking at higher spindle speeds and want higher life Ring Travellers. Today they are talking in terms of breaks per 1000 spindles and not per 100 spindles. The main reason for this change is that labour cost is going up drastically and availability is also an issue. So people want lesser manpower in their units. Spinning Mills are looking for longer life of travellers, which would ultimately reduce labour. All manufacturers have to keep pace with the changing scenario.
In the last few years, LRT has developed a lot of new profiles and finishes. In fact, we have specific travellers for compact spinning. These travellers significantly reduce the start up breaks and also help the spinners to attain very high spindle speeds. For different compact technologies, we have different types of travellers. Similarly, for other requirements like slub yarn , core yarn , we have specific travellers. LRT is continuously improving its processes in-house. The same process, which we had 10 years back, will not be the same today. For e.g.: we had sapphire travellers, which we were manufacturing since 1988. Now also we call it the same, but the production methodology, raw materials and the processes has changed completely.
The life of the traveller and its ultimate performance has improved significantly from what it was earlier. In LRT, we do not rename our finishes unless there is a drastic improvement in performance. Earlier we used to talk about average traveller life of 4-5 days, but today it is about 10-15 days. In the last 5-6 years, our travellers´ life h