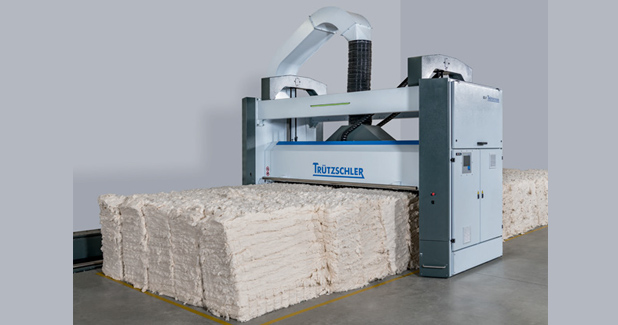
Truetzschler?s solutions for spinning preparation, nonwovens & MMF
Truetzschler Group presented intelligent machine technologies, digital solutions and installations for sustainable nonwovens.
?This allows us to measurably improve our customers? raw material utilisation and productivity while achieving consistently high quality,? says Dr Dirk Burger, CEO of Truetzschler. In addition, new cloud-based digital monitoring and management systems provide yarn manufacturers with transparency over all processes in the spinning mill. The My Wires app, for example, provides information on the status of clothings and service intervals and helps with the planning of reorders. Competent service for re-clothing can be provided immediately by Truetzschler Card Clothing (TCC). ?With the smart networking of machines as well as production and maintenance, we support customers in simplifying their entire spinning process,? explains Dr Christof Soest, CTO of the Truetzschler Group, and emphasises: ?This is why our digital platforms work not only for Truetzschler technology.?
The latest innovation in the blowroom offers more economy and quality as well: The Portal Bale Opener BO-P, with widths of 2,900 mm or 3,500 mm, allows significantly more bales to be placed side by side and processes them in parallel using two opening rolls. Thus, it results in significantly better blending and higher productions of up to 3,000 kg/h.
As a complete supplier for spinning preparation, Truetzschler is also breaking new ground in draw frames, the quality filters in the spinning mill. The autoleveller draw frame TD 10 automatically adjusts the perfect break draft for optimum sliver quality and realises significant cost savings due to its compact design and energy-efficient suction system. Like the TC 19i and the BO-P, the TD 10 provides the operator-friendly T-LED remote display, which visualises important machine and production information in a simple way.
Truetzschler Nonwovens presents sustainable concepts tailored to individual customer needs. The focus is on technologies for the production of biodegradable light-weight webs from renewable raw materials. In addition to proven solutions for carded, spun-laced nonwovens made of 100 per cent cotton or 100 per cent viscose, Truetzschler Nonwovens has developed an alternative technology in cooperation with Voith: In a wet-on-wet process, the web is formed from cellulose-based short fibres suspended in water and then bonded by means of hydro-entanglement. The sustainable, high-quality wipes and cleaning cloths that result from this process can be completely degraded by microorganisms in the environment after usage
by the consumer.
The Man-Made Fibers division presents the new four-end BCF machine MO40, which is based on the proven M40 concept. The symmetrical design in combination with the lamellaless HPc texturing results in maximum yarn and bobbin qualities. As each spinning position produces four BCF ends simultaneously, the machine achieves high productivity at moderate speeds, which ensures a stable process. ?Higher, faster, further is not always the solution?, emphasises Dr Lassad Nasri, CTO at Truetzschler Man-Made-Fibers, ?as with the entire Truetzschler Group, individual customer requirements always have priority for us. We support our customers with complete installation concepts, services and know-how – from the product idea to new business models.?
- As a proof of our commitment to these four principles, we presented our latest developments in rapier and airjet technology. When it comes to rapier technology, Picanol once again sets the benchmark in various aspects. We will deliver the proof, on a denim application, that a machine can be performant, versatile, sustainable, digital and user-friendly at the same time!
The brand new airjet machine, the OmniPlus-i, is however the première we reserved for ITMA 2019 Barcelona. OmniPlus-i is definitely the benchmark in airjet weaving. This further builds on the solid base of nearly 40 years of experience in airjet weaving, during which over 100,000 airjet machines have so far been shipped. OmniPlus-i is combining this extensive airjet expertise with a clear vision of the future! OmniPlus-i is featuring a redesigned reed motion, optimised relay nozzle set up and can be combined with SmartShed, the full electronic controlled shedding motion.
In total, Picanol had 12 machines on display at ITMA Barcelona: five airjet machines and five rapier machines at the Picanol booth. Furthermore, a rapier machine in Jacquard execution was on display at the Bonas booth and a terry airjet at the Stäubli booth. Below is the detailed overview of the machines and highlighted features: - OmniPlus-i-4-D-190 weaving a Car Seat fabric: A machine loaded with all the features that set the benchmark for our new principles. Smart Performance, Sustainability Inside, Driven by Data and Intuitive Control. OmniPlus-i, our new benchmark. Highlighted features include: new display and signal lamps, blue11 EasySet Prewinders, digital shedding motion (SmartShed), waste cord free RHS (CordLess) and PosiJet main nozzle.
- OmniPlus-i-4-R-190 weaving a parachute fabric: Weaving light filament fabrics without having to choose between speed and flexibility. Reaching the required high fabric quality standards becomes even easier with the increased inbuilt stability of the insertion system. Highlighted features include: New Display and signal lamps, Blue11 EasySet Prewinders, air consumption monitoring and management system (AirMaster), automatic relay Valve Drive (ARVD II Plus) and pick repair automation (PRA II Plus)
- OmniPlus-i-4-P-280 weaving sheeting: A clear example of a high end sheeting style. Thanks to the unique air tucking in maximum width flexibility is guaranteed. With the new OmniPlus-i the practical running speeds are lifted to an even higher level. Highlighted features include: New Display and signal lamps, Blue22 EasySet Prewinders, air consumption monitoring and management system (AirMaster) and air Tucking In device for continuous reed.
- OmniPlus-i-4-D-190 weaving Poplin: A proof that even light fabric segment can benefit from the OmniPlus-i platform. Digitisation, maximum flexibility and still running the highest speed. Highlighted features include: new display and signal lamps, Blue22 EasySet Prewinders, digital shedding motion (SmartShed) and air consumption monitoring and management system (AirMaster).
- OmniPlus-i-4-P-190 weaving bottom weight: The proven standard for weaving of bottom weight. Specified with the focus of reaching the highest possible production speed in this fabric segment. A clear demonstration of the potential of the new OmniPlus-i. Highlighted features include: new display and signal lamps, Blue22 EasySet Prewinders, air consumption monitoring and management system (AirMaster), and waste cord free RHS (Cordless)
- OptiMax-i-4-R-220 weaving denim: The digital loom! A machine driven by data, relying on smart performance, always with sustainability in mind. Highlighted features include: new display and signal lamps, guided GC gripper, electronic right Gripper opener (ERGO), quick Style Change (QSC), and waste reduction system LHS (EcoFil 4Colours).
- OptiMax-i-4-R-460 weaving a coating fabric: A new milestone in weaving coating fabrics, Free Flight gripper-system extended until 460 cm at highest insertion rates. No Guide-hooks required anymore on widths above T360! Highlighted features include: new display and signal lamps, pneumatically controlled backrest (DWC), Laserstop warp stop motion, and Electronic Righthand side Gripper Opener (ERGO).
- OptiMax-i-4-P-540 weaving Ground Backing: Our answer to weavers looking for versatile machines to weave a wide range of Technical Fabrics. Thanks to Guided Positive Grippers, Agro-textiles in a range from ground covers to open anti-hail nets become possible. Highlighted features include: new display and signal lamps, guided positive gripper GPG, waste reduction system LHS (EcoFil 4Colours), pneumatically controlled backrest (DWC), mechanical tucking in for tape filling, and waste ribbon winder.
- OptiMax-i-12-J-190 weaving upholstery: The ultimate versatility! No longer a dream, but reality thanks to our revolutionary positive gripper system. Smart performance throughout the complete insertion process. Highlighted features include: new display and signal lamps, Flexible Positive Gripper (FPG), electronic Filling Tension Control (EFT), and electronically controlled weft cutter SmartCut
- TerryMax-i-8-J-260 weaving Terry: The benchmark for terry weaving. No limitations in design, aiming at maximum performance in combination with ultimate quality. Highlighted features include: new display and signal lamps, versatile guided gripper (GCv), electronic Right Gripper Opener (ERGO), electronically controlled filling brake PosiFlex, directly driven pile control system, and electronically controlled pneumatic pile tensioner.
CATEGORIES Trade Fair
TAGS Air Consumption Monitoring And Management SystemAirjet MachineBlue11 EasySet PrewindersDigital Monitoring And Management SystemsDirk BurgerElectronic Filling Tension ControlElectronic Right Gripper OpenerFlexible Positive GripperIntelligent Machine Technologiessuction systemTruetzschler Card ClothingTruetzschler GroupWeaving Sheeting