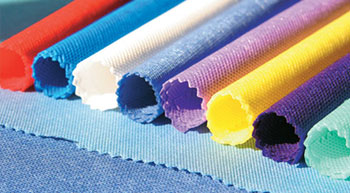
Traditional nonwoven materials are better tissue scaffolds
– By Seshadri Ramkumar, Texas Tech University, USA
Nonwoven substrates made using spunmelt and carding processes are cost effective to develop tissue scaffolds. A team of researchers from the University of Missouri-Columbia and University of North Carolina (UNC)/North Carolina State University (NCSU) have found that nonwoven substrates produced using the above traditional methods provided viable tissue scaffold medium compared to electrospun nanofibre webs.
Nonwoven substrates made using spunmelt and carding processes are cost effective to develop tissue scaffolds. A team of researchers from the University of Missouri-Columbia and University of North Carolina (UNC)/North Carolina State University (NCSU) have found that nonwoven substrates produced using the above traditional methods provided viable tissue scaffold medium compared to electrospun nanofibre webs.
Professor Elizabeth Loboa, who is currently the Dean of Engineering College at the University of Missouri undertook the study while associated with UNC/NCSU with Dr Stephen Tuin and Professor Behnam Pourdeyhimi of The Nonwovens Institute at NCSU.
Electrospinning field has exploded since the early 1990s due the efforts of Dr Jayesh Doshi, Founder of Chattanooga, TN-based eSpin Technologies and Professor Darrell Reneker of the University of Akron. Many industries around the world are working towards improving this method to make it scalable to produce cost effective nanowebs. Loboa and her team used carding and spunmelt technologies to develop polylactic acid scaffolds to grow human stem cells.
These scaffolds showed that stem cells grown on them were healthy after three weeks and could grow into fat and bone tissues. In addition to being effective media to grow stem cells, the cost of these media is relatively cheaper to electrospun nanowebs.
According to Loboa, small piece electrospun webs could cost between $2 to $5, whereas, the cost of traditional media ranges between $0.30 to $3. According to the team, the next step is to evaluate the performance of scaffolds developed using spunmelt and carding techniques in animals in vivo.
Santex Rimar Group has an history based on innovation as well as on tradition. The new name Santex Rimar Group joins together the Swiss tradition of Santex with the Italian foresight which comes directly from Rimar founded by Giannino Marzotto in the 60s as the R&D department of Marzotto Group, one of the world’s leading textiles manufacturers. Santex Rimar Group is based on continuous global growth and innovative product development in textile finishing, nonwovens and technical textiles.
The long experience in the nonwovens sector is today utilised to fulfill the ever-increasing demands for efficiency and productivity where our oven technology in thermo-bonding process still plays an important role for different and flexible applications like home textiles, hygienic, medical or industrial products. Santex Rimar Group can use a perfect synergy effect in combination with the Santashrink dryer for textile finishing under Santex brand.
The new Santatherm thermo bonding oven uses the so-called forced-through-air-mode, which is well established in Santashrink dryers. The air reaches a velocity of up to 40 m/s at the nozzle exit. The heat is transferred to the product surface in an even and effective manner. All kind of fibres can be processed independent from the webforming process. The airflow is adjusted perfectly depending on the actual product with a special flap and nozzle system. A user-friendly control system allows the selection of the airflow parameters, for example direction and kind of airflow. The most important quality feature of the new Santatherm is the uniform quality of the final product on both surfaces.
Efficient heat transfer and temperature stability result in a high productivity. Due to the modular design the machine is very compact enabling a fast installation and easy maintenance. As a result maintenance and service costs are very low.
The Santatherm thermo bonding oven can be combined with the Santabond smoothing and calibrating calendar. Together with the Cavitec coating and laminating systems Santex offers a wide range of solutions for nonwovens applications.
For further information:
Santex Rimar Group, Località Colombara 50 36070
Trissino (Vicenza) – Italy