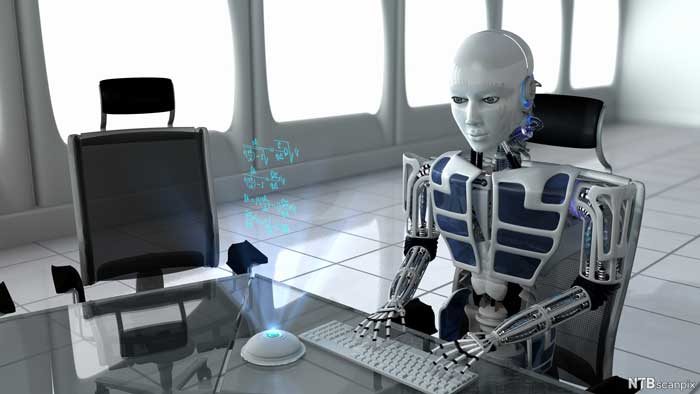
Top 5 robot trends for 2023
The next big thing in industrial automation is to use robots in the textile sector.
According to The International Federation of Robotics, the stock of operational robots around the globe hit a new record of about 3.5 million units – the value of installations reached an estimated $ 15.7 billion.
Along with other industries, even textile industry has been adopting automated practices in the recent years. The next big thing in industrial automation is to use robots in the textile sector.
The textile sector has experienced slower expansion than other sectors, which have scaled up quickly and adopted cutting-edge technologies for better and faster production.
The main reason for this slower pace is that, for the time being, sewing and materials call for a certain amount of human finesse. Here are just a few examples of how using robots to handle fabric and production could significantly improve the textile supply chain.
Automated sewing
Hand sewing requires a lot of time and repetition, which has been related to discomfort and musculoskeletal issues. According to one study, 88% of sewing machine operators experienced back discomfort in the previous year, and 82% also experienced lower back and knee pain that limited their ability to engage in some level of daily activities.
Large-scale sewing has been a challenge for machinery, in large part because robots have never been able to reproduce the accuracy and control of hand sewing on flexible fabrics. With more sophisticated mapping technology, artificial intelligence (AI), and the capacity to travel more complicated courses, modern robotics aim to change that.
Robots now have some amazing innovations that can close seams without human assistance by shifting the sewn design to a temporary solid form. This reduces the physical strain on workers while increasing production volume in a shorter amount of time, ultimately improving the manufacturer’s bottom line.
Layer selection
More than half of a warehouse’s operating costs are incurred while picking orders manually for processing or delivery, primarily because of labour expenditures. If hand picking required unique finesse or trained ability, the reality of those expenses might not be as difficult to accept, but manual picking is notoriously tiresome, especially in high-volume production.
Letting robots handle fabrics has never been a practise that the textile industry has taken lightly. Even modest mishandling can be expensive because machinery has never had the sophistication to grasp the various physical care requirements of different types of fabric.
Robotextile robots is revolutionising the textile industry. The technology employs a specifically created textile gripper to precisely handle and pick each layer of fabric.
Many manufacturers may increase their output more effectively and fulfil the increased need for high-volume production by implementing robots systems similar to these.
Quality control
When producing textiles in big quantities, consistency in quality is essential. Manual quality inspections require a lot of time and are far from accurate since no one can test a fabric against every potential stressor and the human eye can only see so much variation in colour pigmentation.
Simply put, using robots to produce textiles makes more sense. By monitoring all aspects of the production process, such as precise measurements of the pigment, water pressure and flow levels, and fabric temperature, AI algorithms can encourage greater uniformity. Robotic devices are capable of analysing fabrics right down to the fibre level and identifying any colour or quality irregularities.
The end result is far more accuracy and significantly less product waste, which ultimately saves manufacturers money and frees up staff to perform more complex jobs.
Manage growing demands
The market for textiles is expected to rise from $654.57 billion in 2021 to slightly over $861 billion during the following five years due to rising global demand.
Robots in the textile industry might mean satisfying this demand, preventing interruption or lost revenue, and possibly going above and beyond it.
As per the report by The International Federation of Robotics, here are the top 5 trends shaping robotics and automation in 2023:
Energy Savings
Energy efficiency is a crucial to increase companies’ competitiveness amid growing energy costs. The deployment of robotics helps in various ways to minimise energy usage in production. Compared to traditional assembly lines, considerable energy savings can be gained through reduced heating. At the same time, robots work at fast speed thereby raising output rates so that manufacturing becomes more time- and energy-efficient.
Robots of today are made to use less energy, which results in lower operational expenses. Companies use industrial robots outfitted with energy-saving technology to meet their production sustainability goals. For instance, robot controls can convert kinetic energy into electricity and feed it back into the power grid. The amount of energy needed to run a robot is significantly reduced by this technology. The smart power saving mode, which regulates the robot’s energy supply as needed throughout the workday, is another feature. Such networked power sensors are expected to become an industry standard for robotic systems because industrial facilities still need to monitor their energy usage.
Reshoring
Reshoring in a variety of industries is increasingly driven by resilience: Car manufacturers e.g. invest heavily in short supply lines to bring processes closer to their customers. To support their electric vehicle projects, these businesses use robot automation to produce strong batteries in huge quantities at a low cost. These expenditures make the shipment of hefty batteries superfluous. This is significant as more and more transportation businesses refuse to ship batteries for safety reasons.
Relocating microchip production back to the US and Europe is another reshoring trend. Since most industrial items presently require a semiconductor chip to work, their supply close to the client is vital. Due to their ability to meet the high standards of precision, robots are essential in the chip manufacturing process. Robots created specifically for these tasks automate the fabrication of silicon wafers, perform cleaning and sanitising duties, or test integrated circuits. Recent examples of reshoring are Intel´s new chip factories in Ohio or the recently announced chip plant in the Saarland region of Germany run by chipmaker Wolfspeed and automotive supplier ZF.
Easier to use
Programming for robots has gotten simpler and more approachable for non-experts. Companies are supported by suppliers of software-driven automation platforms that enable customers to control industrial robots without any prior programming knowledge. Original equipment producers collaborate closely with low-code or even no-code technology partners to enable programming of robots by users of various skill levels.
An intuitive user interface and simple software replace complex robotics programming, creating new possibilities for robotics automation: With tailored solutions for the demands of small and medium-sized businesses, software start-ups are expanding into this industry. For instance, a conventional heavy-duty industrial robot can be given new software and sensors to enable collaborative setup operation. Workers may easily adapt large machinery to various tasks because to this. Companies will thus get the best of both worlds: robust and precise industrial robot hardware and state-of-the-art cobot software.
The burgeoning new market for low-cost robotics is also driven by user-friendly programming interfaces that let customers set up the robots themselves. In response to the epidemic in 2020, a lot of new clients began experimenting with robotic solutions. Robot suppliers acknowledged this demand: Low-cost robot deployment is supported by simple setup and installation, such as with pre-configured software to handle grippers, sensors, or controllers. These robots are frequently available for purchase online, and programme routines for a variety of applications can be downloaded from an app store.
Artificial Intelligence
Propelled by advances in digital technologies, robot suppliers and system integrators offer new applications and improve existing ones regarding speed and quality. Connected robots are transforming manufacturing. Robots will increasingly operate as part of a connected digital ecosystem: Cloud Computing, Big Data Analytics or 5G mobile networks provide the technological base for optimised performance. The 5G standard will enable fully digitalized production, making cables on the shopfloor obsolete.
Robotics has a lot of potential for AI, which could enable a variety of advantages in manufacturing. Better managing variability and unpredictability in the external environment, whether in real-time or off-line, is the primary goal of using AI in robotics. In software offers where operating systems profit, such as with streamlined processes, predictive maintenance, or vision-based gripping, AI enabling machine learning plays a growing role.
Robotics has a lot of potential for AI, which could enable a variety of advantages in manufacturing. Better managing variability and unpredictability in the external environment, whether in real-time or off-line, is the primary goal of using AI in robotics. In software offers where operating systems profit, such as with streamlined processes, predictive maintenance, or vision-based gripping, AI enabling machine learning plays a growing role.
Industrial robots can have second life
Since an industrial robot has a service lifetime of up to thirty years, new tech equipment is a perfect opportunity to give outdated robots a “second life”. Manufacturers of industrial robots like ABB, Fanuc, KUKA, Stäubli, or Yaskawa have specialised repair facilities adjacent to their clients to efficiently refurbish or improve used units. For both robot makers and their clients, this “ready to repair” approach reduces costs and resources. Offering clients long-term repair is a significant contribution to the circular economy.
Article courtesy: The International Federation of Robotics (IFR)