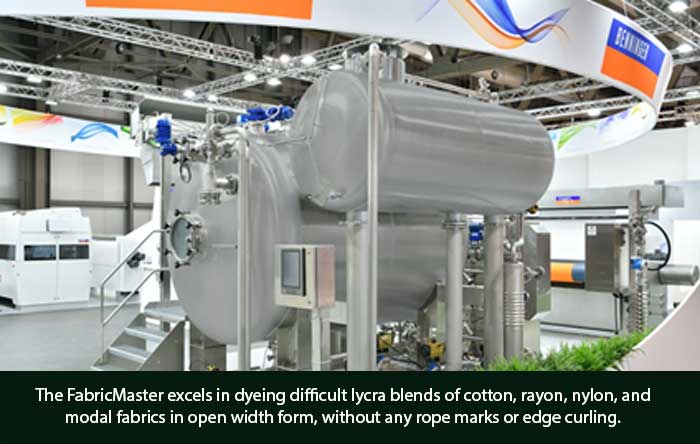
The sustainable way of discontinuous dyeing
Benninger’s FabricMaster revolutionises textile dyeing in India.
The Swiss company Benninger, renowned for its innovative textile machinery, has introduced its latest marvel, the FabricMaster, to the Indian market. This soft flow machine is already making waves globally, with installations in Europe, the USA, Peru, Central America and Bangladesh. Now, it is set to transform the Indian textile industry, with production taking place at Benninger’s High Tech Fabrication facility in Pune.
The first FabricMaster in India has been operational for a year at Amarnath Dyeing And Bleaching Works. The machine’s outstanding performance has led Amarnath to order a second unit, underscoring their complete satisfaction with its capabilities. This second machine is now ready to leave the Benninger Works in Pune, marking another milestone in the FabricMaster’s journey.
“This innovative technology transforms our production capabilities, setting new benchmarks in the industry. Our new machines will help us reach our goal of becoming the leader in quality fabric processing while caring about ecology. The machines will help us do so by enhancing our efficiency, reducing waste, and minimising our environmental impact. This investment not only underscores our commitment to excellence but also to sustainable practices that benefit both our customers and the planet”, says Sudarshan Chandak, Director at Amarnath Dyeing And Bleaching Works.
Excellent dyeing performance
The FabricMaster is designed to handle the most challenging dyeing tasks with ease. It excels in dyeing difficult lycra blends of cotton, rayon, nylon, and modal fabrics in open width form, without any rope marks or edge curling.
The FabricMaster ensures optimal dye penetration and color consistency achieving uniform fabric handling during the dyeing process. This is ensured thanks to the FabricMaster’s nozzle which can be precisely adjusted based on the weight of the fabric being dyed. Lightweight fabrics benefit from low liquor volume, while heavier fabrics are treated with increased flow. Furthermore, the internal fabric plaiter operates at varying speeds, accommodating different fabric types. Moreover, its automated add tank ensures accurate chemical addition simplifying chemical dosing and mixing.
Key factors are minimal consumption of water, steam, chemicals and dyestuff, to ensure right-first-time results with lowest waste. The FabricMaster boasts an optimised chamber design, resulting in the lowest liquor ratio among water-driven piece dyeing machines. The carbon footprint of the FabricMaster is designed to be the future industry benchmark for sustainability.
Why FabricMaster also stands out
The FabricMaster’s self-cleaning lint filter keeps the system running smoothly to enhance productivity. It monitors lint accumulation and automatically cleans itself, minimising downtime and maintenance hassles. Furthermore, the FabricMaster’s high-capacity heat exchanger accelerates heating gradients, reducing cycle times.
After dyeing, unloading the fabric swiftly is crucial. The FabricMaster features a frequency-controlled unloading winch, ensuring efficient fabric removal without compromising quality. The fabric lift from the chamber to the reel is less than half that of competitors’ machines, improving fabric transport.
The FabricMaster is a testament to Benninger’s commitment to innovation and quality. As it continues to gain traction in the Indian market, it promises to revolutionise fabric dyeing processes, setting new standards for efficiency, quality and precision to textile dyeing processes.