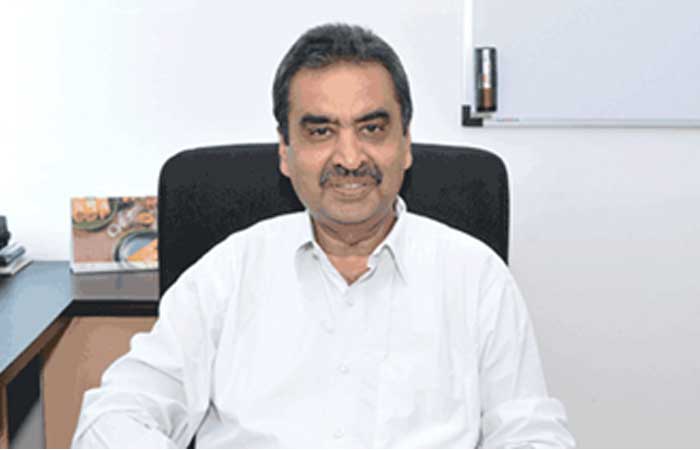
The future trends for automation in textile industry is very promising
Saurer is a globally operating technology company focusing on innovations for the processing of fibre and yarn, including machinery, components and software. The company partner with customers and provide smart fit-for-purpose solutions to help their clients achieve their business aspirations. Ashok Juneja, the Director of Sales & Service, Saurer Textile Solutions, in this interview with Divya Shetty, sheds light on the advantages of integrating automated techniques into the manufacturing unit, and elucidates how his company is leveraging this technology.
Given the current uncertainty of the Indian textile industry and global industry in general, how can automation help mitigate this challenge?
Presently, the Indian textile spinning industry is facing uncertainty due to fluctuating raw material costs, evolving market demand, and global competition.
Automation can address some of these challenges by streamlining production processes, reducing labor dependency, and improving product quality consistency. Automation also supports continuous production with being less dependent on labor force and reducing downtime clubbed with minimising the clubbed human errors. Automated machines can increase efficiency and precision in yarn production, leading to lower production cost and better product quality. Automation in our textile industry can mitigate uncertainty by streamlining production processes and increasing efficiency to a good extent. Advanced machines can be optimised better for resource utilisation and making more consistent quality. Also, automation enables flexibility in adapting to changing market demands swiftly, allowing manufacturers to stay competitive.
Additionally, automation enables real-time data monitoring and analytics can help forecast demand and optimise inventory management. Automation can enhance sustainability efforts by reducing waste and energy consumption.
By integrated automation technologies, the Indian textile spinning industry can enhance its competitiveness in the global market and mitigate the challenges associated with mentioned uncertainties effectively.
How does automation help in increasing productivity and reducing the losses? How is your company benefiting from the automation?
Automation undoubtedly increases productivity by streamlining workflows, reducing errors to a great extent. By minimising manual operations, it enhances operational efficiency. Automation optimises resource utilisation, reducing losses due to inefficiencies.
Automation can perform tasks with higher precision and consistency compared to manual labor, leading to increased efficiency in production. Automated systems can operate continuously without the need for breaks, reducing downtime and maximising production output. Automation often incorporates energy-saving features, leading to reduced energy consumption and lower operating costs. Automation systems generate vast amounts of data, which can be analysed to identify areas for further optimisation, such as process improvements or predictive maintenance. Above all, automation solutions are merely dependent on manual flaws, thus enables to achieve foreseen results with minimum rejections or corrections etc.
We as a manufacturer offer high-quality, techno-logically advanced and customer-specific automated solutions for staple fiber processing from Bale to yarn. For us, automation provides assurance to our consistency in Quality and to meet the timelines of delivery. Thus, enables us to maintain our commitments to customers. This strengthens our competitive position in the market.
What challenges exist in integrating automation into textile manufacturing?
While automation offers numerous benefits to textile market, several challenges exist in integrating automation such as High initial investment – The upfront cost of implementing automation, including purchasing machinery, integrated software system, and training personnel, can be substantial. This initial investment may pose a barrier for SMEs with limited capital resources. Workforce Transition– Automation often necessitates a shift in workforce skills and roles. Employees require training to operate and maintain automated systems, while some traditional roles may become obsolete. Additionally, hiring experts and the retention of such a work force to operate automated machines is an additional challenge. Resistance to change – Resistance to change from employees and management can hinder the successful integration of automation. Addressing concerns about job security, providing adequate training and support is an added responsibility.
Additionally, the initial capital investment required for automation systems can trouble small and medium-sized manufacturers (MSMEs) with limited expenditure capacities. Rising plant maintenance costs is also a present challenge since automated systems require regular upkeep with technical support.
Addressing these challenges requires strategic planning, investment in training programs, and adopting flexible automation solutions tailored to the specific needs and constraints of the textile industry. Fostering the culture of innovation and adaptation is essential for overcoming resistance to automation. It is a continuous process and needs related adaptations from time to time.
How is Industry 4.0 (like AI, IoT networks, robotics, etc.) changing the landscape of textile manufacturing?
Industry 4.0, also known as the Fourth Industrial Revolution, is fundamentally changing the landscape of textile manufacturing by introducing advanced technologies and digitalisation across the entire production process. Industry 4.0 enables the development of smart factories where interconnected machines, sensors and device communications collaborate with each other in real time.
Industry 4.0 technologies such as AI, IOT networks and robotics are revolutionising textile manufacturing by enhancing efficiency, flexibility and quality. AI-driven predictive analytics optimise production processes, OTT networks enable real-time monitoring with control. Robotics automate repetitive tasks, reducing labor costs and improving precision. These advancements help in data-driven decision making, enabling the textile manufacturers to adapt to the changing market demands swiftly while making competitiveness.
Textile manufacturers can leverage data analytics and AI to optimise production efficiency, predict equipment failures, improve product quality, and identify opportunities for process optimisation. Automation and robotics play a central role in Industry 4.0 by automating repetitive and labor-intensive tasks in textile manufacturing with minimised flaws. Digitalisation creates virtual replica of physical manufacturing systems and process, allowing textile manufacturers to simulate, monitor and optimise production in real-time. Overall, Industry 4.0 is revolutionising the textile manufacturing industry by driving digital transformation, increasing automation, enhancing efficiency and productivity, improving product quality, and enabling greater flexibility and customisation to meet the demand of today’s rapidly evolving market.
Industry 4.0 technologies streamline operations, reduce labour and minimise errors, resulting in increased efficiency and overall productivity. AI-helps predictive maintenance anticipates equipment failures, reducing downtime and saving on maintenance costs. By analysing sensor data, AI predicts the material requirement for maintenance, preventive cost.
IoT implementation into textile manufacturing process is somehow becoming a standard nowadays due to fast adaptation of requisite customer demands, also in case of certain customised solutions etc.
What are the future trends in automation in the textile industry?
The future trends in automation in the textile spinning industry are poised to revolutionise production processes, enhance efficiency, and meet the evolving demand of the market. Such key trends are as: Advance Robotics, IoT Integration, Digital Twins, AI and machine learning, Automated quality control, Energy efficient technologies, Integration with supply chain technologies such as RFID tagging & ERP systems. The future of automation in the textile spinning industry will be characterised by increased connectivity, intelligence, and adaptability, driving innovation, efficiency, and competitiveness in the global market.
Future Trends of automation into Textile Industry will play a very vital role in Advanced apparel manufacturing with energy-efficient and high-speed processes supported by Computer aided programming processes. Future trends in automation in the textile industry include the further integration of AI and machine learning algorithms for predictive maintenance and quality control. Collaborative robots will become more prevalent, working alongside human operators to enhance productivity and safety. Advanced sensing technologies will enable more precise material handling. Moreover, there will be a continued focus on sustainability, with automation playing a key role in reducing energy consumption, waste, and environmental impact throughout the textile manufacturing process.
In a nutshell, the future trends for automation in textile industry are very promising with substantial growth into various applications right from understanding the market needs and delivery the adequate requirement within least timespan. It can be foreseen gradually becoming as a standard with increased integration into various segments of textile industry.