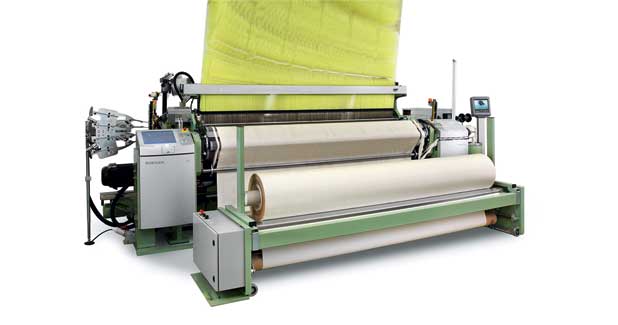
DORNIER solutions inspired by ’The Green Machine†concept
When the conversation turns to sustainability, many are of the opinion that business should lead from the front; machine builder DORNIER has applied this guiding principle rigorously for more than 65 years.
When the conversation turns to sustainability, many are of the opinion that business should lead from the front; machine builder DORNIER has applied this guiding principle rigorously for more than 65 years. At the upcoming Techtextil exhibition, the family-owned company will present comprehensive solutions in sustainable technologies for the manufacture of clothing, home textiles and technical fabrics.
“Our machines are not just green on the outsideâ€, declares Wolfgang Schöffl, head of the Weaving Machines product line at DORNIER. He is referring to the trademark green color of the machines from Lake Constance, which also serves as the visual equivalent of the company’s philosophy of sustainability, “The Green Machineâ€. In this way, DORNIER pursues a total approach which is applied systematically to all technological aspects from the machine to the woven fabric up to and including the finished product.†With regard to filtration, for example: The “Green Machines†are used to make ultrafine precision fabrics which are implemented in the service of environmental protection all over the world in filters for cleaning or preserving the cleanliness of air, water and exhaust gases. “We are constantly refining our equipment so that our customers can manufacture still more closely woven fabricsâ€, says Schöffl. Consequently, the last few years have seen a steady improvement in filter quality: With the latest generation of P2 machines, a reed impact force of up to 50 kN and particularly the shed geometry optimised for technical fabrics are combined to produce wide air and water filter fabrics of very high density.
Conserving fuel with ease
The machines from DORNIER also weave with fuel economy in mind: For example, between 1990 and 2017 German airlines reduced the amount of fuel consumed for carrying passengers 100 km by almost half. This impressive achievement is due in large part to the material favored by all engineers who wish to make their machines lightweight yet durable: carbon-fibre reinforced plastic (CFRP). Airbus and Boeing both began testing installing the first CFRP components in the early 1970s.
These days, CFRP accounts for over half of the construction of the modern aircraft types such as the A350 XWB and the Dreamliner. But what hardly anyone outside the close community of the initiated knows: Weaving machines by DORNIER have represented the standard for working high-performance fibers such as carbon, glass and aramid for more than 50 years. And as environmental requirements become inexorably more stringent and every last gram is scrutinised intensely, these days even lightweight, ultra-strong primary structures such as turbine blades are produced on modern 3D Weaving Machines from DORNIER. Apart from aviation and space travel, the use of fibre composite plastics is also becoming more widespread in the construction industry (based primarily on the idea of replacing steel with carbon) and automobile construction. Incidentally, on the subject of cars: Two out of three airbags and three-quarters of all motor vehicle tires with textile reinforcement are made on weaving machines from DORNIER.
CATEGORIES Industry Update