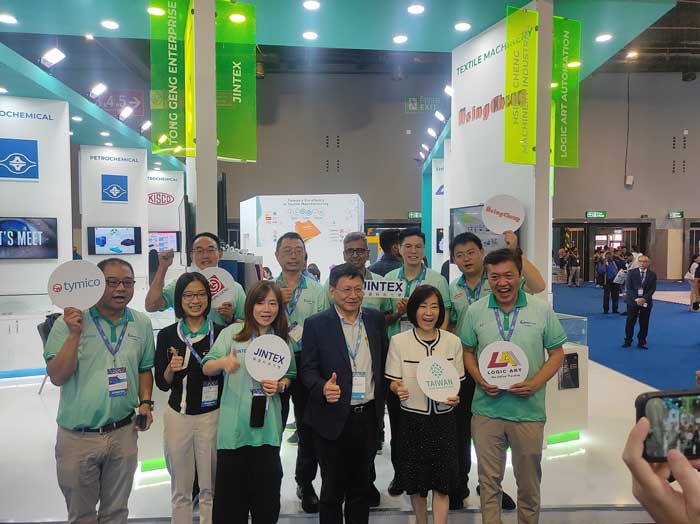
Taiwan offers smart dyeing solutions to Indian textile firms
The highlight of the Taiwan Expo 2024, held in New Delhi, was smart, one-stop solutions offered by a group of Taiwanese firms for all dyeing requirements of textile companies, says Rakesh Rao.
Taiwan Expo 2024 India, hosted by the Taiwan External Trade Development Council (TAITRA) in New Delhi from July 8-10, showcased the latest advancements in the textile and shoe-making industries at the Taiwan Smart Manufacturing Pavilion. The event underscored the expanding trade and technological collaboration between India and Taiwan. Taiwan is globally recognised for its comprehensive range of machinery and accessories for various manufacturing sectors. The country offers premium textile products ranging from specialty chemicals to automated and eco-friendly machinery, accessories, and high-functional fabrics.
The highlight of the show was smart, one-stop solutions offered by a group of Taiwanese firms, under the Taiwan Textile A-Team, for all dyeing requirements of textile companies. The A-Team offered a unique platform to explore the latest dyeing process advancements and discover opportunities to elevate dyeing house’s capabilities. At the Taiwan Smart Manufacturing Pavilion, the spotlight was on six major Taiwanese companies specialising in textile dyeing processes.
JINTEX offers biodegradable solutions for dyeing
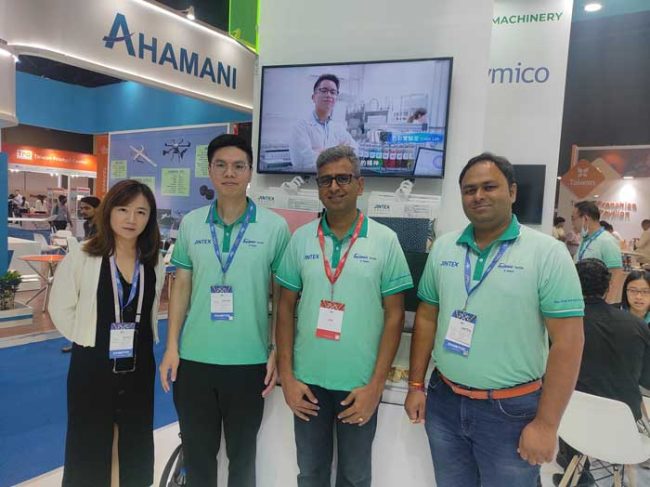
Paul Chen (2nd from left) and Ganesh HR (3rd from left) with JINTEX team
JINTEX Corporation, the leading manufacturer of textile and leather specialty chemicals, has made dedicated efforts in the field of green chemicals for many years. It has branches in Taiwan, Vietnam, India, Indonesia, and China. Each of these five branches includes its own manufacturing factory. Their main products are chemical agents used in the dyeing and pre-treatment processes, as well as functional agents for finishing processes. In India, their manufacturing units are located in Chennai and Bengaluru. Additionally, JINTEX India provides a specialised chemical agent for leather treatment.
“Our primary focus in India is on synthetic agents due to the rising demand seen in Taiwan and Vietnam. In South India, the market for cotton and synthetic fibres is roughly balanced at 50-50. We are seeing increased use of blends such as polyester-cotton and polyester-spandex. I believe the demand for synthetic agents in textiles will continue to grow and potentially double in India,” stated Paul Chen, from the Business Development Department of JINTEX Corporation Ltd.
“We are also prioritising the development of biodegradable products to reduce carbon footprints, which is crucial for us. For instance, companies like Adidas aim to reduce their carbon footprint by 60 to 80 per cent by 2030. It is essential to address this issue at every level, from machine use and water use to electronic use and fabric recycling. Reducing carbon footprints is vital for everyone,” added Chen.
The company manufactures biodegradable chemicals in India and has around 20-40 USDA-certified products. The USDA certification indicates that a product contains more than 25 per cent bio-based content. Currently, over 30 of our agents have successfully obtained this certification.
In India, JINTEX Chemical Solutions began its operations in 2011, initially focusing on cotton due to the country’s established cotton manufacturing ecosystem. Around 2017 or 2018, the company noticed a global and domestic shift towards synthetic fabrics driven by changing consumer demand.
Cotton fabrics, while absorbent, become heavy and uncomfortable when wet, necessitating frequent changes. In contrast, synthetic fabrics, enhanced by innovations in moisture management and antimicrobial properties, are lightweight, vibrant, durable, and quick-drying. These advancements have led to a widespread preference for synthetic materials.
“Given Taiwan’s significant contribution to synthetic fabric technology, accounting for nearly 70 per cent of global production, we leveraged our expertise in nylon and polyester blends. Recognising the importance of controlling the entire value chain—from fibre production to fabric manufacturing, processing, and finishing—we assembled a team of top players from Taiwan to ensure competitiveness and quality,” said Ganesh HR, Director & Vice President, JINTEX Chemical Solutions.
When asked about the company’s presence in the technical textiles sector, Ganesh said, “Our efforts in Taiwan have been successful, attracting numerous inquiries from both existing and new players. We aim to expand our offerings in various fields, including natural fibres like jute and geotextiles, where we currently support colouring and functional finishes. However, this segment requires extensive understanding. We are active in the automotive sector, producing high-end UV protection chemicals to safeguard fabrics exposed to sunlight. While we are fully engaged in sportech, we have yet to explore other segments of technical textiles.”
Hsing Cheng showcases novel pre-treatment solutions
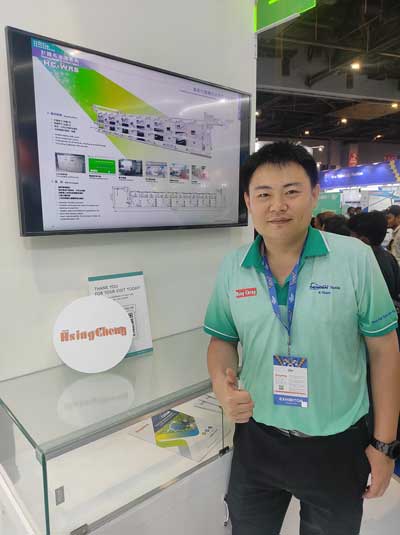
Steven Yeh, Dy GM, Hsing Cheng Machinery Industrial
Hsing Cheng Machinery Industrial Co LTD – a specialist in manufacturing textile pre-treatment machines, wet finishing machines, and automated packing equipment for the textile industry – presented its novel pre-treatment technology for synthetics and blends with Spandex at Taiwan Expo 2024.
“This time we are showcasing our desizing machine because it is crucial for the dyeing process. The Indian market is currently thriving and expanding every year. As a result, Hsing Cheng is considering the possibility of building a new factory in India to better serve our local customers,” commented Steven Yeh, Dy General Manager, Hsing Cheng Machinery Industrial Co Ltd.
The company, which was established in 1984, has been serving the Indian market for quite some time. However, over the past two years, there has been a significant shift towards synthetic textiles in India. Consequently, the company has increased its focus on the Indian market.
“We believe our future prospects in this market might surpass those in China, particularly in the dyeing sector of the textile industry. We provide comprehensive solutions for chemical machinery automation and also supply knitting machinery. Our A-Team acts as a complete dyeing solution provider to the textile industry,” added Yeh.
Tymico unveils machines for synthetic segment
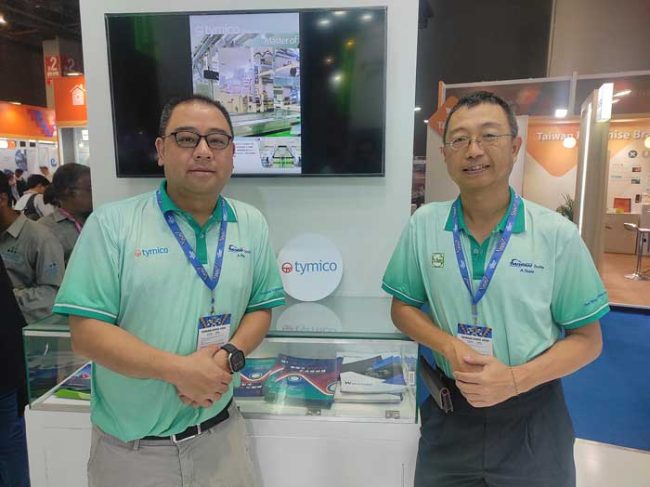
Wei-Chen Yin (left), Marketing Director – SE Asia Region, Tung Yang Machine Industry (Tymico)
Tung Yang Machine Industry (Tymico), which specialises in textile machinery with a focus on the synthetic segment for the past 30 years, showcased its Hi-air Computerised Stenter that gives customers great quality in fabric finishing. “At this expo, we are highlighting our core products, including large textile processing lines and finishing machines. Specifically, we are introducing our machinery for the Indian textile market, focusing on the direct polyester segment. We have been serving the Indian market for nearly 20 years,” stated Wei-Chen Yin, Marketing Director, South East Asia Region, Tung Yang Machine Industry Co Ltd (Tymico).
In the past 5-6 years, the Indian market has been stable for the company. Historically, Tymico did not consider India a major market due to its traditional focus on natural fibre cotton. However, since last year, the Indian market has been expanding its interest in synthetic materials, which has prompted their increased involvement.
“Our components are manufactured in Taiwan, assembled in Thailand, and then shipped to India. We have observed a growing demand for machinery, particularly driven by the rising interest in synthetic materials in India,” Yin added.
Logic Art offers smart automation solution for dyeing
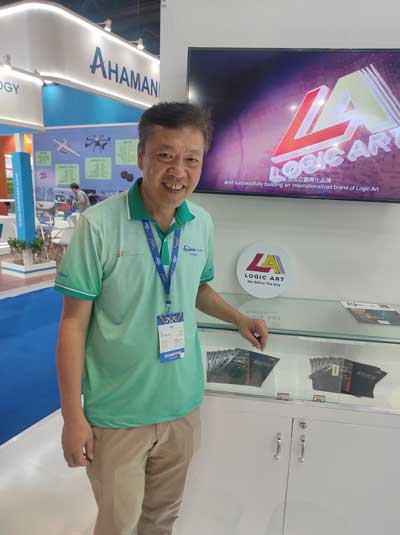
Steven Shen, MD, Logic Art Automation
Logic Art Automation Co Ltd – a key player in the Taiwan Textile A-team and the only integrated enterprise providing a comprehensive dye house solution globally – showcased its smart solutions for dye houses at the expo. “As a crucial equipment manufacturer and supplier in textile dyeing and finishing automation, Logic Art is the sole global provider of a comprehensive colour management solution platform. It integrates laboratory control with workshop operations, enabling Just-In-Time (JIT) production for intelligent manufacturing,” said Steven Shen, Managing Director of Logic Art Automation.
Logic Art, an expert of LA-Total solutions for smart manufacturing, is the world’s largest ODM equipment manufacturer for dispenser since 1993. It has dedicated for a long time in ‘integration of factory automation’, changing the inherent models of traditional industries, and creating smart production.
He added, “Logic Art Automation innovatively create smart dyeing and finishing plants by integrating laboratory dyeing formulas and processes, implementing LA-SPC central monitoring systems for dyeing machine networking, workshop dyeing auxiliary measurement and transportation systems, and setting machines.” Additionally, by combining ERP development, the company create intelligent production system equipment for dyeing and finishing plants, offering a Total Solution for automation equipment, and ultimately aiming to enhance the first-pass colour matching rate in dyeing.
“Global brands like Nike and Adidas are now focusing on reducing carbon emissions and their carbon footprint. With our new technologies, we emphasise saving energy and water while reducing the carbon footprint. Looking ahead, we plan to focus on the Indonesian, Vietnamese, and Indian markets,” noted Steven Shen.
Tong Geng eyes expansion in India via active wear
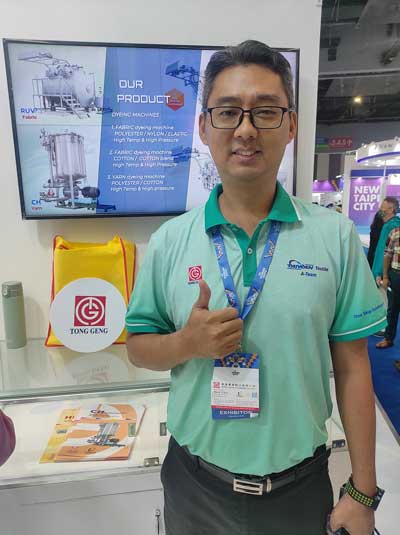
Mark Chen, GM, Tong Geng Enterprise
Tong Geng Enterprise Co Ltd, a manufacturer of dyeing machines for fabrics and yarns, caters to dye houses in the textile industry. Its machines are designed for dyeing both cotton and synthetic fibres, including those used in active wear and sportswear.
“Fashion trends are increasingly shifting from cotton to synthetic fibers. To meet this demand, we have introduced a dye machine specifically for synthetics, featuring a low decay ratio that significantly reduces energy consumption compared to traditional synthetic dye machines. Our machine operates with a liquid-to-fabric ratio of 1:5, meaning one kilogram of fabric requires only five liters of water. Traditional machines typically operate with ratios as high as 1:8 or 1:10,” explained Mark Chen, General Manager, Tong Geng Enterprise Co Ltd, Taiwan.
The Indian market is now focusing more on dyeing, with increasing inquiries about transitioning to synthetic dyes. This new method represents a significant change for many dye houses. Tong Geng’s solution is well-suited for this market shift, and is seeing more inquiries from regions such as Ludhiana, Ahmedabad, and Coimbatore.
“In the future, as more people wear active wear and sportswear, our presence in India will grow. We have partnered with agents in both northern and southern India to handle sales and services. Additionally, we have collaborated with dye houses in Thailand to demonstrate our machines in operation, providing customers with greater confidence in adopting new technologies. By showcasing our applications in these centres, we aim to increase awareness and drive sales,” concluded Chen.
Everlight Chemical introduces eco-friendly solutions
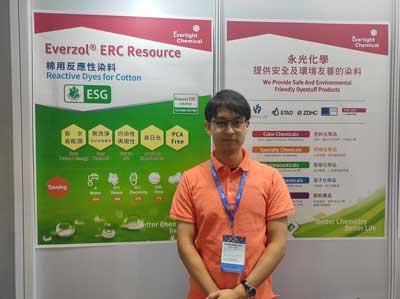
Leo Liu, Project Manager, Color Chem, Everlight Chemical Industrial Corp
Everlight Chemical focuses on the development of chemical synthesis technology, which has gradually become its core competency. The company has positioned itself as a high-tech chemical enterprise contributing to the well-being of mankind.
“Our core business is in dyes, specifically for the textile industry. We produce reactive dyes for cotton fabric, AC dyes for nylon and polyamide, as well as some auxiliary products. Recognising the environmental impact of the textile industry, particularly during the dyeing process, we have introduced a new product called Everzol ERC Resource. This solution uses significantly less water and operates at lower temperatures, which saves energy. For instance, a regular water washing process typically involves 10 steps, but with our ERC solution, it only requires four or five steps. Additionally, traditional dyeing uses 98-degree water, whereas ERC only needs 70 degrees, thus conserving energy,” said Leo Liu, Project Manager, Color Chem, Sales Div. II, Everlight Chemical Industrial Corporation, Taiwan.
The company launched this product last year and has since promoted it to customers in India and South Asia. The feedback has been positive, with customers reporting significant savings in water and energy during the dyeing process. The Everzol ERC solution is particularly effective for cotton fabrics.
“Currently, we are focusing on cotton, as it is widely used fibre in India. All these products are manufactured in our factories in northern Taiwan. In India, our growth plans include collaborating with local agents we have worked with for over two decades. These agents have a network across many provinces in India, allowing us to promote our eco-friendly products to a broader customer base. As part of Team A, we continuously revise our cost and pricing strategies for these products in India,” added Liu.
(With inputs from Divya Shetty)