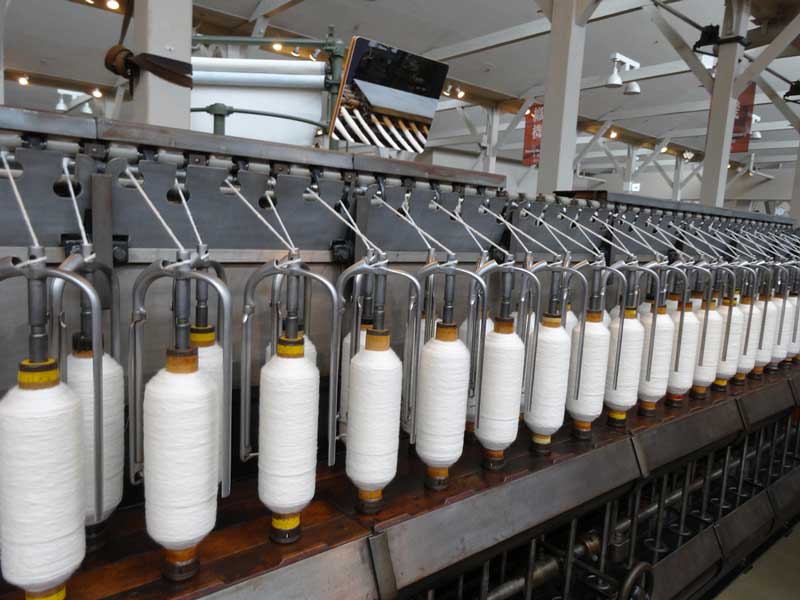
Spinning Woes
Examining the various challenges confronting the Indian spinning industry, Divya Shetty explores the root causes and potential solutions.
While the spinning industry holds a pivotal role in the financial and economic growth of country, it is currently facing a significant crisis. This is attributed to various factors. The spinning mills are on the brink of production closure because of a notable drop in the global demand for garments. This decline, in turn, is impacting the purchase of cotton yarn and fabric.
Subtle causes
Over the past decade, there has been significant expansion in spinning capacity, however, there are many reasons why the typically thriving industry is facing the challenges.
Over capacity: In last few years, there was a massive addition of spinning capacities as they witnessed an increased yarn import from China. China closed down approximately 1 or 2 million spindles and replaced old ones, prompting others to capitalize on the situation by adding capacity. Additionally, favourable state policies led to the construction of numerous mills in the country.
However, a shift has occurred in recent years. China and Bangladesh, major importers, have reduced their yarn imports, creating excess capacity in the Indian spinning industry. This situation is compounded by the impact of COVID, with Bangladesh increasing its internal capacities. Consequently, India, which holds a 25-27 per cent market share in exports, is grappling with reduced demand, especially as its main export destinations have diminished, informed an industry veteran. Currently, most spinning mills are operating at only 60-70% capacity due to a lack of demand. The country’s spinning giant, recognising the looming threat, has shifted its focus from the Indian market to prioritize export markets due to its heavy reliance on the spinning industry. To address this, they have established a subsidiary in Dubai for value addition, exporting machines worldwide.
But unfortunately, few companies could not stand the turmoil, a prime example being Sintex Industries. The company inaugurated a 1 million spindle plant located near the port, primarily influenced by favourable policies of the Gujarat state government and the lucrative Chinese market. The decision was driven by cost-effective power and various other advantages. The plant was strategically situated just a few kilometres from the port. Unfortunately, following the market downturn, Reliance took over that facility.
Chinese imports: Many Indian manufacturers have urged the government to either stop the import of Chinese fabrics in the Indian markets or impose stringent custom duties on them. The imported fabrics are significantly more affordable, which is the underlying cause. Nimish Parekh, Vice President, Gimatex Industries, says, “Imported fabric, particularly synthetic fabrics, is considerably cheaper than Indian domestic prices. Major producers like Reliance and Grasim contribute to the high cost of synthetic fibre, making it challenging for spinners to compete with Chinese, Indonesian, and other imports. The elevated power and labour costs add to the competitiveness issue.” Vineet Ajitsaria, Director, Sivanta Spuntex, also adds, “The government needs to oversee Chinese imports, as it is a primary reason behind this degrowth. The market disruption caused by war has created excessive pressure on the domestic market due to insufficient export support. I request the government to either halt Chinese imports or impose custom duties on them, providing significant support.”
Red Sea Crisis: The Red Sea crisis, also known as the United States–Iran proxy war, began on October 19, 2023 when Yemen’s Houthi movement initiated a series of attacks, targeting ships in the Red Sea. Hence, the industry is requesting the government’s support to help sustain exports amidst the Red Sea Crisis. This crisis has caused significant impacts on textile exports, including shipment delays and increased costs. Militants have been attacking cargo ships passing through the Red Sea, which is one of the busiest trade routes connecting Europe and Asia through the Suez Canal. As a result of the attacks, ships are taking a 6,000-nautical-mile detour around Africa, adding 15 days of transit time. This detour is causing a steep increase in freight rates and insurance premiums.
“I expressed serious concerns about the deteriorating situation in the Red Sea and how it is affecting textile and clothing exporters. Freight rates to European ports from India have already increased by 40 per cent, with further possible increases in rates soon. The rise in shipping costs is becoming an additional burden for textile and clothing exporters. Also, urged the government to support textile and clothing exporters to help them handle the situation and enable them to survive and sustain their exports. The majority of textile and clothing shipments pass through the Suez Canal, which connects the Red Sea and the Mediterranean Sea,” wrote to government Bhadresh Dodhia, Chairman, SRTEPC, in his recent social media post. Freight rates have stabilised after a steep increase during COVID-19, and the current crisis in the Red Sea has once again pushed up freight rates, which is not good for exporters. If the crisis continues and is not contained quickly, it will not only harm exports from India but will severely disrupt the global supply chain and hurt the world economy.
International wars: Global economic slowdown because of wars have added to the supply chain disruptions and the risk of stagflation, has led to a sharp slowdown in global growth. Inflation, and weak consumer spending also adds to the challenges. “Previously, we exported 70% of our products globally, but for the past year and a half, exports have ceased. Key customers like Latin America, Egypt, Bangladesh, and others are not placing orders due to on-going wars,” informs Ajitsaria. Zaveri adds, “On-going wars have resulted in a lack of demand from the European and US markets, causing a stagnant market for over a year. We anticipate a positive change in the near future. The entire value chain, not just spinning, has suffered significantly due to geopolitical disruptions. Hopes are pinned on a shift in the scenario in the upcoming quarters, specifically in April.”
Unsatisfactory government policies: The textile industry had received critical support worth Rs 16,920 crore under the Emergency Credit Line Guarantee Scheme (ECLGS0, constituting approximately 6 per cent of the total disbursement of Rs 2.82 lakh crore as of September 30, 2022. However, the spinning segment is in a severe crisis with a 50 per cent decline in cotton yarn exports, a 23 per cent drop in overall exports of cotton textiles, and an 18 per cent reduction in total textiles and clothing products during the financial year 2022-23 compared to the previous year. Hence, the associations like CIT and SIMA have requested the government for an extension of the one-year moratorium for repayment of the principal amount, and conversion of three-year loans under ECLGS into six-year term loans.
The industry is also seeking reduction of GST on raw material, including viscose and polyester staple fibre to 12 per cent from the existing 18 per cent, resulting in zero revenue loss to the government. The associations have also been receiving appeals to impose anti-dumping duty on import of polyester spun yarn (PSY) under ASEAN Free Trade Agreement (FTA) and making import of cotton duty free as this will provide a level playing field for all the stakeholders in the textile sector.
The consqeuences
Spinning mills across the nation, particularly in Coimbatore, Erode, Ludhiana, and Surat, have experienced temporary closures in the last six months. The primary reason for this has been their inability to cope with the rising costs of raw materials and the falling prices of yarn. The mills are grappling with steep electricity bills due to increased tariffs, encompassing peak-hour and fixed demand charges. Moreover, the spinning mills have been adversely affected by the 11 per cent tax imposed on cotton imports.
This year’s Diwali season, traditionally considered the peak period for the entire industry, witnessed a complete lack of demand for fabrics. Even after the shutdown, the mills have overproduced and it is burdening the nation. Zaveri comments, “The absence of exports means that the domestically produced goods are flooding the market. However, there is a limit to the volume the nation can absorb. The production exceeds domestic requirements, and despite associations presenting their needs, uncertainty looms regarding when authorities will address this demand.”
Thread of hope
Despite numerous short-term and long-term challenges affecting the spinning sector, the industry maintains optimism about its future. The potential positive impact of forthcoming government policies, coupled with persistent advocacy efforts by the association, could serve as a silver lining amidst the challenges. Government’s proactive measures, such as the MITRA scheme, showcase a commitment to the spinning industry’s growth. The recent Comprehensive Scheme Guidelines for the Knitting & Knitwear Sector and the National Technical Textiles Mission (NTTM) further highlight dedication to innovation. The allowance of 100 per cent FDI in textiles and the strategic move of the Production-linked Incentive (PLI) Scheme for manmade fibre and technical textiles over the next five years are promising steps. These initiative have the potential to benefit a significant part of the spinning industry. If the government could fast forward the implementation of these initiatives, it would undoubtedly accelerate the positive impact on the industry. Quick spread of these initiatives would benefit not just the spinning industry but the entire ecosystem, promoting widespread growth.
Parekh suggests, “The government could implement BIS standards on spinners, mirroring the successful approach taken with polyester yarn, providing relief to polyester spinners in India. Encouraging innovation is crucial, considering the repetitive use of the same yarn and patterns. Government subsidies can support innovative endeavours. Exploring opportunities, technical textiles offer a vast potential, and there is substantial demand for Siro Compact Yarn in spinning. To thrive in this competitive market, embracing innovation is essential for survival.”
Nivedan Churiwal, Managing Director, BSL, also adds, “The prevailing challenge is not in terms of volume, but rather lower margins due to diminished demand. It seems we are currently at the bottom, or slightly better than the bottom. Looking ahead, the cyclical nature of the business is expected to manifest every two to three years, bringing about better prospects.”
Also, emerging sectors like home textiles ans technical textiles can prove to be a boon for the spinning industry. As more companies venture into technical textiles, the demand for skilled employees will rise, creating opportunities and contributing to overall economic growth. So, both home textiles and technical textiles seem to be holding some real promise for our spinning sector. Pratik Gadia, Founder, The Yarn Bazaar, comments, “With consumers getting more conscious about their choices, sustainable yarns are getting quite the spotlight. It’s interesting how the shift towards sustainability aligns with what consumers want and adds another layer of opportunity for our spinning sector.”
The industry as a whole is eagerly anticipating a positive transformation in the near future. The broader value chain, encompassing not just spinning but the entire sector, has borne the brunt of substantial setbacks attributed to geopolitical disruptions. Expectations are high for a notable shift in the prevailing circumstances in the upcoming quarters, with a particular focus on the prospects unfolding in April.