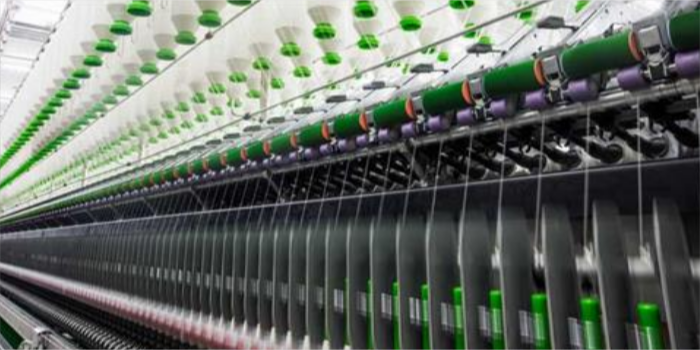
Flexible solutions for ring spinning
Rieter’s G 38 ? an all-rounder with a fully electronic drafting system ? is the ideal solution for producing high-quality yarns flexibly.
The Rieter ring spinning portfolio includes machines for a variety of customer needs. The “workhorse” G 37 with the semi-electronic drafting system is now available in a new, attractive configuration with up to 1 200 spindles. The G 38 ? an all-rounder with a fully electronic drafting system ? is the ideal solution for producing high-quality yarns flexibly. Intelligent features and automation solutions like the intelligent spindle monitoring and the piecing robot ROBOspin enhance efficiency.
The ring spinning machine G 37 with the semi-electronic drafting system meets all requirements for efficient yarn production. It scores with reliability, consistent performance and high productivity. This machine is in particularly high demand from customers who produce the same yarn types over longer periods of time.
Various features of the machines have been specifically designed to increase productivity and machine efficiency. The fast automatic doffing with a cycle time of less than 120 seconds comes as standard and improves the productivity of the G 37. With the integrated SERVOgrip system, doffing can be performed without underwinding. Thanks to the individual spindle monitoring system, ISM basic, the operator is guided directly to spindles with ends down which enhances the machine efficiency. Durable and economic Bräcker spinning rings and Rieter aprons ensure consistently high yarn quality and a reduction in machine downtimes.
CATEGORIES Spinning