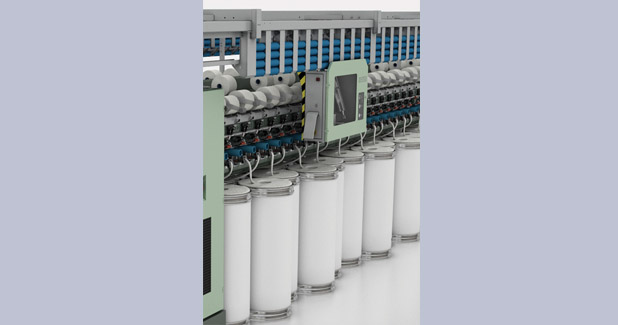
Semi-automated rotor spinning with maximum flexibility
The semi-automated rotor spinning machine is the ideal solution for customers with personnel availability who want to use low priced raw materials.
New R 37 offers high yarn purity over a wide range of applications.
The semi-automated rotor spinning machine is the ideal solution for customers with personnel availability who want to use low priced raw materials. It enables cost-efficient spinning of rotor yarns based on high productivity, low energy consumption and personnel-saving machine ergonomics – with maximum flexibility in terms of the raw material used.
The innovative technology of the new R 37 enables excellent trash extraction and reduces the ends down. The R 37 therefore offers up to 8 per cent higher productivity than other semi-automated machines.
A major contributory factor to this productivity is the optimised spinning box, now with exchangeable trash channel. This enables the efficient processing of a much wider range of raw materials than previously, particularly those with a high trash content. Using a trash channel specific to the raw material secures optimum trash extraction and ensures that the rotor groove remains clean for longer. This greatly reduces ends down. Yarn purity and therefore imperfections and Classimat values are also considerably improved. Customers benefit from a reliable and robust spinning process – with considerably fewer ends down than on other machines. The previous model, the R 36, already consumed 5 per cent less energy than competitor models, thereby greatly reducing production costs.
Low energy consumption
The previous model, the R 36, already consumed 5 per cent less energy than competitor models, thereby greatly reducing production costs. This is due to the modern drive concept which is also used in the R 37.
Automatic package change
The particularly low working height of the R 37 combined with the AMIspin piecing device makes the machine easier to work with. As a result, up to 8 per cent more spinning positions can be served by the same number of operators compared to other machines. Newly an optional robot, the ROBOdoff, changes the full packages without interrupting the spinning process. In this case all doffed packages have the same defined package length. ROBOdoff enables more efficient work organisation and replaces the exhausting process of manual doffing along the machine.