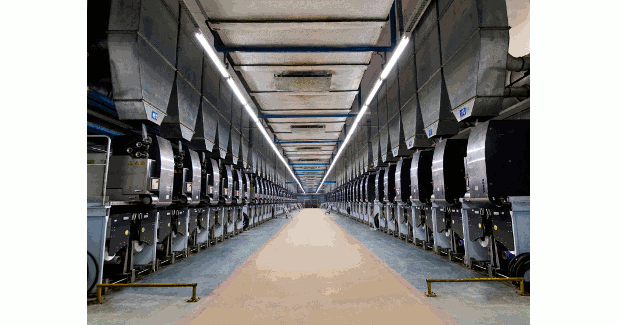
Recycling of polyester from waste on our agenda: M Bhageria
Filatex India, a provider of speciality polyester, nylon, and polypropylene mono filament yarns, has always been at the forefront in providing sustainable measures.
Filatex India, a provider of speciality polyester, nylon, and polypropylene mono filament yarns, has always been at the forefront in providing sustainable measures. While speaking to the ITJ, Madhu Sudhan Bhageria, Chairman & Managing Director, Filatex India, said, “We have been trying to see that we do the least possible pollution at our units. We plan to start recycling of polyester from the waste produced. We plan to recycle yarn from bottled waste. This will also help us in reducing the carbon footprint.†Filatex manufactures multi filament yarns of polyester – POY, FDY and DTY.
Excerpts…
What is the market size for these commodities? Also, what are its various applications?
The combined market size is roughly around 4 million tonne (MT) annually. POY is basically a intermediary product. The final product are FDY and DTY, which are used for making fabrics. POY [as it is] cannot be used for making fabrics.
Separately, the market share for FDY and DTY will be around 1 MT and 3 MT respectively. These are just broad approx. figures as there are no statistics available.
FDY and DTY are used to make polyester fabrics. These are also used for home furnishings, children wear, ladies wear, etc. It can be used as a combination or separately depending on the fabric that you are making. The quality of the fabric depends on the requirements of the customers.
How much is your annual production capacity?
The production capacity [as of now] is around 3,28,000 tonne. In this, around 2,70,000 tonne would be yarns and balance of 60,000 tonne is chips.
Which are your stronger markets in India and abroad?
We supply our products pan India. Primarily, the market is around Surat, Mumbai, Ichalkaranji, Bhiwandi, Panipat, Ludhiana and Delhi NCR. These are major markets. Other markets include Eastern and the Southern regions too, but these are smaller ones.
Globally, we export to more than 40 countries. Major countries include: Brazil, South Korea, Bangladesh, Turkey, Poland and Egypt. Last year, around 20 per cent of our business was export, while 80 per cent was domestic. We mainly export DTY. Out of the total volume of export, DTY will be around 80 per cent. Balance 20 per cent would be chips and FDY. We export DTY more because DTY is little more labour-intensive, and India is more competitive in pricing as compared to China or any other country. In FDY, China is still more competitive than India in pricing.
How is India faring compared to countries like Bangladesh and Vietnam that are growing rapidly in exports?
Vietnam and Bangladesh are growing because of two major reasons: firstly, the labour cost is less compared to India; and secondly they have favourable taxation for exports to Europe and the US. Our products are taxed higher as compared to Vietnam and Bangladesh by the US and Europe.
Who all are the leading players in this sector?
Reliance Industries, Bhilosa Industries and Wellknown Polyesters are the top three players. We are No. 4. If you talk about capacity-wise, Alok Industries should be No. 4, but they are not running at a full capacity at present.
What are the USPs of your products as compared to these leading players?
The main USP is to give good quality product and good service to the customer. If someone buys a product at Filatex, he is assured of a good quality product. Getting goods at the right time and the right goods is also very important. If you don’t give what the customers want at the right time, then it is not good for the customer. Giving timely service is equally important.
In terms of FDY and DTY, what are the latest innovations taking place in this industry?
Not much, however there are minor innovations are happening. Air texturing is one such innovation. It is like giving slub effect in the yarn by air. At Filatex, we do not have such machine. In our next expansion plan, we plan to put up air texturising machine too. Apart from these, there are no major innovations happening in this field.
The POY machines are from China, while FDY machines are from Germany. In texturising, Indian machines are pretty good. In FDY, most of the companies will be having Japanese or German machines because there you need more quality. POY is a mix of Chinese, Japanese and German, while texturising is mostly Indian.
What is the annual budget allotted for R&D?
There is not much R&D happening in these products as these are commodity products. Total percentage spent would be very minuscule of total revenue.
What are the reasons behind low output and technological backwardness of the Indian textile industry?
In the industry that we represent, the utilisation rate is more than 90 per cent. Speaking about the textile industry in general, availability of labour is a big problem. No one wants to work on machines anymore. Today, getting good workers is a tough task. In Spun Yarns, the requirement of workers is at least four to five times more than that for filament yarn. The textile industry is using less capacity because there is a dearth of workers.
What are the challenges that the Indian polyester yarn business is currently facing?
Our industry has been given step-motherly treatment by the government. The government keeps on promoting cotton. Synthetic yarns have been highly taxed even though today’s common man fabric is polyester. Cotton, which is mainly for rich people, is taxed at 5 per cent; whereas, we are taxed at 12 per cent on yarn, while our raw materials is taxed at 18 per cent. We are not included in the TUF scheme either. The benefits of textile policy initiatives are not available to polyester, which is the most dominant fibre globally.
In the last few years, China has started to become costly. This is why the Indian market has started to come up. Earlier India was only into cotton.
… then what are your suggestions for the government?
The government should bring in polyester spinning into the textile domain. We, at present, are under the Ministry of Fertilizers and Chemicals. We should be put under the Textile Ministry. Generally, most of the products are classified on the basis of final product and our final product is a part of textile. Only our raw materials come under petrochemicals.
Rationalise our GST from 18 per cent on our raw material to 12 per cent and custom duty on PFY to 10 per cent, which is now at 5 per cent. Changing our Ministry to textiles will help both – the Textile Ministry as well as our industry. This is because, in the last few years, the growth in textile have come only from polyester. If the textile has grown worldwide, around 70 per cent growth has come from polyester. Only 30 per cent has come from cotton, man-made and other yarns. We need support from the government to take this up.
China is at the top of polyester production. Indian market size is currently at 6 MT; the next country is around 1 MT. There is a huge gap between No. 2 and No. 3. But now since China is slowing up its speed because of a number of reasons, India should be able to take up that position. For this, we need government’s support. Without any incentives and interests, it will be very difficult for India to put up large capacities to fill up that vacuum. Every year, around 2.5 to 3 million MT polyester filament yarn is needed in the world and that is mainly provided by China.
How important is sustainability at Filatex?
We are a zero discharge company. Everything we produce is recyclable. The energy required to produce a cotton yarn is roughly five times than that you require to produce a polyester filament yarn.
For e.g: At Filatex, we make 150 denier, which is actually equivalent to 30s count of cotton. So the 30s count would like around five units to convert raw cotton to yarn. Whereas, for DTY and FDY, we require only one unit. Similarly, if we talk about the man-hours required, it will be around four to five times. It is the same with capex too. It’s just a myth that cotton is natural and cheaper fibre to process.
We have been trying to ensure that we do the least possible pollution at our units. We plan to start recycling of polyester from the waste produced. We plan to produce yarns from bottled waste. This will also help in reducing the carbon footprint.
What are your plans for FY 2020?
We are doing more expansion in POY and DTY. In this calendar year, we would be adding 62,000 tonnes of POY and 72,000 tonnes of DTY. After 2020, we plan to increase our exports too and add captive power plant to reduce our power cost.