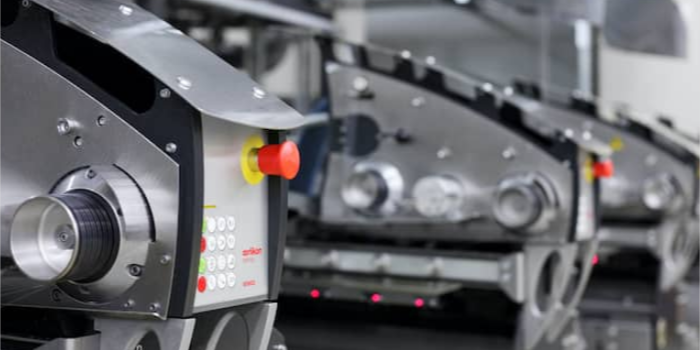
POY process now even more energy-efficient
The requirements-specific design of the compact inverter unit ensures functional optimisation of the winder’s control functions.
Following several years of development with partner Siemens, Oerlikon Barmag kicked off serial production of its new drive unit for POY systems at the beginning of the year. The new component makes stands out above all with regards to energy efficiency. The requirements-specific design of the compact inverter unit ensures functional optimisation of the winder’s control functions. And the new component is used in conjunction with a performance-optimised chuck motor. This means that energy savings of up to 3 per cent can be achieved for the take-up. “In the case of a 1,000-position system, this represents a saving of around 1,20,000 euros a year, depending on the relevant local energy costs. The many years of collaborating with our partner Siemens means that we are always state-of-the-art in terms of control technology. With our e-save-certified solutions, we are consistently able to offer our clientèle sustainable technology for the efficient manufacture of yarnsâ€, states Arnulf Sauer, responsible for winder technology at Oerlikon Barmag.
Further customer benefits include a significant reduction in cables and cable trays. The reduced number of switching cabinets also saves space. Following intensive field tests at two well-known customers last year, the compact inverter unit was finally released for serial manufacture at the beginning of 2020. There are plans to deliver several thousand positions with the new component this year.
Less wear and superior fibre quality
Technological changes to Oerlikon Neumag’s Baltic crimper thrust pad contacting device have resulted in considerably reduced friction in the crimper rolls and hence less wear and fewer metal particles contaminating the crimped staple fibres. Thrust pads close the gap between the crimper rolls on either side. Normally, these thrust pads are continually pressed – under high pressure – against the sides of the crimper rolls. Wear and metal debris on the thrust pads is the result of this constant contact. The metal debris can contaminate the fibres, something that is particularly undesirable in hygiene applications.
With the new system, the thrust pads are pressed against the rolls with less pressure and then fixed into place. This prevents fibres from being caught and the frictional force between the pressure disk thrust pad and the crimper roll is minimised. Pilot applications have demonstrated that metal debris from the pressure disks thrust pads is dramatically reduced, making them between three and seven times more durable. The new thrust pad contacting device is now available.
Oerlikon engineers materials, equipment and surfaces and provides expert services to enable customers to have high-performance products and systems with extended lifespans. Drawing on its key technological competencies and strong financial foundation, the Group is sustaining mid-term growth by addressing attractive growth markets, securing structural growth and expanding through targeted mergers and acquisitions. A leading global technology and engineering Group, Oerlikon operates its business in two Segments – Surface Solutions and Manmade Fibers – and has a global footprint of more than 11,100 employees at 182 locations in 37 countries. In 2019, Oerlikon generated CHF 2.6 billion in sales and invested more than CHF 120 million in R&D.
With its Oerlikon Barmag, Oerlikon Neumag and Oerlikon Nonwoven brands, Oerlikon Manmade Fibers segment is the world market leader for manmade fibre filament spinning systems, texturing machines, BCF systems, staple fibre systems, solutions for the production of nonwovens and – as a service provider – offers engineering solutions for the entire textile value added chain. As a future oriented company, the research and development at this division of the Oerlikon Group is driven by energy-efficiency and sustainable technologies (e-save). With the supply of continuous polycondensation and extrusion systems and their key components, the company caters to the entire process – from the monomer all the way through to the textured yarn. The product portfolio is rounded off by automation and industry 4.0 solutions. The primary markets for the products of Oerlikon Barmag are in Asia, especially in China, India and Turkey, and – for those of Oerlikon Neumag and Oerlikon Nonwoven – in the USA, Asia, Turkey and Europe. Worldwide, the segment – with just under 3,000 employees – has a presence in 120 countries of production, sales and distribution and service organisations. At the R&D centers in Remscheid, Neumünster (Germany) and Suzhou (China), highly-qualified engineers, technologists and technicians develop innovative and technologically-leading products for tomorrow’s world.