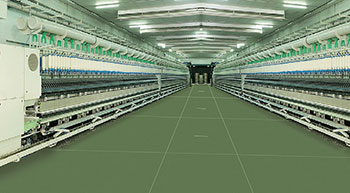
Opportunities galore
Coimbatore, known as the textile hub of Tamil Nadu, houses a large number of small, medium and large textile mills. It also has textile research institutes like the Central Institute for Cotton Research (CICR), South Indian Textiles Research Association (SITRA) and the Sardar Vallabhai Patel International School of Textiles and Management.
Coimbatore, known as the textile hub of Tamil Nadu, houses a large number of small, medium and large textile mills. It also has textile research institutes like the Central Institute for Cotton Research (CICR), South Indian Textiles Research Association (SITRA) and the Sardar Vallabhai Patel International School of Textiles and Management. The city also houses two of the Centers Of Excellences (COE) for technical textiles proposed by Government of India, namely Meditech, a medical textile research centre based at SITRA, and InduTech based in PSG College of Engineering and Technology. The Coimbatore region is famed for the quality of its cotton and dyed fabric. The growth of textiles naturally led to the inception of textile machinery manufacturing. Today, some of the best known global brands in textile machinery and component manufacturing are home. The neighbouring town of Tirupur is home to some of Asia?s largest garment manufacturing companies, exporting hosiery clothes worth more than Rs 50,000 million.
Coimbatore, a city residing in the hills of Nilgiris is a second largest in Tamil Nadu. This is also known as a cotton town. Kovai is the other name of Coimbatore. It has a flare of cotton production because of the black soil of that land which suits cotton growing. If Coimbatore is known for cotton production, Tirupur is known for knitting. Tirupur is also known as a knit city. It is 50 kms far away in the east from Coimbatore. Forty five countries are buying from Tirupur and they are visiting that regularly. Tirupur is the only city which is doing 65 per cent of knitwear export alone. The city Erode is known for handloom weaving and carpet manufacturing. It also has large scale cotton ginning mills. Erode along with Salem is known as the home of textile weavers.
Tirupur, the heartland of the knitwear industry in India, has a supplier base which consists essentially of manufacturer who are mostly integrated forward or backward if not vertical. Tirupur textile industry has units all along the value chain of knitwear starting from spinning, knitting wet processing, printing, garment manufacturing and exports. In addition there are ancillary units supplying buttons, laces, embroidery, cones and yarn processing etc. Despite being late entrant, Tirupur’s annual production far exceeds that of other knitwear clusters. There are more than 500 production units which are involved in exports of knitwear from Tirupur. Entire Tirupur cluster generates direct employment for over 3,00,000 persons. Knitwear exports from Tirupur cluster have registered a growth 15.5 per cent in terms of rupee and 15.9 per cent in terms of foreign currencies during the just ended 2014-15, knitwear products worth Rs. 20,730 crore were exported from Tirupur cluster during 2014-15 fiscal when compared to Rs 18,000 crore worth of exports registered in the previous fiscal.
The Southern India Mills? Association (SIMA) is very active in the Coimbatore region and governs most of the textile industry in South India. SIMA has a membership spread across the southern states and protects the interests of the textile mills and its workers. To encourage textiles in the state, SIMA is organising Texfair 2016 during May 20-23, 2016 at the CODISSIA Trade Fair Complex, Coimbatore. Texfair 2016 is intended to bring together the manufacturers and suppliers of textile machinery, spares, accessories, components and the consumers such as textile mills, powerlooms, handlooms and knitters under one roof.
All the earlier eight events of Texfair starting from 2001, attracted several technocrats, CEOs and shop floor technicians including fitters and electricians from all the sectors of the textile industry across the country and greatly benefited both the buyers and sellers/suppliers and had gained popularity in the textile community.
TN accounts 50% yarn export
Dr G Ramakrishnan, Senior Associate Professor, Department of Fashion Technology, Coordinator KCT-TIFAC CORE in Textile Technology & Machinery, Kumaraguru College of Technology, shared the current state of textile industry in Coimbatore and Tirupur. He said, ?The textile industry in Coimbatore, the backbone of the economy in the region, is at a crossroad. It has been hit by a series of negative developments such as rising cost of raw materials, labour and power; the misery has been compounded by the decline in demand, creation of excess capacity and high financial cost. Coimbatore region accounts for around 15 per cent of India?s cotton spinning capacity. Textile mills in Coimbatore ? they have to import cotton from other states/countries and send their finished products like cotton yarn/cloth to other centres, incurring huge transportation cost both ways.?
He added: ?The cotton spinning mills of Tamil Nadu also account for more than 50 per cent of the yarn exports of the country ? a testimony to the entrepreneurial spirit of the Coimbatore region. With a low asset turnover, spinning is a capital-intensive industry. The poor power situation is now affecting the industry?s prospects more than any other factor. The mills will need to automate more to tackle the labour shortage that seems to loom as also to keep costs down.?
Speaking on the future of textile industry in Coimbatore region, Dr G Ramakrishnan avers: ?The future of the industry will hinge more on how raw cotton prices behave and the ability to service debts with lower margins. Banks and financial institutions need to take a pragmatic and long-term view and make funds available for working capital. The state government should ensure availability of power at a normal rate and also have a liberal and progressive policy on labour. The management style requires a dramatic change as any consumer product needs a large marketing and design team. Despite its achievements, the industry has also been facing several headwinds in the past 4-5 years like the unprecedented fluctuation in cotton prices and competition from countries like Pakistan, Bangladesh and Vietnam in garment exports. Unless the manufacturers in this sector moved closer to the customers by adding value to their products, they would not be able to bear the relentless cost increase. The Central Government had announced the integrated processing development scheme long back, the scheme is yet to take off despite extending 25 per cent capital subsidy. Extending a financial support up to Rs 2.5 crore to integrated textile parks, which would provide ample opportunity for the handloom and powerloom sectors to focus on consolidation, integration and value addition which are the pre-requisites to achieve a sustained global competitiveness and growth.?
Dr G Ramakrishnan said, ?Tirupur textile industry is still facing some problems like labour shortage and environmental problem.Tirupur has no star hotels is also a great drawback for the exporters. Due to the lack of star hotels most of the visitors stay in the Coimbatore and they visit Tirupur. So it causes inconvenience to the foreigners and because of this the industry loses some of its business. Another issue which affects is the shortage of skilled and unskilled laborers. The owners of the process house are regulated by stringent legislations of the Tamil Nadu state for the environment controls. In Tirupur the process houses must have Reverse Osmosis or Zero Effluent Discharge plant or else the existing plants have to close and application of new plants will not be approved. Therefore, the amount of investments in terms of plant & machinery and overheads in the integrated garment industry is quite high as compared to other knitwear clusters and thus requires efficient management for timely Return on Investment. In spite of the fact that the Tirupur town is reeling under acute infrastructural shortage, the Tirupur knitwear exporters are able to make a mark in the international sourcing map of the textile industry because they work as a group and help each other for a common cause. Various industry bodies were demanding that speedy execution of free trade agreement with European Union and Canada could help the knitwear exporters here increase their market share.These apart, different stakeholders were asking for steps to reduce interest rates on credit needed for capacity expansion, an increase in the duty drawback rates and initiation of steps to ensure level playing fields in commerce with certain competitor countries for enhancing the manufacturing prowess of the knitwear manufacturers here, among others.Two obstacles noticeable in Tirupur which need immediate considerations are: acute shortage of water and ban on commercial boring to draw water from earth has made the wet process on to fabric/garment a very difficult task, especially in future.?
No headway in product innovation
Thilagavathi Govindharajan, Professor, Department of Textile Technology at PSG College of Technology, Coimbatore, said, ?Coimbatore and Tirupur have witnessed muted growth in recent years in the traditional textiles segment like knitwears and looms. This could be on account of stiff competition from countries like Bangladesh and China, lack of product differentiation, price anomalies, currency fluctuations etc. Added to this there has not been much headway in product innovation and manufacturing practices.?
T Govindharajan added, ?In our opinion, diversification of products using synthetic fibres and blends and other value added products will help sustain them in the market. At the same time, synthetic raw materials are expensive due to import and other duties. In addition, branding and new designs developed by the companies on their own will definitely help them to have an edge in the market. As a diversification strategy, technical textiles offers a good scope with the potential for technical textiles is largely untapped in India and is an emerging area with a projected growth rate of about 20 per cent year on year. Premium product development using engineered fabrics for performance applications in this sector is essential.?
To bridge the knowledge gap, the government has facilitated setting up of Centres of Excellence (COEs) to provide infrastructure support at one place for the convenience of manufacturers of technical textiles.
The government has thus set up eight COEs across the country in collaboration with institutions and research associations. One such COE for Industrial Textiles, named PSGTECHS COE for Indutech set up by the departments of Textile Technology and Automobile Engineering of PSG College of Technology with funding from the Ministry of Textiles. It provides world-class facilities for testing of products of identified segments of technical textiles, indigenous development of prototypes, commercialisation, in-house training of core personnel from the technical textile industry and knowledge sharing with stakeholders.
Coimbatore-based Lakshmi Machine Works Limited (LMW) is today a global player and one among the three manufacturers of entire range of textile spinning machinery from blow room to ring spinning.
LMW introduced a range of machines during the recently-concluded ITMA event in Milan. The following were at display and the live demonstration of the products: card silver system – Card LC636; combing system – Comber LK69, Autoleveler Drawframe LDAZ; ring spinning system – Compact change gearless ringframe LRJ9/SX; components and parts; and yarn and fabric display.
LMW was the first to launch world?s fastest comber LK69 and has been successfully working across the globe at 600 npm. Compact Ring frame LRJ9/SX with 1824 spindles is designed to cater to customers requirement of ease of producing wide ranging counts, value added yarns Compact, Slub, multi count, multi twist and core yarn with various fibres and with the unique change gearless drafting drive.
Textiles always a sunrise industry
T Balamuralikrishna, Senior GM ? Marketing & Sales, and G Mani, Senior GM ? Global Service at LMW, spoke about their company?s plans for the upcoming Texfair event in Coimbatore. They expected enhanced customer satisfaction through addressing their needs both: to supply and enhance/ensure the maximum uptime of the machines in the field, and to enhance the life cycle of the products.
?New rings, new spindles, performance enhancement kits (upgrades), spare parts for all LMW machinery, conversion kits and mechatronic will be at display at the TEXFAIR 2016,? said the LMW pair. They further added that LMW is very keen on the life and health of the machines. Utmost care is taken in the design & manufacturing stages to ensure precision of the components and parts in order to meet customer expectations.
LMW?s products are equipped with better productivity, quality and automation that deliver quicker Return on Investment to the customer. With a LMW machine customer can expect more savings on the investment made on project cost.
Speaking on the problems & prospects of the industry, T Balamuralikrishna and G Mani said, ?The Textile Spinning Industry in India is cyclical. Cotton production (monsoon) and price, government policies (including various duties & taxes) and in general the economy are the factors effecting the prospects of the industry. As said the Indian textile industry is always a sunrise industry. The entire value chain of the Indian textile industry is doing well and is poised to grow at a rapid pace in the coming years irrespective of its cyclical nature, because of the following reasons: rising demand in exports, increasing demand in domestic market due to changing taste and preferences, growing population driving demand for textile, growing incomes, increasing urbanisation, increasing travel and cultural changes.
S Senthilkumar, Managing Director of Simta Machinery Pvt Ltd, who is also participating at Texfair in May, spoke on their plans for the event. He said, ?We will be displaying SIMTA JACOBI, overhead travelling cleaners, bobbin transport systems, SIMTA-synthetic spindle tape and SIMTA cleaner rollers for various applications besides the clearer rollers, cleaning machines and auto feeders.
At Texfair, S Senthilkumar anticipates vibrant exhibitors and look-out for a fairly large number of visitors to walk-in with a special focus to look for the right engieering at affordable costs.
SIMTA is an integrated group of textile engineering companies, consisting of tapes manufacturing, overhead travelling cleaners, bobbin transport system, clearer rollers, sheet-metal engineering and industrial fabrics divisions located at spread-out geographies.
Coimbatore and Tirupur have witnessed muted growth in recent years in traditional textiles segment like knitwear and looms.?
– T Balamuralikrishna, Senior GM ? Marketing & Sales, and G Mani, Senior GM ? Global Service at LMW
We anticipate vibrant exhibitors & look-out for a fairly large number of visitors to walk-in with a special focus to look for right engieering at affordable costs.?
– S Senthilkumar
MD, Simta Machinery Pvt Ltd
Growth oriented budget: SIMA chief
The Union Budget 2016-17 has come out with nine thrust areas to enable the country to achieve a sustained growth rate despite slowdown in the global economy. M Senthilkumar, Chairman, The Southern India Mills? Association (SIMA) has welcomed the nine pillars of growth trajectory budget marking at developing infrastructure, skill upgradation, agriculture development (doubling farmers income by 2022), health care, social development, education, etc. SIMA chief has also welcomed the nine point agenda to ensure compliance, ease of doing business, curbing black money, providing opportunity for declaring undisclosed income, etc.
With regard to textiles, he thanked the Government for continuing optional Cenvat route on cotton textiles which was the main demand of the association. He has expressed his gratitude to the Prime Minister, Finance Minister and the Government for allocating Rs 1,480 crore for Technology Upgradation Fund Scheme (TUFS). He has stated that additional funds would be required to meet the pending subsidies since September 2014. Senthilkumar has also welcomed the reduction of basic customs duty on MMF from 5-2.5 per cent though the association has demanded for total withdrawal. He has stated that reduction in customs duty on MMF would marginally improve the competitiveness of the MMF and their blended textile manufacturers in the country.
Senthilkumar has opined that the Government could have avoided imposing 2 per cent central excise duty without Cenvat credit facility or 12.5 per cent central excise duty with Cenvat credit facility on branded ready-made garments and made-ups materials priced above Rs 1,000. He has said that as the Central government is expected to implement GST in short while, the Centre could have avoided levy of central excise duty on such items. He has stated that the tariff value of ready-made garments/made-ups for the purpose of levying central excise duty has been increased from 30-60 per cent of the MRP which would marginally increase the cost for the consumers. However, SIMA chief has thanked the Government for exempting non-branded textile items below the value of Rs 1,000 from the purview of excise duty which would benefit the people below the poverty line. Senthilkumar while commenting on the various benefits extended for the skill development and job creation in the nation, has hailed EPF benefit of 8.33 per cent extended for the new entrants in the EPF. He has stated that this would significantly improve the compliance and also ensure social security of the employees. SIMA Chief has also appreciated the enhancement of limit of house rent allowance from Rs 24,000 to to Rs 60,000 which would benefit the salaried class.
CORRIGENDUM
In our previous issue of ITJ, the above write-up was tagged with a wrong picture. We regret the error.