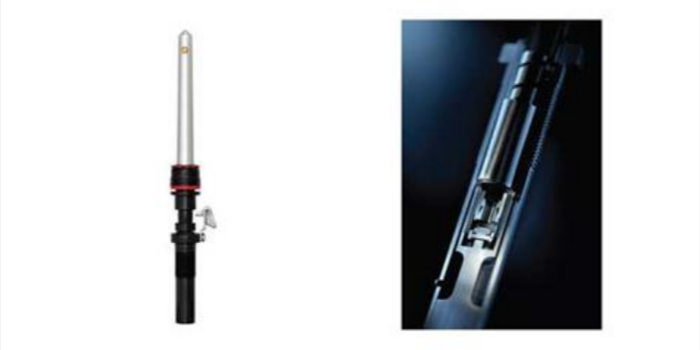
Novibra Introduces Lena
The low- energy and noise-absorbing spindle that delivers the highes speeds.
Saving energy and decreasing energy cost are
key requirements to keep spinning mills
competitive. Novibra addresses this market need
with the development of the spindle LENA –
which combines the proven Novibra spindle design with
technological optimization and further innovative
features. LENA achieves record speeds of up to 30 000
rpm while saving on average 4 to 6 per cent of energy.
Independent tests by customers using LENA showed
significant energy savings, less maintenance, and even
the added bonus of experiencing less noise.
The overall high reliability and long service life of the
spindles are decisive factors for spinning mills. Modern
spindles are expected to deliver faster speeds and
therefore increased productivity, no running-in time and
less maintenance due to long lubrication cycles. The most
important long-term goals are energy savings and the
reduction of energy costs.
Novibra fulfils the maeket needs with LENA
Novibra confirms its market leadership and leverages
its proven spindle technology to deliver on this common
need with LENA stands for Low Energy and Noise
Absorption.
LENA is the latest addition to Novibra’s spindle family
and combines the well-known, successful spindle
technology and design concepts of Novibra with new
features. Novibra’s spindle technology is characterized by
a unique hydro dynamic two-level bearing system that
effectively absorbs imbalances caused by belt tension, full
cop imbalances, traveller tension etc. The absorption of
imbalances leads to the industry’s longest operational
lifetime and high reliability.
LENAsaves energy and reduces noise thanks to technical optimizations
LENA was designed to achieve the highest speeds
with low energy consumption, achieving speeds of up to
30 000 rpm while saving on average up to 4 to 6 per cent
of energy.
For efficient noise reduction, LENA features a second
damping system. This unique and well proven Noise
Absorbing System Assembly, known from Novibra NASA
spindles, ensures minimum neck bearing load as well as
minimum vibration and low noise level at high speeds.
The LENA neck bearing diameter was reduced to 5.8
mm and thanks to the smaller bearing, the wharve
diameter could also be reduced to only 17.5 mm. From a
power transmission perspective, reducing the wharve
diameter allows the machine to be operated at a lower
speed – compared to spindles with standard wharve
diameter
– while keeping the same speed of the spindle itself
and thus the desired yarn count and twist. The small
wharve diameter of the LENA spindles is unique in the
market.
The footstep bearing unit consists of a radial and an
axial bearing. The radial bearing is designed as a
hydrodynamic plain bearing with the internal diameter
of 3 mm. It’s the small diameter of the shaft’s tip that
allows additional energy saving as the power
consumption of the radial bearing is directly influenced
by its own diameter, on top of many other factors. This
correlation has been confirmed already by a low energy
consumption of the HPS 68/3 spindles
All these optimisations make the energy savings
possible.
Customers confirm energy savings in independent tests
The main target application for LENA spindles is
spinning with tube lengths up to 210 mm at high speeds
up to 30 000 rpm. All material can be spun with LENA
and the spindle is suitable for yarn counts of Ne 30 and
finer. Many Novibra customers trust LENA spindles for
their daily production. Some of them reported their results
of their own energy saving tests.
A customer in India conducted an independent power
study after installing LENA spindles with clamping crown
CROCOdoff on a LR60/AX ring spinning machine. Polyester
and cotton were spun, with a yarn count Ne 30 and a
spindle speed of max. 20 000 rpm. The customer profited
from a power saving effect of 6.5 per cent thanks to LENA
as well as a reduction of yarn breakage during the start-up
of the machine. An additional observation was that the
incidence of low twist yarn was eliminated after
installation of the Novibra spindles.Another valued customer in India compared the overall
energy consumption using LENA spindles and reported a
saving effect of 4.6 per cent per machine after the
installation of LENA spindles on a LR6/S ring spinning
machine with manual doffing. Their trial was performed
with cotton, yarn count Ne 60 and the spindle speed wentup to a maximum of 22 700 rpm.
Installation and options
The installation of LENA requires only a small change
in the machine settings, making the spindle
commissioning fast and easy. LENA spindles can be
equipped with state-of-the-art cutting and clamping
crowns (e.g. CROCOdoff). CROCOdoff enables
underwinding-free doffing which significantly reduces its
maintenance and optimizes the automation of spindle
operation. Crocodile-like teeth ensure dependable clamping
and cutting of the yarn while doffing and reduce the
number of after doff end downs.
This shows that LENA spindles significantly contribute
to energy savings during ring spinning and a lower noise
level in spinning mills – even at the highest spindle speeds
– thanks to various technological optimizations.
Novibra is the only manufacturer in the world that
offers spindles with a wharve diameter as small as 17.5
mm. Unmatched expertise and in-depth experience allow
Novibra to launch innovative products such as LENA,
delivering significant improvements over conventional
spindles and keeping our customers at the forefront of
their industry.
For further details please visit www.novibra.com