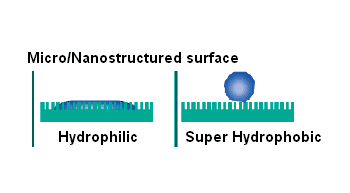
Nanofinish in textile: An emerging technology
The use of nanotechnology in the textile industry has increased rapidly due to its unique and valuable properties, affirm Tanveer Malik and TK Sinha. Finishing is the final step in the fabric manufacturing process, the last chance to provide the properties that customer will value.
The use of nanotechnology in the textile industry has increased rapidly due to its unique and valuable properties, affirm Tanveer Malik and TK Sinha.
Finishing is the final step in the fabric manufacturing process, the last chance to provide the properties that customer will value. Finishes give it special functional properties including the final ´touch´ & nanotechnology is one of the emerging technologies used for textile finishes. Nanotechnology is an umbrella term covering a wide range of technologies concerned with structures and processes on the nanometer scale.
Nanotextiles are broadly classified as: Nanofibres: Nano clay used in textiles, intelligent clothing, sensors; Easy care: Hydrophobic Nano Finish is mainly used for cotton fabric, so that the fabric will posses water repellent property by creating nano whiskers; Self cleaning effect: In this property water droplets which falls onto fabric, bead up and if the surface slopes slightly, will roll off, keeping the fabric surface dry even in heavy shower; UV-protection: It is used for furnishing fabric such as car seat covers because they are generally, exposed to sunlight for longer duration;
Anti-bacteria: With the help of organic and organo metallic compounds fabric is given antibacterial finish; Photocatalysis: This finish develops a property which is capable of killing bacteria, cleaning water and even splitting water to give hydrogen and oxygen, which helps in preserving original touch of fabric; Nano-Dry: It is a hydrophilic finishing technology which is generally used for polyester and nylon synthetic garment, which gives breathability to fabric; Nano-Touch: The ultimate finishing technology which gives superior refinement in blended fabric; and Easy care-hydrophobic nano finish: Hydrophobic surfaces can be produced mainly in two ways (i) by creating a rough structure on a hydrophobic surface (ii) by modifying a rough surface using material with low surface free energy. Both the approach has been used to give a hydrophobic finish to textile substrates.
The water-repellent property of fabric by creating nano-whiskers, which are fluorocarbons and 1/1000 of the size of a typical cotton fibre, that are added to the fabric to create a peach fuzz effect without lowering the strength of cotton. Thus a rough hydrophobic layer is formed. Fluorocarbons are a class of organic chemicals that contains perfluroalkyl residue in which hydrogen atom have been replaced by Fluorine. These chemicals have very high thermal stability and low reactivity.
Super hydrophobicity: Hydrophobic fluorocarbon finishes as stated above lower the surface energy and can give a maximum water contact angle of roughly 120.To get higher contact angle and to have self-cleaning ability, super-hydrophobic finish with a contact angle of above 160 is required. This type of finish can not be obtained by surface coating. Super hydrophobic increase in surface roughness provides a large geometric area for a relatively smack projected area. The roughened surface generally takes the form of a substrate member with a multiplicity of micro scale to Nanoscale projections or cavities. Water repellency of rough surface was due to the air enclosed between the gaps in the surface. This enlarges the air /water interface while the solid/water interface is minimised. In this situation, spreading does not occur the water form a spherical droplet.
Self cleaning effect using silver nanoparticles: A highly water-repellant coating made of silver nanoparticles that can be used to produce suits and other clothing items that offer superior resistance to dirt as well as water and require much less cleaning than conventional fabrics. Na