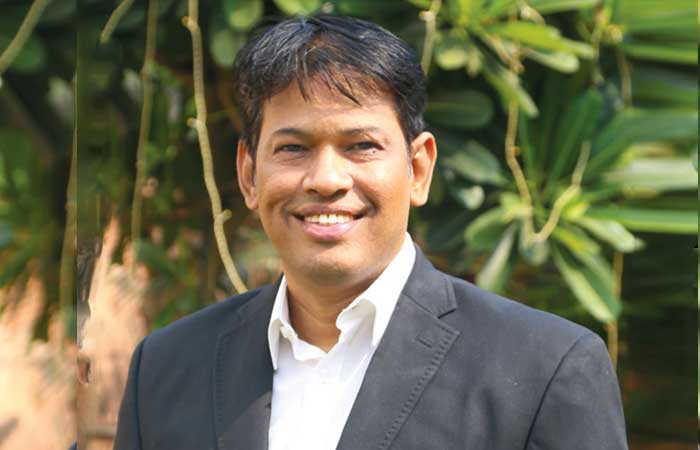
MMFs can be engineered to mimic the look and feel of natural fibres
Perfect, founded by technocrats four decades ago, is still driven by a firm mission for technological and engineering excellence. Perfect has shot into the international market thanks to its unwavering commitment to rigorous quality standards and ongoing innovation, making it the preferred supplier of top multinationals in the global textile arena. B Sankar, G M of Technical and Development at Perfect Engineering Corporation, discusses the reasons behind the growing popularity of synthetic fibre spinning in an interview with Divya Shetty.
How is the spinning of synthetic fibres, particularly MMF (Man-Made Fibres), gaining traction in today’s textile industry?
The spinning of synthetic fibres, notably Man-Made Fibres (MMF), is experiencing a surge in the modern textile landscape due to several compelling factors. MMFs, such as polyester, nylon, and acrylic, offer a plethora of advantages over traditional natural fibres like cotton or wool. They are highly versatile, boasting properties like durability, moisture-wicking abilities, and resistance to wrinkles and shrinkage, making them ideal for a wide range of applications. Moreover, MMFs can be engineered to mimic the look and feel of natural fibres, providing designers and manufacturers with immense creative freedom.
One significant driver behind the growing popularity of synthetic fibre spinning is its cost-effectiveness. MMFs can be produced at a lower cost compared to many natural fibres, making them an attractive option for businesses looking to optimise their production processes without compromising on quality. Additionally, the consistency in quality and availability of MMFs further enhances their appeal to textile manufacturers, ensuring reliable sourcing and production schedules.
Furthermore, the rising demand for performance-driven textiles in various sectors such as activewear, technical textiles, and automotive textiles has propelled the adoption of synthetic fibres. These industries require materials that offer enhanced functionality, such as moisture management, UV protection, and abrasion resistance, all of which are inherent characteristics of many MMFs.
In summary, the spinning of synthetic fibers, particularly MMFs, is gaining traction in today’s textile industry due to their versatility, cost-effectiveness, and ability to meet the evolving demands of modern consumers and industries.
With awareness and concern on ecofriendly and earth saving the use of recycled fibre for staple fibre spinning getting attention and MMF fibre assist for better spinnability of recycled fibres.
Which segments of the textile industry are utilising synthetic yarns the most, and what factors contribute to their preference for synthetic fibres?
Synthetic yarns have found widespread utilisation across various segments of the textile industry, with some sectors exhibiting a particularly high demand for these versatile fibres. One of the primary segments driving the consumption of synthetic yarns is the apparel industry, encompassing casual wear, sportswear, and outerwear. The performance characteristics of synthetic fibres, such as moisture-wicking properties, durability, and stretch ability, make them indispensable in the production of active wear and athleisure garments.
Another key sector leveraging synthetic yarns is the home textiles market, including bedding, upholstery, and curtains. Synthetic fibres offer superior resistance to fading, staining, and wrinkling, making them well-suited for applications where durability and easy maintenance are paramount.
The automotive textiles industry also heavily relies on synthetic yarns due to their ability to withstand harsh environmental conditions and frequent use. From seat covers to carpets, synthetic fibres enhance the longevity and performance of automotive interior components.
Several factors contribute to the preference for synthetic fibres in these segments. Firstly, the affordability and consistent quality of synthetic yarns make them an attractive option for manufacturers seeking cost-effective solutions without compromising on performance. Additionally, the versatility of synthetic fibres allows for the creation of innovative textile products that cater to diverse consumer needs, driving demand across different market segments.
Furthermore, the increasing emphasis on sustainability and eco-friendliness in the textile industry has prompted manufacturers to explore alternative materials such as recycled synthetic yarns. By incorporating recycled polyester or nylon fibres into their products, companies can reduce their environmental footprint while meeting consumer demand for sustainable textiles.
Overall, the versatility, performance, and sustainability credentials of synthetic yarns contribute to their widespread utilisation across various segments of the textile industry.
What do synthetic yarn and synthetic fibre manufacturers envision for the future of their industry, considering advancements in technology and changing consumer preferences?
Synthetic yarn and fibre manufacturers are optimistic about the future of their industry, fuelled by advancements in technology and evolving consumer preferences. One of the key trends shaping the future of synthetic fibres is the increasing focus on sustainability and circularity. Manufacturers are investing in research and development to innovate new recycling technologies that enable the conversion of post-consumer waste, such as plastic bottles and discarded textiles, into high-quality recycled synthetic yarns.
Moreover, the advent of smart textiles and functional fibres is opening up new avenues for growth and innovation in the synthetic fibre industry. By integrating technologies like embedded sensors, conductive yarns, and phase-change materials, manufacturers can create textiles with enhanced functionalities such as temperature regulation, health monitoring, and interactive capabilities.
Furthermore, customisation and personalisation are becoming increasingly important in the textile market, driven by consumer preferences for unique and individualised products. Synthetic fibre manufacturers are leveraging advanced manufacturing techniques like 3D printing and digital textile printing to offer customisable solutions that cater to the diverse needs and preferences of consumers.
Additionally, the rise of e-commerce and digital platforms is reshaping the supply chain and distribution channels in the textile industry. Synthetic fibre manufacturers are adapting to these changes by embracing digitalisation and investing in online platforms to connect directly with consumers, streamline production processes, and optimise inventory management.
Overall, synthetic yarn and fibre manufacturers envision a future characterised by sustainability, innovation, and digitalisation, where advanced technologies and changing consumer preferences drive continued growth and evolution in the industry.a sustainability and eco-friendliness in textile production by adopting innovative approaches to recycling and circularity. One of the most significant initiatives undertaken by these manufacturers is the development of recycled yarns derived from post-consumer waste materials.
Advanced recycling technologies enable synthetic fibre manufacturers to reclaim and process materials such as discarded polyester garments, plastic bottles, and industrial waste, transforming them into high-quality recycled yarns. These recycled yarns offer the same performance characteristics as virgin fibres but with a significantly reduced environmental footprint, contributing to the circular economy and mitigating the impact of textile waste on the environment.
Moreover, synthetic fibre manufacturers are collaborating with partners across the value chain, including brands, retailers, and recycling facilities, to establish closed-loop systems that facilitate the collection, sorting, and recycling of textile waste. By incentivising consumers to participate in recycling programs and offering incentives for returning used garments, manufacturers can ensure a steady supply of recycled materials for the production of sustainable textiles.
In addition to recycling, synthetic fibre manufacturers are exploring alternative sources of raw materials, such as bio-based polymers derived from renewable sources like plant-based feedstocks. These bio-based fibres offer similar performance characteristics to traditional synthetic fibres but with a lower carbon footprint and reduced dependency on finite resources.
Furthermore, advancements in chemical recycling technologies hold promise for the future of sustainable textile production. These innovative processes enable the breakdown of complex polymer structures into their constituent monomers, which can then be used to produce new fibres without degradation in quality or performance.
Overall, synthetic fibre manufacturers are embracing sustainability as a core pillar of their business strategies, leveraging recycling, bio-based materials, and technological innovations to meet the evolving demands of eco-conscious consumers and drive positive change in the textile industry. The advancement in technological development for mechanical recycling of cotton hard waste lead to reclaiming the best quality cotton fibers enable to mix the recycled cotton fibers along with virgin cotton.
How is Perfect Engineering Corporation contributing to the growth of synthetic fibre spinning?
Traditionally, recycled yarn production relied heavily on PET bottle and virgin polyester fibers. However, with enhancements in recycled fibre parameters, Perfect Engineering Corporation has expanded its use of recycled fibres beyond synthetic materials to include cellulosic fibers. This diversification not only broadens the scope of materials suitable for recycling but also promotes greater environmental sustainability by reducing dependence on virgin resources.
Furthermore, Perfect Engineering Corporation is focused on manufacturing wider width cards, capable of handling up to 2.5 metres, to facilitate the production of non-woven technical fabrics. These fabrics, predominantly composed of synthetic fibres, play a crucial role in various applications across industries. By enhancing manufacturing capabilities in this area, the company is supporting the demand for high-quality technical fabrics while also driving innovation in synthetic fibre spinning.
In summary, Perfect Engineering Corporation’s commitment to technological advancement, sustainable practices, and product diversification underscores its significant contribution to the growth of synthetic fibre spinning and the broader textile industry.