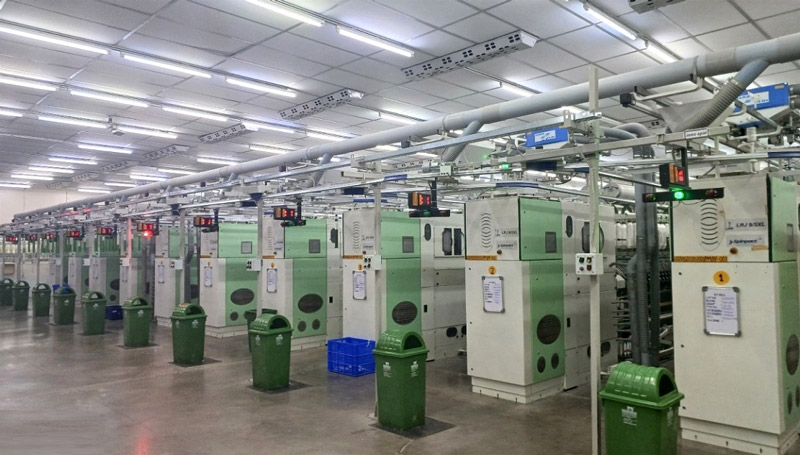
LMW & Gimatex: Flourishing partnership for spinning success across applications
LMW has recently completed the commissioning of a 30,000 spindles project at their Bela facility dedicated to processing cotton, viscose, and blends (P/C, P/V) applications.
The long-standing partnership between LMW and M/s. Gimatex for over three decades has not only weathered the tests of time but has also evolved with the changing dynamics of the industry. LMW has recently completed the commissioning of a 30,000 spindles project at their Bela facility dedicated to processing cotton, viscose, and blends (P/C, P/V) applications. Concurrently, the next expansion project with 30,000 spindles at the same location is under supply for cotton and blends application.
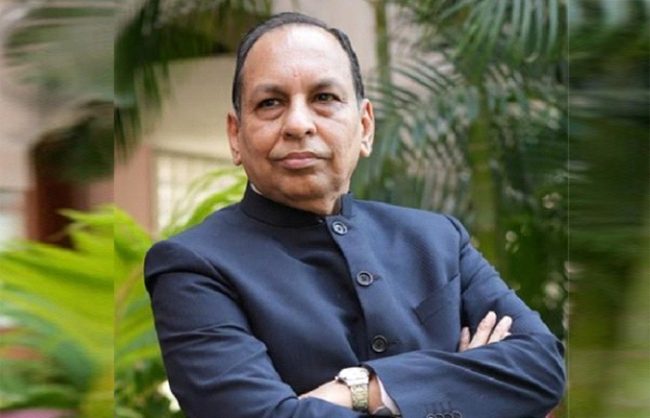
Gimatex, a business conglomerate with a rich heritage of over 125 years (dates back to RSR Mohota Mills in the year 1898) is today a completely integrated textile facility from ginning to apparel (ginning, spinning, weaving, processing, and apparels).
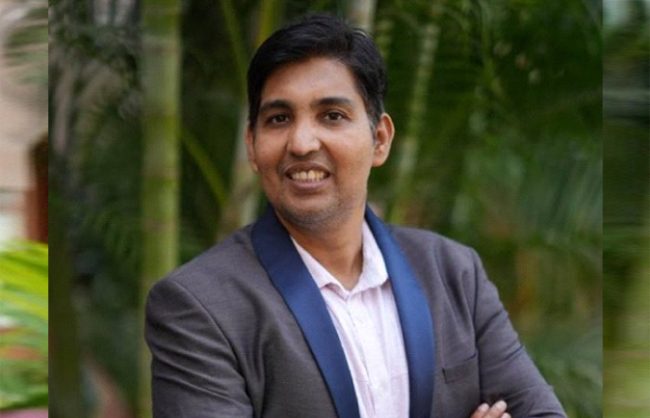
In operation since 1996 with 25,000 spindles, today the company has grown significantly to a capacity of more than 2,00,000 spindles and 960 airjet spindles with modern production and testing facilities strategically distributed across Hinganghat, Wani and Bela cities of Maharashtra that deliver superior total value to the customers.
Versatile solutions compatible with a plethora of applications
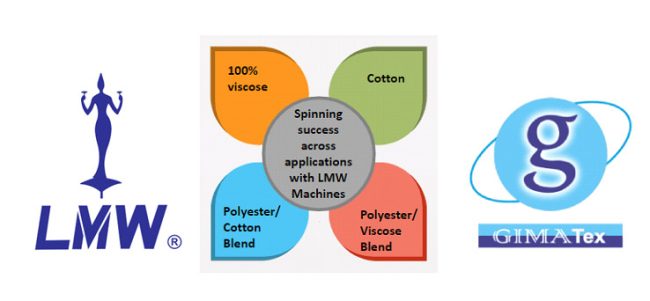
The versatile smart series machines from LMW, compatible with a diverse range of raw materials, including regenerated fibers, are a testament to sustainability and circularity in the field of spinning. The commissioning of several units with 100 per cent LMW machinery, processing a varied range of counts from 20’s to 40’s for Cotton, Blends (P/C, P/V) and 100 per cent Synthetic (100 per cent viscose) applications stands as a testimony to the reliability and adaptability of LMW solution offerings in meeting the evolving production requirements of Gimatex.
LMW and Gimatex, enduring partnership thriving within an environment of mutual trust
The state-of-the-art facility at Hinganghat houses 100 per cent LMW machines with 25000 spindles capacity for processing polyester and viscose applications (Grey and Dyed). The Airjet looms at the facility are also equipped with smart preparatory machines from LMW.
At the facility in Wani, two units are equipped with 100 per cent LMW smart solutions for processing P/V, P/C and 100 per cent viscose application, operating with 11,000 spindles capacity each. The unit – 3 at this facility with 11,000 spindles capacity is equipped with state-of-the-art solutions from LMW for preparatory spinning and Unit – 4 is facilitated with LMW Smart Ring frames for 25,000 spindles capacity.
Smart Compact Ring frame LRJ 9/SXL
The installations (completed & ongoing), at Bela includes 4 units wherein unit – 1 & 2 are operating with A – Z state-of-the-art smart series machines from LMW at 30,912 spindles capacity for processing cotton and viscose materials. The machinery lineup at the Unit – 1 & 2 include,
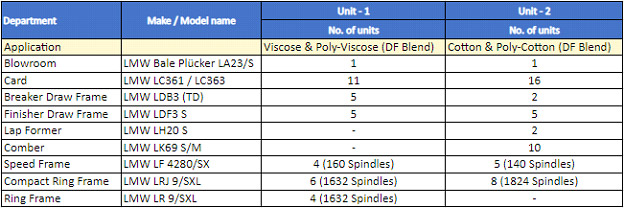
The Unit – 3 & 4, at Bela facility with 30,912 spindles for processing cotton and blends application are currently under execution with end-to-end LMW solutions. The machinery lineup at this facility comprises of
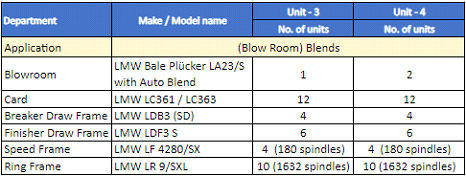
The preparatory machines from LMW for cotton at this facility includes,
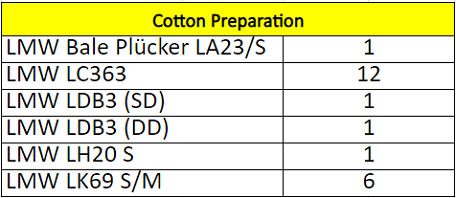
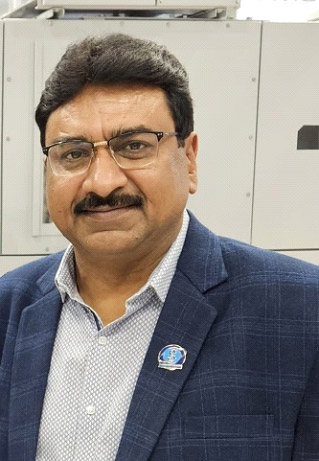
Ashwani K. Gupta, President (Spinning)
The new generation machines from LMW are built to enable remote monitoring, remote diagnosis, and real-time data analysis to ensure spinning mills thereby making real-time spinning machinery data part of strategic decision-making process.
Additionally, LMW’s machines are equipped with higher efficiency motors and reliable components, minimizing power consumption and contributing to sustainability goals. Real-time service support provided by LMW ensures longer machine uptime, enhancing reliability and the longevity of machine parts.
(Plant technical team)
The enhanced productivity, coupled with consistent quality, power efficiency, reduced manpower requirements and costs, minimized waste, and various other advantages, guarantee a swift Return on Investment (ROI) for the deployed capital. This accelerated ROI is achieved within a short timeframe, empowering the customer to achieve success in their spinning endeavors.
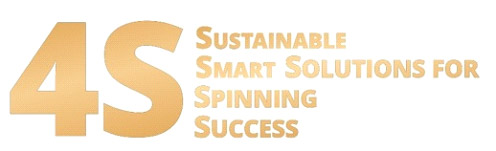
LMW’s Sustainable Smart Solutions for Spinning Success (4S), supported by a culture of innovation, empower mills with a technological and competitive advantage. This is achieved through mission-critical automation, real-time data, analytics from connected machines, compatibility with all applications, and reliable performance under diverse operating conditions.