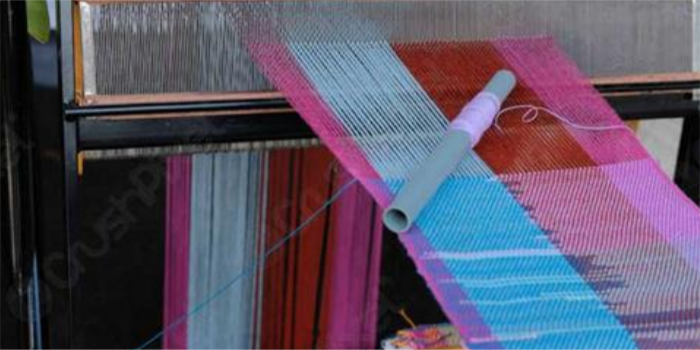
Indian weaving industry on the growth path
In this article, Sanjay Arora highlights the current status of the Indian weaving industry in terms of production, capacities, fabric demand and emerging trends.
The textile industry plays a crucial role in Indian economy. It contributes to 7% of industrial output in terms of value, 2% of the GDP and 12% of country’s export earnings. Next to agriculture, it is the second largest employment generating industry in India, employing approximately 45 million people directly. There are around 1,600 spinning mills, 4 lakh weaving units, 50,000 knitting units, 5,000 processing units and 71,000 garmenting and made-ups units in India. Majority of the production happens in decentralised sector in various clusters across India some of which are vertically integrated.
India has the largest installed base of weaving in the world with approximately 5 million looms. The capacities are growing owing to adequate supply of raw material and manpower. The Indian weaving industry is globally known for its handmade fabrics thriving its cultural heritage.
Overview of the Indian weaving industry
India accounts for 64% of the globally installed capacity of looms with approximately 2.3 million handlooms, 2.52 million power looms, and 0.13 million shuttleless looms. Almost 95% of the fabric production happens in the decentralised sector comprising of power looms and handlooms. There are 4 lakh weaving mill in India with Maharashtra having the highest share (37%) followed by Tamil Nadu (22 %) and UP (15%). This sector provides direct employment to about 9 million people with powerloom sector contributing 4.8 million, handloom sector 4.1 million and shuttleless looms sector 0.1 million jobs.
Figure 1: Loom types
|