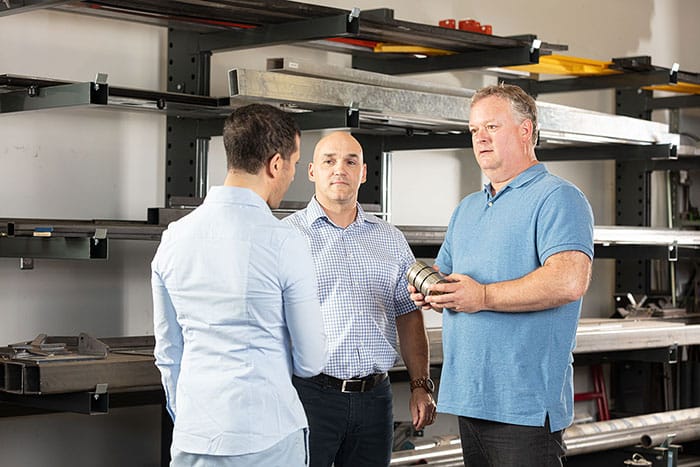
ITA SmartMill: A fully digitalised spinning mill for innovative and sustainable fibres
Through a step-by-step, iterative further development of sensor technology, data storage and data processing, an innovation space is being created at the ITA with the SmartMill that demonstrates the potential of digitalisation for yarn production.
The potential of digitalisation and sustainable production in the textile industry is still partly untapped and can be explored using the innovation space of the ‘SmartMill,’ a fully networked spinning mill that combines digitalisation and the circular economy. The innovation space serves as a model factory for interconnected textile production, enabling monitored production from fibre to yarn. The implementation of the SmartMill follows a seven-step approach, incorporating sensor technology, data analysis, and dynamic control loops. After and during the implementation the gathered data can be used to demonstrate the digitalisation potential in yarn production as well as advance sustainable textile development.
Introduction
Digitalisation and the production of sustainable or recycled textiles are two global megatrends that have not been focused on in the textile industry in recent decades. Here, however, the economic innovation potential of sustainable production and a circular economy for clothing and other textiles is enormous. On the one hand, the pressure to innovate is increasing for the textile industry, while on the other hand, opportunities are arising for the development and marketing of new textiles and the technologies needed to produce them. For the core spinning technologies, such as ring and rotor spinning, the state of the art is already well researched with the means of conservative mechanical engineering. Many processes are automated or monitored by sensors, although the process data from the sensors used are used in isolation and not collected to draw conclusions about the overall process.
In the following, a possibility is shown to address topics of digitalisation and the circular economy in parallel by setting up the cross-process innovation space ‘SmartMill’ and uncovering synergies. The SmartMill is a digitalised and fully networked spinning mill with spinning preparation, which is currently under development and is to be set up as a demonstrator at the Institute of Textile Technology. The Institute of Textile Technology (ITA) at RWTH Aachen University combines research along the entire textile process chain, from fibre production to the textile surface, under one roof and also has expertise in the area of digitalisation. This provides excellent conditions for tapping unused potential.
Current state of the digitalisation within the textile industry
In order to be able to manage the earth’s raw materials sustainably, innovative and sustainable fibres must be considered as a raw material for the textile industry of the future. An alternative to cotton as a conventional natural fibre for clothing is hemp and flax, which require less water and pesticides in comparison. In addition, the use of fibres from agricultural or consumer waste offers an opportunity to reduce CO2 emissions, as these fibres would otherwise only be used for the production of energy. However, the processing possibilities of these fibres differ in part from the processing of cotton to such an extent that modified or basic production technology and adapted process parameters have to be developed.
One possibility to identify suitable process parameters lies in the sensor-based monitoring of the textile process chain. Many process steps between the fibre material and the yarn are already equipped with sensors that record process properties online. For example, in the regulating draw frame, the unevenness of the sliver is recorded and used to dynamically adapt the drawing to the unevenness of the sliver. This control loop can be used to reduce the unevenness of the sliver. Likewise, each yarn produced is checked for intolerable thin and thick spots in the yarn either directly at the spinning position or during rewinding and these are automatically removed from the yarn. The sensor technology applied also detects imperfections and quantifies the non-uniformity. This gives the yarn manufacturer an overview of the quality of the yarn produced. However, the textile machines commercially available at the moment are limited to this monitoring only and neglect the potential of a cross-process analysis of the data collected anyway.
Vision for the SmartMill
Using the SmartMill innovation space, it will be demonstrated how the potential of networked textile production can be scientifically identified step by step and how ecological and economic advantages can be used. This addresses the megatrends of digitalisation and sustainability simultaneously. The innovation space enables monitored production from fibre to yarn at ITA, which serves as a model factory for interconnected textile production on a laboratory scale for a quantity of a few grams to 10 kg at a time. Figure 1 shows the concept for the material, signal and information flows in the SmartMill innovation space, which can be used for cross-process analysis.
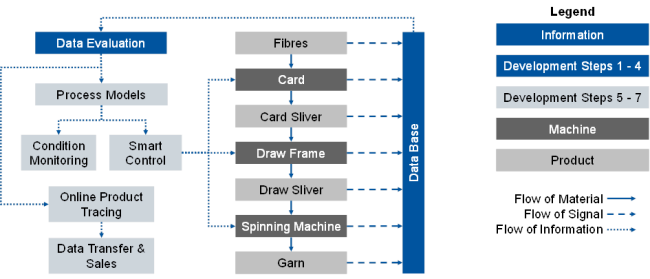
Concept for material, signal and information flows in the SmartMill innovation space
Within the scope of the innovation space, an infrastructure for a wide variety of research questions is generated through the digitisation across machines. Two examples of current research issues that build on the implemented digitisation of the machines are given below.
Possible research issue I: Digitalised yarn
In current research, a distinction is made between the digital twin and the digital shadow. While the digital twin describes its physical original as accurately as possible, the digital shadow is limited to the level of detail required for the application. The core of the digital shadow lies in a reduction of the information to the essential in each case and thus in an efficient performance for a chosen application. Before the digital shadow can be designed, in the case of the SmartMill, a digital twin is created for the yarn for research purposes. This “Digital Yarn” contains all the information about the yarn recorded from the beginning to the end of the process in relation to the run length and thus enables tracking across all process stages. This means that data exists on past states and process steps as well as on the current state. With the help of this data, correlations can be made between anomalies and their past causes. It is also possible, for example, to model and simulate the future process steps and states of the yarn in the area in order to predict problems in the process and faults in the area. Data is used to create value. In the long term, this makes it possible to decide which information about the yarn is relevant, so that the digital twin of the yarn can be converted into a digital shadow.
Possible research issue II: Process modelling
If a model describes a process sufficiently well, it establishes a mathematical relationship between different process variables. With the help of the correlation, predictions for output variables can then be derived by specifying input variables (e.g. sensor values). A common application of a model that describes a production process is the development of a control concept. The behaviour of the modelled system is simulated with the help of the model and the control loop is designed in this way. Another application of process models are soft sensors. Soft sensors generate values for process or product variables that cannot be measured directly using sensors. These models are used for quality control, for example in control engineering or in condition monitoring, where conclusions about wear are drawn by means of deviations between model and reality. For the pure calculation of the underlying values, the type of model is irrelevant as long as it is accurate enough. While physical models that describe the process by simple formulae or equations work most efficiently, data-driven solutions such as neural networks, on the other hand, often require greater computing capacity. Nevertheless, data-driven solutions are becoming increasingly interesting for various applications due to the constantly increasing computing power. In the scope of SmartMill, process modelling can be carried out on the basis of both physical and data-driven models. This identifies which type of model offers advantages for which application.
Approach for implementing the SmartMill
In order to implement the complex and extensive version of SmartMill, an iterative approach is chosen, which is iterated through. The implementation is based on the Industrie 4.0 Maturity Index and the 4 stages of Smart Factory, which are combined to form a 7-stage approach to implementation.
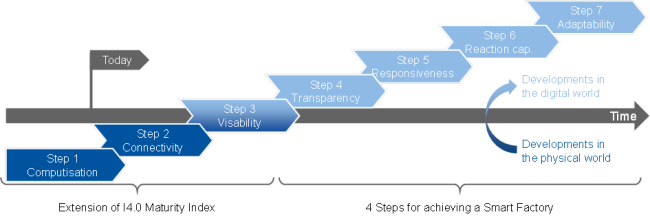
Seven-step approach to implementing the SmartMill
In the first stage, the individual process parameters are digitally recorded and the necessary sensors for comprehensive data acquisition from the machines are implemented at the ITA. In the second stage, all data is compiled online in a data lake and in the third stage, their interdependencies are presented. In stage four, causal relationships behind the correlations are searched for and process models are then created from the findings. In stage five, the physical infrastructure is enabled to intervene dynamically in the process via actuators, while in stage six, models are created that enable prediction of future errors. The predictions can already be made available to the operator as an aid. Finally, the same models are used in stage seven to react to and prevent the errors with the help of the previously created dynamic control option. The realisation of stage seven thus forms an intelligent factory that independently detects errors, makes decisions and actively intervenes in its processes.
Conclusion
Through a step-by-step, iterative further development of sensor technology, data storage and data processing, an innovation space is being created at the ITA with the SmartMill that demonstrates the potential of digitalisation for yarn production. At the same time, developments are required in the field of sustainable textiles, which can also be addressed within the scope of the SmartMill. The innovation space of the ITA SmartMill allows the agile development of production technology and process parameters and the use of small amounts of raw materials, as data is already recorded during the processing and made usable for improving the process behaviour. In this way, the transformation to sustainable textiles is shaped.
Acknowledgement
Funded by the German Research Foundation (DFG) as part of the Excellence Strategy of the Federal Government and the Länder – EXC-2023 Internet of Production -390621612.
About the author:
Lanfer Pierre is the Researcher of the Institut für Textiltechnik of RWTH Aachen University, Germany.
Kühn Justin is the Researcher of the Institut für Textiltechnik of RWTH Aachen University, Germany.
Lechthale Lukas is the Head of Staple Fibre Technology at the Institut für Textiltechnik of RWTH Aachen University, Germany.
Gries Thomas is the Director of the Institut für Textiltechnik of RWTH Aachen University, Germany.