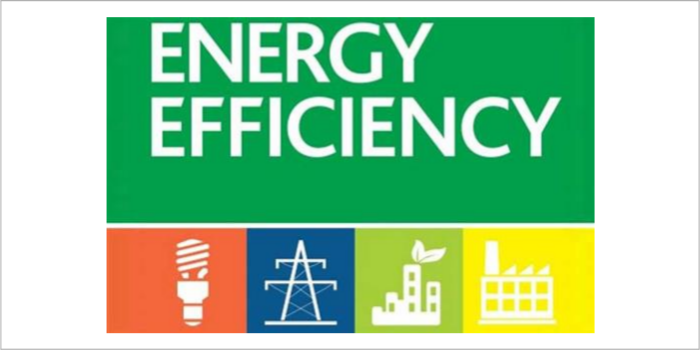
Improved energy efficiency with Edge Controller
Edge Controller, a powerful factory automation solution from B&R makes it possible to have complete command over textile process chain.
Textile is an energy intense industry with strong focus towards producing highest quality product and staying competitive. Textile industry perform series of operation to produce finished yarn from raw cotton. It is a fragmented and heterogeneous sector dominated by SMEs. Textile manufacturing is characterised as complex chain because of usage of a wide variety of processes, machinery and components with different types of raw material, methods of fabric production, and finishing process, which are all interrelated in producing a complete fabric. When one of these components is disrupted, properties of product are affected. Moreover, in a cost sensitive market optimising production and becoming more efficient is the need of the hour.
Textile industry has started perceiving the need of saving energy in entire production process, which indirectly counts to efficiency and improving profits. Textile is an energy intensive industry with a mix of manual labor, semi-automatic systems, modernised equipment and continuous usage of equipment. Processes such as ginning, spinning and weaving employs different type of machines and electrical systems at various stages. The energy consumed by automated machines holds a majority share of total energy consumed in the factory. With higher energy cost accounting to around 15 % of overall production cost can be relatively compared to cost of raw material. Therefore, over the years, textile-manufacturing setups are focused on energy optimisation and are consistently looking for implementing energy monitoring measures to optimise and bring down energy costs.
Energy monitoring gaining traction with smart factories
A textile-manufacturing unit utilises energy from various sources such as electricity, natural gas, heaters, chillers, air, water etc. Increased demand increases the demand for keeping production running 24/7. Thus, offering a higher impetus on energy conservations and optimisations. Evaluating energy consumption at all major stages in yarn production is important to identify energy patterns. In addition auxiliary process such as weaving, dyeing, coating are using heaters, coolers, steam, water, compressor and utilities that account for additional energy consumption, which typically goes un-noticed. It adds to the challenge of factory operators to streamline all energy sources and monitor seamlessly within a single system.
Edge Controller, a powerful factory automation solution from B&R makes it possible to have complete command over textile process chain. With EnMon (Energy Monitoring) solution, an integral part of Edge Controller, it enables factory operators to measure, record and evaluate all relevant energy parameters across textile process in real time providing optimal support for continuous improvement of process. The system can monitor energy that are utilised in various form such as electricity, thermal, gas, compressed air, steam and waste management. The measured data gives power to factory operators to devise a strategy to optimise process design and meet energy demands while reducing operating costs.
With an efficient energy monitoring system, textile lines can ensure maximum utilisation of manufacturing capacity, identify key energy sources, fine tune machines, equipment, processes, and adopt best energy saving practices. Energy data allows factory owner to structure a systematic approach to minimise energy losses and identify deviations. The system provides energy data using intuitive reports and trends that makes it possible to visualise abnormal symptoms in inefficient energy usage in textile manufacturing facility. B&R EnMon solutions enables collection of energy data from weaving, combing, and spinning line in runtime and calculates load distribution within the plant. The collected data is analysed and a base line is identified to get best possible energy conservation opportunity. The analysis of EnMon reports provides optimal support for reducing energy costs by avoiding peak loads and preventing unplanned outages.
Edge Controller extends support for energy audit
Textile industry has started performing energy audit to have constant check on energy flow. EnMon solution rightly supports factory owners to perform audits by providing them with real time energy consumption data of the process. It considerably simplifies the implementation of energy management tasks set up in connection with ISO 50001 and EN 16001 standards. The flexible Edge Controller extends support for audit process from energy to air, water, lighting, load and condition based performance monitoring. Factories can use existing automation controller to process measured values eliminating need of a dedicated controller that usually adds complexities in plants. Energy monitoring solution is equipped with libraries and function blocks that are used for processing and analysing measured values in real time. The historical records indicates usage pattern and helps identify any surge in energy consumption. This assists factories to take necessary measures in optimising energy usage and making way for efficient manufacturing in textile industry. With Edge Controller, textile industry is able to not only perform continuous energy monitoring tasks but also enhance line health, prolong its life, reduce downtime, wear & tear and ultimately improve profitability using a single system.
Process control and monitor using single system
Machines coupled with modern instrumentation makes it possible to record, determine and assess the condition of critical parts continuously with a high degree of precision. With ConMon (Condition Monitoring) solution which is a core component of Edge Controller, B&R offers a pre-installed and pre-configured package that makes implementing condition-based maintenance more straightforward than ever. It helps identify potential sources of malfunction and damage in advance so that maintenance team schedules corrective action. The mean time for maintenance can be reduced to considerable length and improve health of overall textile lines. Integrated PDA (Process Data Acquisition) features from Edge Controller make it easy to manage operational and production data for machinery and plants seamlessly in a central location. Data from machines are collected using open protocols such as OPC UA and MQTT that adds a transparency to the process. It can significantly handle rapidly growing volumes of data to keep pace with demands of modern textile production. Thus, based on the needs of any textile factory the Edge Controller can be easily scaled to fit the needs of the factory.
Edge Controller provides synergy for profitable future
Apart from losses due to unplanned shutdowns, energy is another main contributor to costs in textile industry. Especially in times of energy price volatility, improving energy efficiency is one of the main concerns of textile industry. Energy monitoring solution provides various opportunities to identify energy intensive and energy efficient areas in manufacturing. Moreover, majority of textile plants in India are SMEs or MSMEs, where there is always a challenge in making an additional investment for specialised energy monitoring solution. With B&R, Edge Controller proves to be a single system for controlling processes, monitoring energy, condition based monitoring of assets and handling data for process optimisation. The scalable hardware and powerful software helps textile industry to focus more on innovation while reducing operational cost and become profitable.
Pic caption: