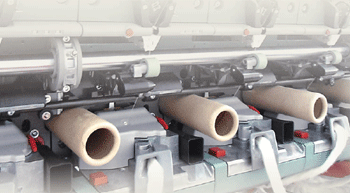
First R 35 rotor spinning machine in India: Customer calculates the benefits
The recently introduced R35 semi-automated rotor spinning machine, known as a smart and economic solution to increase productivity, has arrived in India. The R35 impresses the Indian rotor spinners with its ergonomics, productivity, the AMIspin-piecing technology and its flexibility.
The recently introduced R35 semi-automated rotor spinning machine, known as a smart and economic solution to increase productivity, has arrived in India. The R35 impresses the Indian rotor spinners with its ergonomics, productivity, the AMIspin-piecing technology and its flexibility.
The first R35 rotor spinning machine in India was commissioned at Saranya Spinning Mill Pvt Ltd in Namakkal (Fig.1). This spinning mill already has experience with the former R923 model and evaluates the innovations of the R35 as distinctive advantages.
The new R35 semi-automated rotor spinning machine has up to 500 spinning positions. It allows rotor speeds up to 1,20,000rpm and delivery speeds of 200m/min and that at full machine length. The new S35 spin box improves spinning and makes the work for the operator easier, so that optimal yarn quality is reached. The new electronic yarn traverse enables settings including winding width, winding angle and edge displacement to be made over a wide range to give more options for optimising package quality.
The design of the R35 is intended to make this machine the new workhorse for all applications where maximum cost efficiency and long-term performance are required.
Easier operation and higher output
At Saranya mill, the R35 produces a woven cotton yarn Ne20 using a blend with 15per cent virgin fibres. One of the first positive impressions of the operators at Saranya was the easier handling of the spin box (Fig. 2). The optimised opening area of the spin box provides ideal conditions for cotton fibre opening, with positive benefits in yarn properties. The modified feeding area prevents unintended damage to the sliver. This new design of the S35 spin box ensures better spinning stability, even with low-grade blends. Already after a brief running-in period, the operators at Saranya observed significantly lower end down rates on the R35, while at the same time the rotor speeds were 3 per cent higher than on the R 923.
Added value with excellent piecing quality
The AMIspin device for excellent piecing quality has been further developed. It is now more independent of the operator. Saranya noted that thanks to the new arrangement of the yarn path, handling of the AMIspin piecing process has become even easier and up to 10per cent more successful.
The software for the feed roller in the new spin box optimises the piecing sequence. Saranya reports higher strength and excellent appearance of the piecings. This quality also means added value for the downstream processors of the yarns. As a result, the machine efficiency of the new R35 is up to 1.5per cent higher compared to the R923 running with the same application.
Quality check for yarn and piecings
For the R35, the new Rieter Q10 yarn clearer is optionally available. The Q10 is fully integrated into the machine control system. All settings, quality data and the actual status of machine ad spinning position are displayed on the operating panel of the machine.
Compared to the previous model, the Q10 provides more detailed settings for all basic yarn faults (N-S-L-T). It gives rapid response to sliver weight variations, which is especially important in the case of the short spinning process using card sliver.
Easier operation & maintenance
Saranya names even further additional benefits of the new R 35:
The setting with the large, graphic machine display is convenient. The information shown is clearly structured. When necessary, an electronic printout can be very easily made by means of the USB interface.
The redesigned suction system with a new trash collection chamber is easier to operate. The main fan with frequency converter drive enables an optimation of the suction. In addition